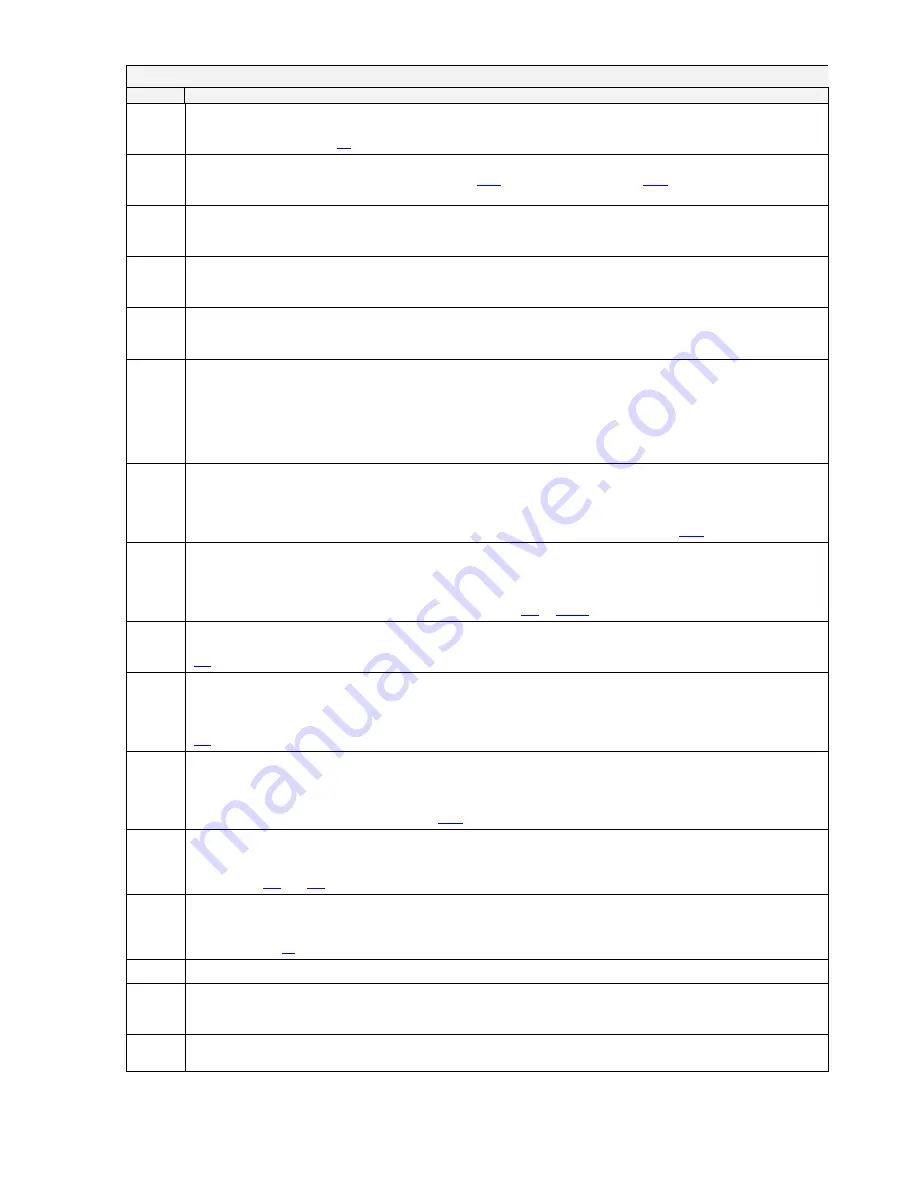
Product Specification
Page 17 of 18
1303090MS01
LA-309 Controlled Atmosphere Infrared Furnace
April 15, 2009
Table 17-1. Optional Equipment
KEY
DESCRIPTION
HSK Handshake
Signaling.
NO and NC signals to upstream and downstream equipment or to the production line
controller about the furnace status when the furnace is part of an automatic production line.
Requires the Process
Ready/Alarm Light Tower (
) option. Option available on all furnaces.
HT High
Temperature
Operation.
High temperature construction for furnace operation above 500°C up to 1000°C.
Includes upgraded insulation and materials, changes
316 stainless steel belt to
Nichrome material, and
adds cabinet temperature thermocouple plus alert/alarm on cabinet temperature.
Option available on most furnaces.
IPS
Inlet Pressure Switch.
Pressure switch upstream of the gas distribution system that signals the operator and the
furnace control system in the event of pressure loss in the process gas supply line. Furnace PROCESS START
mode will be inhibited automatically until pressure is restored to normal.
