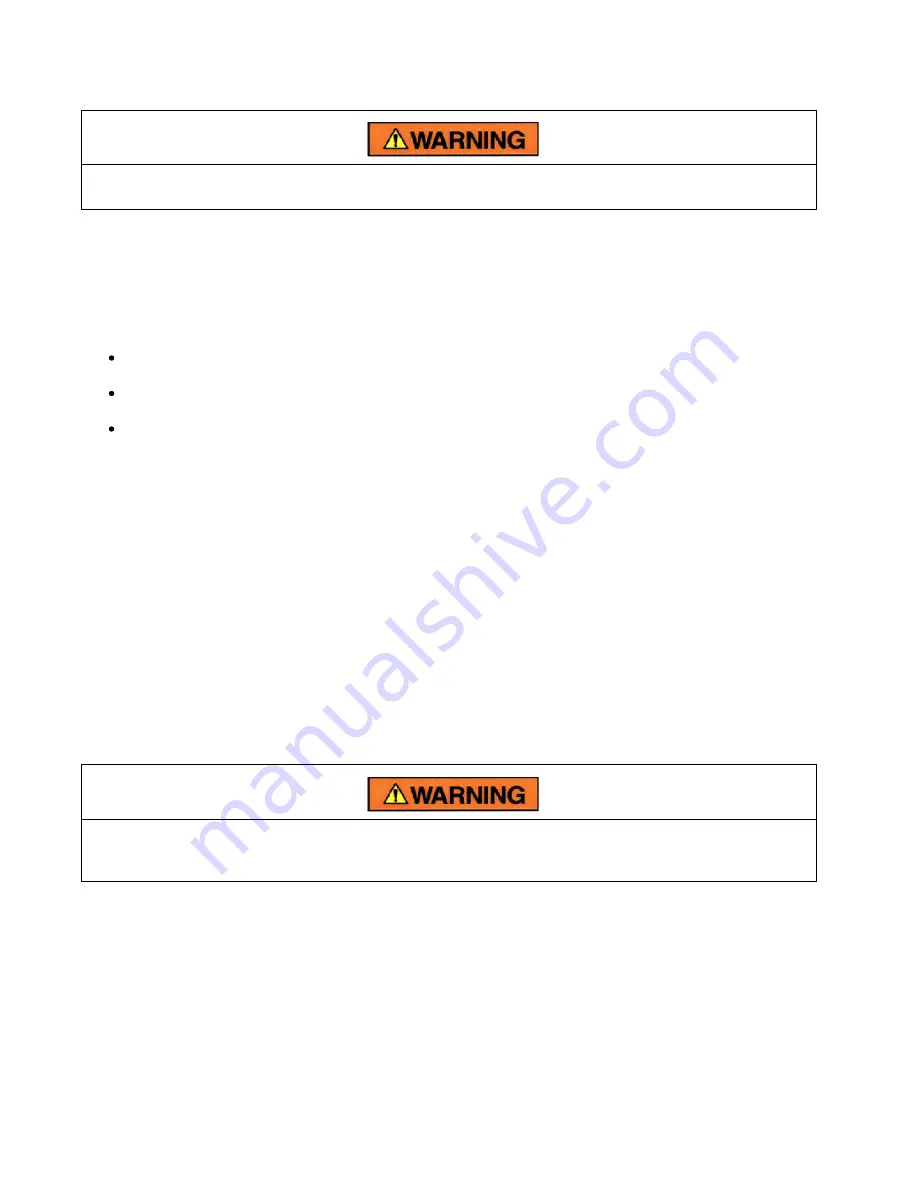
SB-7-621 Page 14
Exceeding overhung load limitations leads to unwarrantable premature bearing failure and shaft
breakage.
The location of the sheave on the blower shaft greatly affects the stress in the shaft. The optimum blower sheave
positioning is as close as possible to the blower drive cover, not to exceed dimension “C” in Drive Shaft
Illustration, FIGURE 2-2, page 15
The calculated shaft moment must not exceed the maximum allowable moment listed in Maximum Allowable
Moment Chart, FIGURE 2-2 page 15. If the calculated shaft moment exceed the maximum allowable moment:
Increase Sheave Diameters to Reduce Belt Pull
Use Jackshaft Drive
Use Direct Coupled or Gearbox Drive
To calculate shaft moment for a given V-Belt Drive Arrangement:
1. Use the formula for Calculation of Belt Pull, FIGURE 2-2, page 15, to calculate belt pull. Refer to Arc of
Contact Factor Chart, Figure 2-2, page 15.
2. Insert the calculated belt pull into the formula for Calculation of Shaft Moment, FIGURE 2-2, page 15 to
arrive at the calculated shaft moment.
PIPING
Inlet and discharge connections on all blowers are large enough to handle maximum volume with minimum
friction loss. Reducing the pipe diameter on either inlet or discharge will only create additional line loss and
increase the overall pressure differential. Excessive weight of piping and fittings will cause internal misalignment
and premature wear. Never allow the blower to carry the weight of the pipe. If possible, a spool or sleeve-type
expansion joint should be installed between the unit and the piping. Where a flexible connection is not practical,
the weight of the rigid connection must be separately supported.
All system piping must be cleaned internally before connecting to the blower.
Sutorbilt blowers are shipped dry from the factory. Do not attempt to operate the blower before
following proper lubrication instructions. Permanent damage to the gears, bearings and seals will
occur.
Содержание GAA_ _ P Series
Страница 2: ......
Страница 36: ...SB 7 621 Page 35 SECTION 8 PARTS LIST 300GAA810 C Ref Drawing ...
Страница 38: ...SB 7 621 Page 37 200GAB810 E Ref Drawing ...
Страница 40: ...SB 7 621 Page 39 300GAC810 B Ref Drawing ...
Страница 42: ...SB 7 621 Page 41 300GAC810 B Ref Drawing ...
Страница 44: ...SB 7 621 Page 43 ...