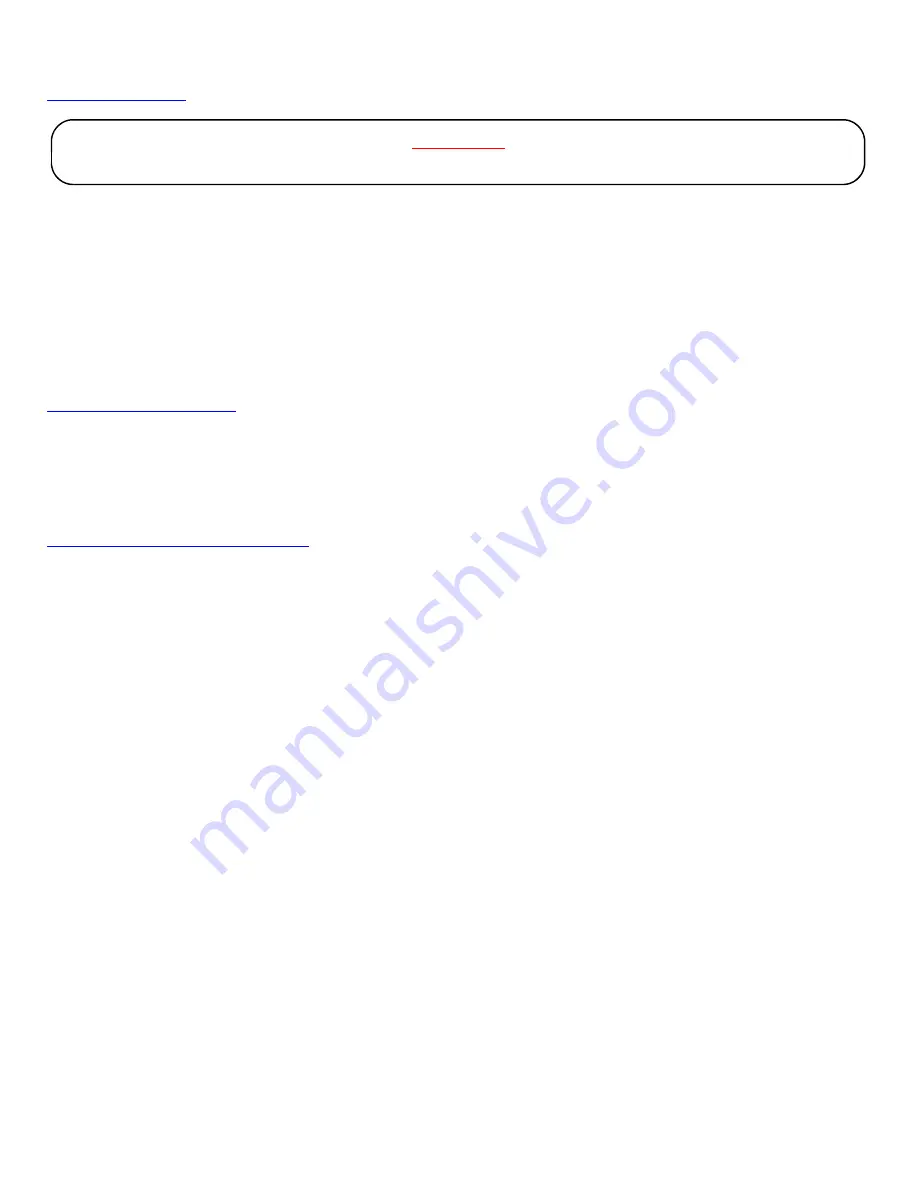
MAINTENANCE:
1. Scheduled inspections to detect and correct minor problems are part of an effective
preventive maintenance program. 902000 service kit contains a complete set of gaskets,
seals and washers these items should be kept on hand at all times.
2. Inspect hydraulic fittings to make sure they are secure.
3. Inspect hoses for signs of damage. Replace hoses if necessary. Inspect during operation to
detect any leakage, abnormal heating or vibration.
4. Inspect hydraulic fluid on a regular basis. Clean reservoir and replace fluid if contamination
5 Keep exterior surfaces clean.
TROUBLESHOOTING:
Use the Troubleshooting Chart as an aid in locating problems and correcting them. Always
check out the simplest possible cause of malfunction first. Eliminate each possible cause until
the part is located. Substitute good parts for suspected bad parts.
TROUBLE SHOOTING CHART:
1. Tool will not reciprocate when motor is running.
A. Improperly coupled hoses.
B. Bind in tool or nose assembly.
C. Pump to motor coupling damaged.
D. Hydraulic fluid level is low or viscosity not proper.
E. Unloading valve in tool improperly installed or missing.
2. Fastener pintail fails to break off.
A. PULL pressure set too low.
B. Defective hose couplers.
C. Defective internal relief valve or set too low.
D. Overheated hydraulic fluid.
E. Hydraulic fluid level low or viscosity not proper.
F. Defective pump.
3. Tool will not return or push nose assembly off swaged fastener when switch is released.
A. Pressure set too low.
4. Pump making noise throughout operating cycle.
A. Pump is cavitating, the fluid viscosity is too heavy or the fluid level may be too low.
B. Filter is clogged or dirty.
6. Tool operates slow throughout entire cycle.
A. Pump is cavitating, the fluid viscosity is too heavy or the fluid level may be too low.
B. Filter is clogged or dirty.
C. Defective pump.
6
WARNING
:
MAKE SURE AIR IS DISCONNECTED BEFORE SERVICING ANY COMPONENTS.
Содержание GB902
Страница 7: ......