Option available on most furnaces.
IR-E
Interface Roller, Entrance.
Small diameter belt rollers at the entrance of the furnace that permit close transfer of
parts from upstream conveyor equipment. The rollers are less than 3 inches (76.2 mm) in diameter. Adds 6.4 cm (2.5
inch) to the length of the furnace.
Option available on most furnaces.
IR-X
Interface Roller, Exit:
Small diameter belt rollers at the exit of the furnace that permit close transfer of parts to
downstream conveyor equipment. The rollers will be less than 3 inches (76.2 mm) in diameter. Adds 6.4 cm (2.5
inch) to the length of the furnace.
Option available on most furnaces.
LT
Process Ready/Alarm Light Tower:
Provides a three stage alarm status light tower. The status system activates a
three element alarm light, located above the upper frame, as follows:
o
Red Indicator: Alarm Condition, audible alarm
o
Yellow Indicator: Process Not Ready, no alarm
o
Green Indicator: Process Ready, no alarm
Option available on most furnaces.
MA Moisture
Analyzer:
Provides a moisture monitoring system for the process atmosphere in a furnace with a hermetic
sealed chamber. A gas sample is withdrawn continuously from a sample port in the furnace chamber through the
analyzer. A switched pump and vacuum break are provided to withdraw the sample. The analyzer is provided with
an inline 1µm filter for removal of particulates from the sample flow. ProControl™ OIT displays dew point in ºC or
moisture as PPM, and alert/alarm conditions.
Option available on most furnaces. Requires
option.
N2-S Nitrogen
Auto
Gas
Shutoff:
Automatically opens the nitrogen supply inlet valve when the control system is started,
prior to furnace entering WARM UP mode, and automatically shuts off that valve at furnace shutdown after COOL
DOWN mode is complete. Can help minimize waste of process gas and relieves the operator having to return to the
machine to shut off the process gas when the furnace has cooled down. Includes timed delay to assure clearing of all
process gas and emissions from furnace chamber.
Requires
, option available on most furnaces.
NGFS Nitrogen/Forming
Gas
Selector.
Allows ability to select between nitrogen (N
2
) or a nitrogen hydrogen (N
2
/H
2
) mix
(forming gas) process atmosphere in heating chamber of the furnace, depending on process requirements.
Requires
. Option available on most furnaces.
NO Nitrogen
Operation.
Allows for efficient use of nitrogen (N
2
) in the furnace, minimizing consumption where an N
2
process atmosphere is required. N
2
is supplied only to oxygen-controlled areas (entrance baffle, heating chamber,
and transition tunnel), while CDA is supplied to eductors and cooling. Controlled atmosphere processes should be
reviewed to assure that the product is below its oxidation temperature before reaching cooling section.
Order with
, standard on some furnaces, option available on most furnaces.
OA Oxygen
Analyzer:
Provides an oxygen monitoring system for the process atmosphere in a furnace with a hermetic
sealed chamber. A gas sample is withdrawn continuously from a sample port in the furnace chamber through the
analyzer. A switched pump and vacuum break are provided to withdraw the sample. The analyzer is provided with
an inline 1 µm filter for removal of particulates from the sample flow. ProControl™ OIT displays oxygen concentration
in PPM, and alert/alarm conditions.
-On-line Gas Sampling. System, option available on most furnaces.
OSS
On-line Gas Sampling System:
The sampling system provides 4 selectable inputs: 3 sample ports in the furnace
and 1 port with a 13.7 kPa (2 psi) regulator in-line for source gas monitoring or sensor purging to improve sensor
response during startup of sampling. System may be turned on/off and any of the 4 inputs selected via the furnace OI.
Required for
options, option available on most furnaces
OT
Over-temperature Monitor & Shutdown Alarm.
Provides completely independent temperature measurement in
each zone with audible alarm and automatic furnace shutdown for temperatures out of range. Includes second
thermocouple for each zone directly connected to separate zone scanner and monitor with display. Alarm integrated
with the furnace
Option available on most furnaces.
PCMS
Computer Monitor, Special.
Option available on most furnaces.
PH1
Parts Height, 1 inch.
Reduces clearance at all baffle and cooling section throats, and zone dividers ) to 25 mm (1
inch) from the standard 51 mm (2 inch). Allows for larger zone-to-zone temperature differences for small parts.
Option available on most furnaces.
PH4
Parts Height, 4 inch.
