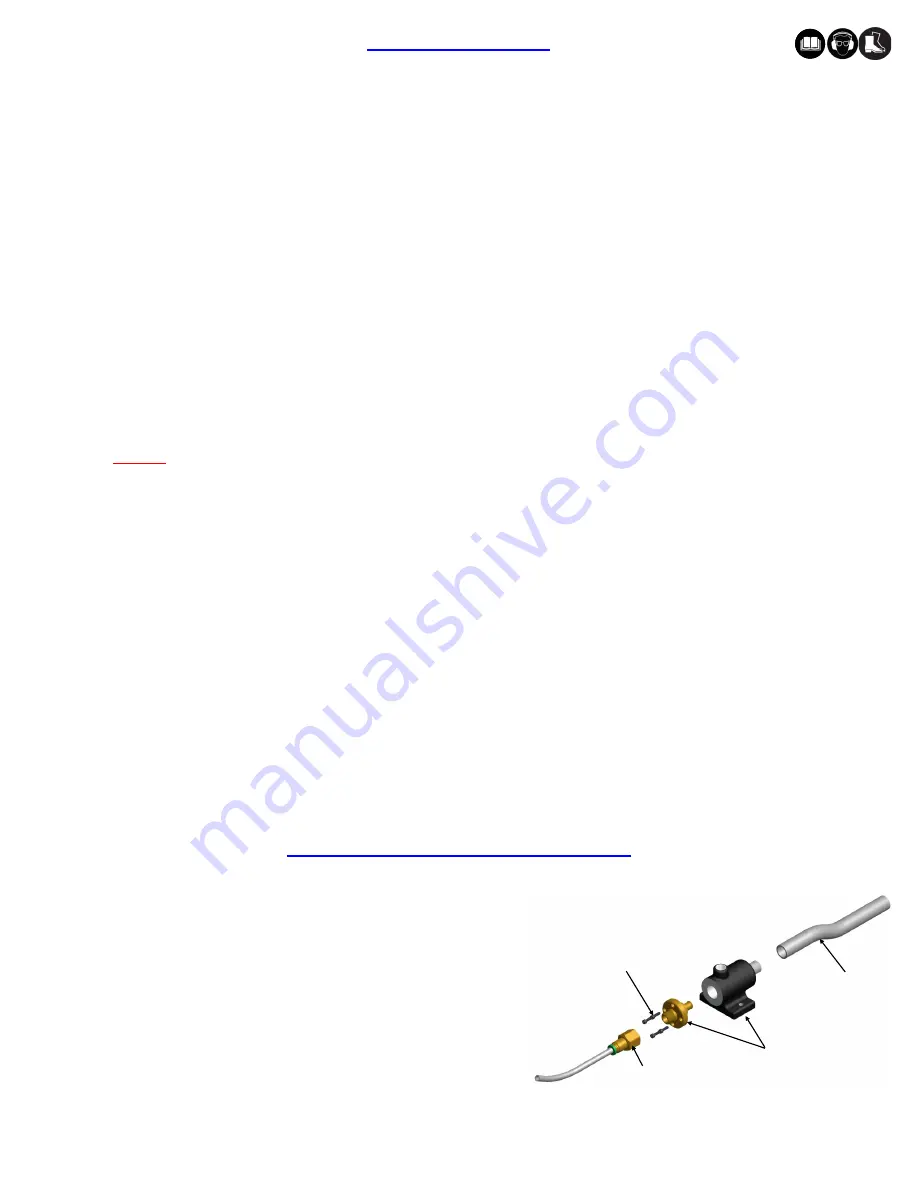
13
5/17 REV. 1/23
GB751SRVT
PLEASE CONTACT GAGE BILT FOR ALL OTHER SERIAL NUMBERS.
TROUBLESHOOTING
Providing all maintenance conditions have been met, follow this systematic approach to diagnosis.
1. MORE THAN ONE PULL IS REQUIRED TO BREAK FASTENER.
a)
Tool needs to be bled. (See filling and bleeding procedures pgs. 11
-
12).
b)
Spring has fatigued, replace.
c)
Jaws are stripped or packed with chips. Clean or replace.
d)
Incorrect nose tip.
2. SLOW OR PARTIAL OPERATION WHEN THE LEVER ASSEMBLY (724017) IS DEPRESSED.
a)
Polyseal (405865) and o
’
ring (400788) on the piston (751307) could be worn or damaged. Replace.
b)
O
’
ring (S945) and backup ring (401102) on the piston rod assembly (704138) could be worn or damaged. Replace.
c)
Muffler (704146) or filter inside valve spool assembly (704143) may be plugged with dirt. Clean thoroughly and back
-
blow
with compressed air.
d)
Hole in metering screw in valve spool assembly (704143) may be blocked or damaged. Hole diameter should be .028" (.71 mm).
Clear and size or replace.
3. NO OPERATION WHEN LEVER ASSEMBLY (724017) IS DEPRESSED.
a)
Tool seized due to mechanical failure or damaged parts.
4. OIL LEAKAGE.
a)
DO NOT
OPERATE WITH OIL LEAKING FROM TOOL. HIGH PRESSURE OIL MAY CAUSE SEVERE PERSONAL INJURY.
b)
Any oil leaking externally should be traced to its source. An o'ring or seal that leaks should be replaced.
5. AIR BYPASS FROM VALVE HOUSING.
a)
If the spring (704141) breaks or dislodges, air will flow freely through the muffler (704146). Replace or reset. Valve spring
installation tool assembly (704262) is recommended.
b)
Check o'rings on valve sleeve (704140), valve spool assembly (704143), and valve plug (704145). If worn or damaged,
replace. Valve sleeve removal tool assembly (704163) is recommended.
6. FASTENER STEM JAMMED IN NOSE ASSEMBLY.
a)
Nose assembly components require service.
DISCONNECT AIR FROM TOOL
, remove the nose from the tool and disassemble.
Replace worn or broken parts. Clean the surface the jaws ride on.
b)
Stems lodged side by side in the follower. Disassemble, remove stems, and reassemble.
c)
Incorrect follower.
7. PINTAIL IS NOT BEING VACCUMED THROUGH.
a) Check vacuum pressure using vacuum gage (703567) (sold separately).
Note: Offset nose assemblies must be check by removing the vacuum line from the nose assembly.
b) Press gage against the vacuum line or nose assembly to create seal.
Optimum vacuum pressure at nose assembly must be between 15
-
22 inHg.
(381
-
558.8 mmHg).
HOW TO CLEAN VACUUM REGULATOR
1.
Remove fitting, adapter and muffler from vacuum regulator (703515).
2.
Remove (4) S.H.C.S. from front of regulator and disassemble.
3.
Clean both pieces in clean mineral spirits and blow dry.
4.
Reassemble and connect hoses.
5.
Check vacuum pressure using vacuum gage (703567) (sold separately).
Press gage against the vacuum line or nose assembly to create seal.
Optimum vacuum pressure at nose assembly must
be between 15
-
22 inHg.
(381
-
558.8 mmHg).
Note: The vacuum regulator may visually appear clean, but still may be
contaminated with a thin film, therefore, the steps above should
be performed to assure best performance.
703515 Vacuum Regulator
Fitting
(
4) S.H.C.S.
Tube
Images may not reflect actual tool