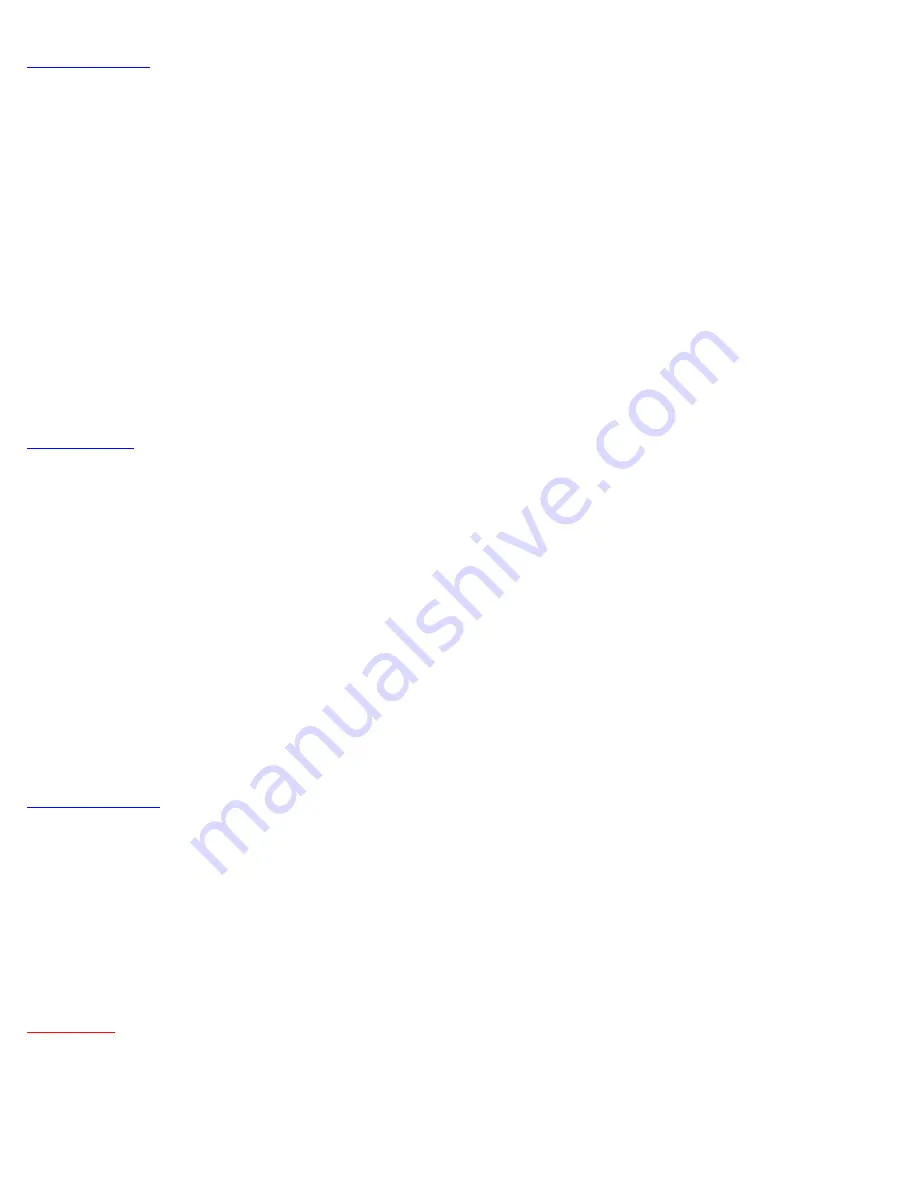
DESCRIPTION
Covered under Patent No. 5,371,933
The GBP205 and the GBP205A are hydraulic installation tools designed specifically for the efficient
installation of a wide range of blind rivets and lockbolt fasteners thru 3/8" diameter, and the installation
of interference fit Hi-Lite® pins. It weighs just under 4 lbs. and can be operated in any position with one
hand. It has a .750 rivet setting stroke.
The GBP205 installation tool operates on hydraulic pressure developed by the GBP940 Powerunit, set
at 5600 psi maximum PULL pressure and 2400 psi maximum RETURN pressure. The tool comes
equipped with 12 feet of hydraulic hoses and couplings, actuator and cord. The GBP205A installation
tool operates on hydraulic pressure developed by the GBP910A Powerunit set at 5600 psi maximum
PULL pressure and 2400 psi maximum RETURN pressure. The tool comes equipped with 12 ft. hydraulic
hoses and couplings, air trigger and tubing.
ALL GBP HYDRAULIC INSTALLATION TOOLS ARE COMPATIBLE WITH HUCK POWERIG'S. NOSE
ASSEMBLIES ARE NOT FURNISHED WITH THE RIVETER AND MUST BE ORDERED SEPARATELY.
OPERATION
When the tool is connected to a Powerunit, operation is controlled by a trigger or switch in the handle.
To send the signal, the GBP205A incorporates an air trigger; the GBP205 an actuator. When the button
is depressed, a directional valve in the Powerunit directs fluid to the front side of the piston forcing it
and the nose assembly collet rearward. This action causes the jaws to clamp on the fastener pintail and
pull the material together. During a lockbolt installation sequence, the anvil is forced over the collar,
swaging it into locking the grooves of the fastener. Further force breaks the pintail off approximately
flush with the collar. The pull-in sequence is started in the same manner, but the pull-in mandrel may
be grabbed a number of times. Releasing the trigger allows the operator to advance the tool on the pin
for installations that require greater than .750 stroke.
When the piston nears the end of its stroke it exposes flats on the back of the unloading valve. These
flats "dump" fluid back to the Powerunit tank. When the button is released the directional valve reverses
fluid flow to the back of the piston and pushes the nose assembly off to the swaged fastener. The spent
pintail is forced out the back of the nose assembly with the insertion of the next fastener.
MAINTENANCE
The performance of any tool depends upon the practice of good maintenance.
Following these minimal requirements for service and care will extend the life of your tool.
*Only use a hydraulic power source equipped with relief valves and
pressures set within specified limits.
Consult Powerunit Manual for procedure to set Pull and Return pressures.
*Keep hydraulic system free of dirt. Avoid letting couplers contact a dirty floor.
*Do not use as a hammer to force fasteners into holes or otherwise abuse tool.
*Proper care by operators is necessary in maintaining full productivity and reducing down time.
WARNING
Be sure Powerunit is disconnected before cleaning, or when replacing worn or damaged components.
Severe personal injury may occur if power source is not disconnected.
4