Raises clearance at all baffle and cooling section throats, and zone dividers to 102 mm (4 inch)
from the standard 51 mm (2 inch).
Option available on most furnaces.
Содержание LA-309
Страница 5: ...10 004 676 110000 v WARRANTY Warranty goes here ...
Страница 6: ...vi LA 309 Owner s Manual ...
Страница 12: ...Contents xii LA 309 Owner s Manual ...
Страница 20: ...Section 1 1 8 LA 309 Owner s Manual ...
Страница 68: ...Section 3 3 28 LA 309 Owner s Manual ...
Страница 70: ...Section 4 4 2 LA 309 Owner s Manual ...
Страница 72: ...Section 4 4 4 LA 309 Owner s Manual ...
Страница 98: ...Section 5 5 2 LA 309 Owner s Manual ...
Страница 100: ...Section 5 5 4 LA 309 Owner s Manual ...
Страница 106: ...Section 5 5 10 LA 309 Owner s Manual ...
Страница 108: ...Section 5 5 12 LA 309 Owner s Manual ...
Страница 110: ...Section 5 5 14 LA 309 Owner s Manual ...
Страница 112: ...Section 6 6 2 LA 309 Owner s Manual ...
Страница 114: ......
Страница 115: ......
Страница 126: ...Section 7 1 Fiberfrax Cements MSDS 042006 Owner s Manual ...
Страница 139: ...MSDS 2 Fiberfrax Duraboard MSDS 042006 MATERIAL SAFETY DATA SHEETS ...
Страница 140: ...Section 7 2 Fiberfrax Duraboard MSDS 042006 Owner s Manual ...
Страница 153: ...MSDS 3 Fiberfrax Fibers MSDS 042006 MATERIAL SAFETY DATA SHEETS ...
Страница 154: ...Section 7 3 Fiberfrax Fibers MSDS 042006 Owner s Manual ...
Страница 167: ...MSDS 4 Fiberfrax Papers MSDS 042006 MATERIAL SAFETY DATA SHEETS ...
Страница 168: ...Section 7 4 Fiberfrax Papers MSDS 042006 Owner s Manual ...
Страница 181: ...MSDS 5 Magnaform MSDS 050406 MATERIAL SAFETY DATA SHEETS ...
Страница 182: ...Section 7 5 Magnaform MSDS 050406 Owner s Manual ...
Страница 183: ......
Страница 184: ......
Страница 185: ...Section 7 6 RTU Silicone Red Hi Temp 042006 Owner s Manual ...
Страница 186: ...MSDS 6 RTU Silicone Red Hi Temp 042006 MATERIAL SAFETY DATA SHEETS ...
Страница 189: ...Section 7 7 Kaowool Insulation MSDS 050406 Owner s Manual ...
Страница 190: ...MSDS 7 Kaowool Insulation MSDS 050406 MATERIAL SAFETY DATA SHEETS ...
Страница 201: ...Material Safety Data Sheets 7 15 Notes ...
Страница 202: ...Section 7 7 16 Owner s Manual ...
Страница 203: ...8 1 Section 8 APPENDIX A 8 1 TEC10 INTERFACE MODULE CALIBRATION 8 2 675 110001 FURNACE DRIVE MOTOR AND CONTROL ...
Страница 204: ...Section 8 Owner s Manual ...
Страница 206: ...Section 8 Owner s Manual ...
Страница 212: ...iv Operation and Troubleshooting ...
Страница 214: ...vi Operation and Troubleshooting ...
Страница 224: ...Page 10 Operation and Troubleshooting ...
Страница 231: ...9 1 Section 9 APPENDIX B 9 1 EC913 CALIBRATION REPORT 9 2 SERIES EC900 OXYGEN ANALYZERS ...
Страница 232: ...Section 8 Owner s Manual ...
Страница 233: ......
Страница 234: ...Section 8 Owner s Manual ...
Страница 276: ...EC900 Series Operation Manual V 4 1 www systechillinois com Page 39 Appendix 1 Drawing Number B900 176 ...
Страница 277: ...EC900 Series Operation Manual V 4 1 www systechillinois com Page 40 Appendix 2 Drawing Number B 920 043 ...
Страница 278: ...EC900 Series Operation Manual V 4 1 www systechillinois com Page 41 Appendix 3 Drawing Number B 900 180 ...
Страница 279: ...Section 8 Owner s Manual ...
Страница 281: ...MSDS MATERIAL SAFETY DATA SHEETS ...
Страница 282: ...16 Notes ...