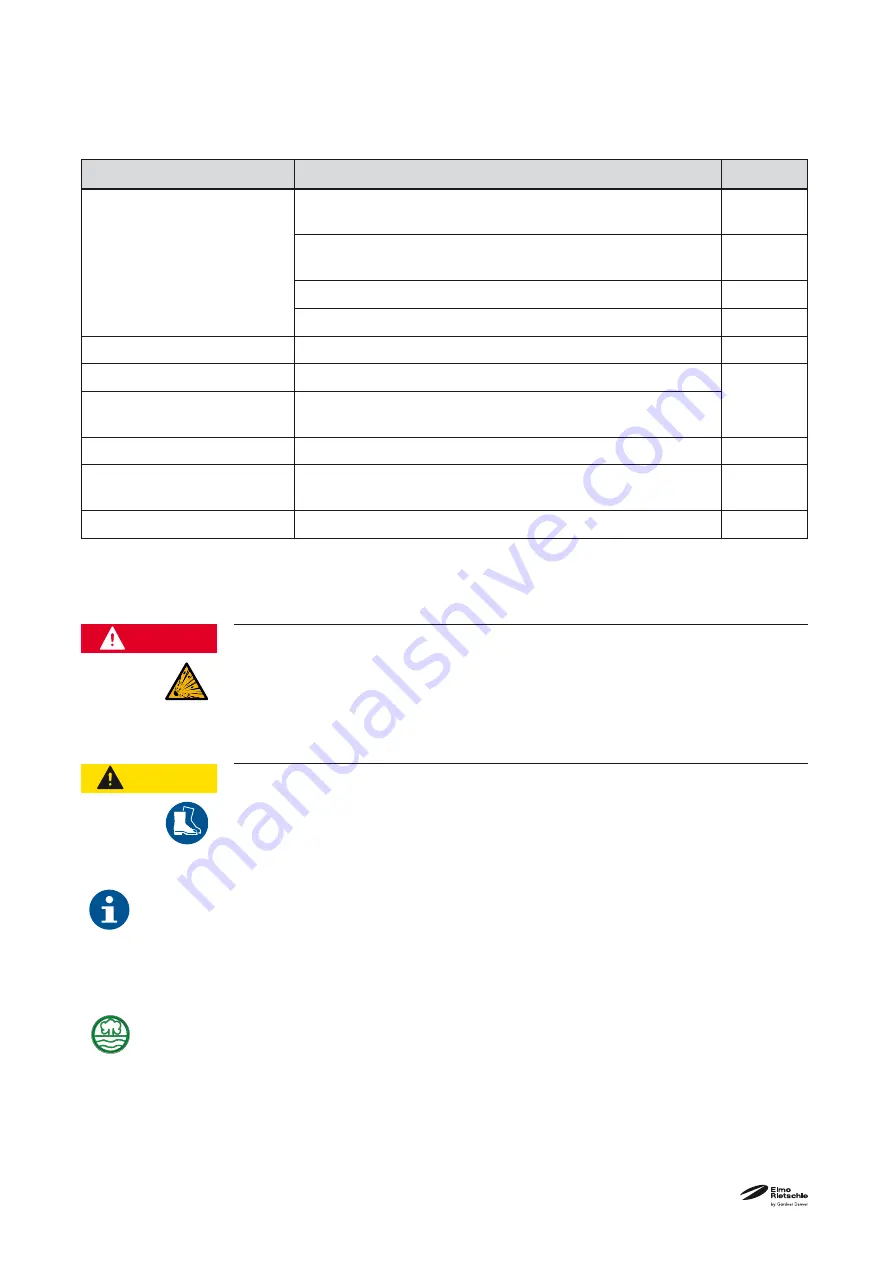
26
|
www.gd-elmorietschle.com © Gardner Denver Schopfheim GmbH, Gardner Denver Deutschland GmbH
Maintenance and repair
7.2 Maintenance tasks
Interval
Maintenance activities
Chapter
Monthly
Check the pipes and screws for leaks and ensure their tight fit
and if necessary re-seal or re-tighten.
–
Check the terminal box and cable inlet holes for leaks and if
necessary re-seal.
–
Clean the cooling ribs on the machine and the motor.
–
Clean the fans, safety guards and cooling-air outlets
–
Monthly
Check the oil level
Monthly
Check the cooling water system and the inlet pipes
Depending on the contami-
nation of the cooling water
Replace cooling water
7,500 h
Oil change
Depending on how dirty the
sucked in medium is
Clean inlet air filter
Clean gas ballast valve filter
At least 1 x per year
Check couplings for wear
7.2.1 Change the oil
DANGER
Risk of explosion due to wrong lubricating oil!
Wrong or not approved lubricating oils can cause potentially explosive gas mixtures.
This causes a serious danger of explosion!
Ø
Exclusively use the type of oil specified by Elmo Rietschle OXY-GEAR-LUBE 160.
This lubricating oil has been released by the Federal Institute for Materials Re-
search and Testing (BAM).
CAUTION
Risk of injury due to slipping and falling!
The floor can be slippery due to leaked oil and cause slipping, tripping or falling.
Ø
For oil change wear non-slip shoes.
Ø
Remove leaked oil immediately.
Always change the oil when the machine is at operating temperature and in an atmospherically
ventilated area. If it is not completely emptied, the refilling quantity is reduced.
If you change the type of oil, empty the oil tank completely.
A minimum oil quantity may escape from the vent screw due to pressure compensation.
If larger quantities of oil escape, wash the internal filter of the vent screw.
The waste oil must be disposed of in compliance with the local environmental protection regulations.