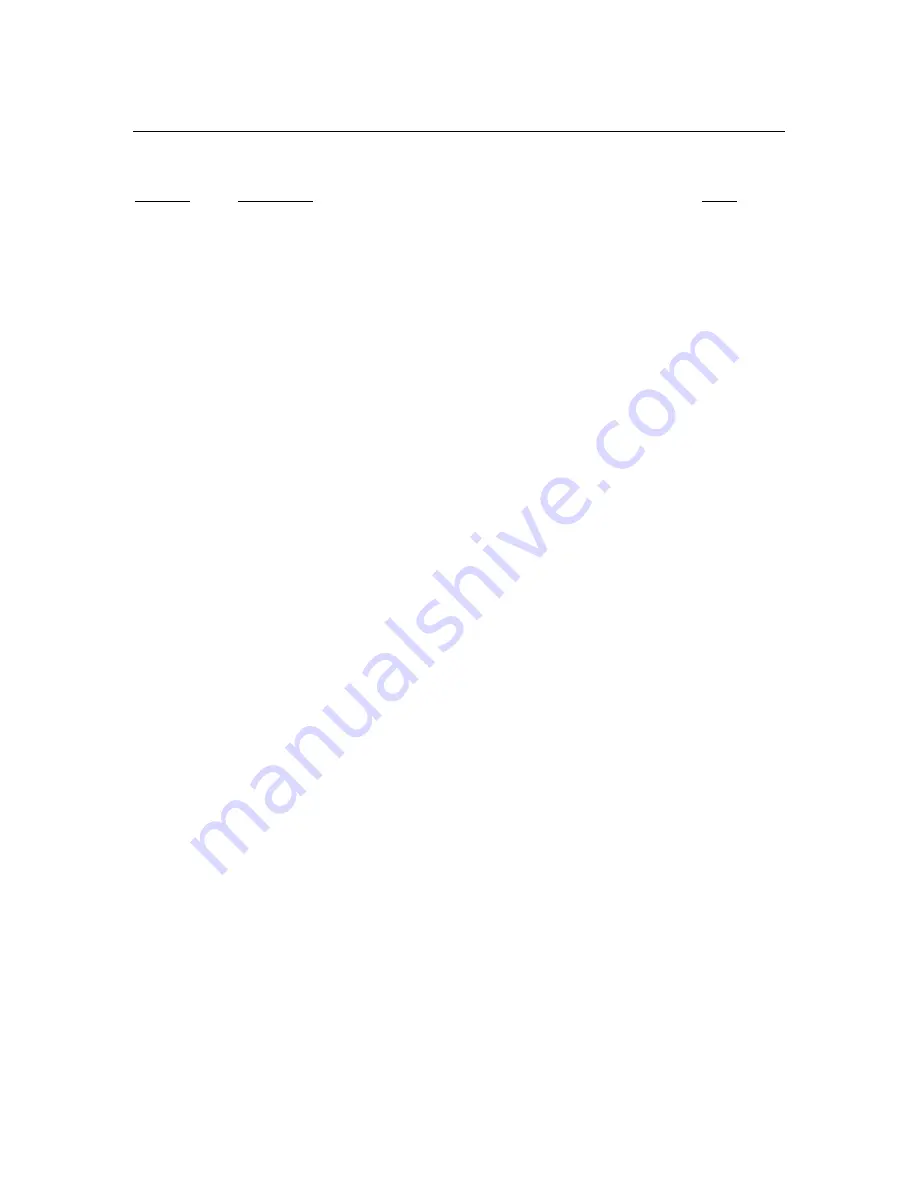
Page v
LIST OF ILLUSTRATIONS
Figure # Description
Page
Figure 2-1 HD-2250 Pump ...................................................................................... 9
Figure 2-2
HD-2250 Power End Section A-A........................................................... 10
Figure 2-3
HD-2250 Power End Section B-B........................................................... 11
Figure 2-4
Fluid End ............................................................................................... 12
Figure 3-1
Power End Lubricant Recommendations................................................ 16
Figure 4-1
Fluid End, Stay Rods, and Heavy Hex Nuts ........................................... 21
Figure 4-2
Packing Assembly ................................................................................. 21
Figure 4-3
Valve Cage Spring Retainer .................................................................. 22
Figure 4-4
Gunsight Spring Retainer....................................................................... 22
Figure 4-5
Crosshead Assembly ............................................................................. 24
Содержание HD-2250
Страница 15: ...FIGURE 2 1 HD 2250 PUMP Page 9...