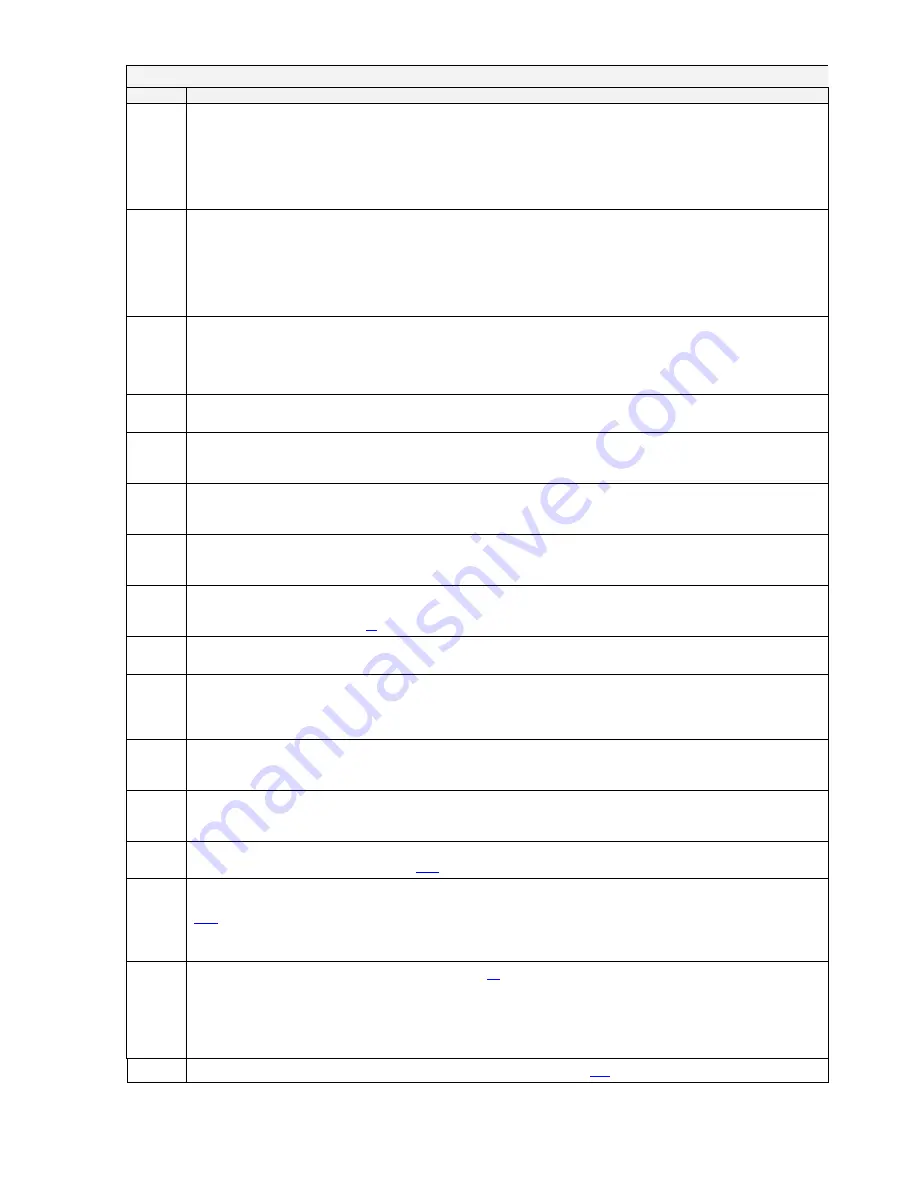
Product Specification
Page 14 of 18
1303090MS01
LA-309 Controlled Atmosphere Infrared Furnace
April 15, 2009
Table 16-1. Base Equipment Features
KEY
DESCRIPTION
CMB30
Forced Air Cooling Module.
Supplies fan-driven ambient air for rapid convection cooling of product on the belt. This
76.2 cm (30 inch) long, forced air cooling module uses two top-mounted cross-flow 13.3 m
3
/min (471 cfm) fans to
force ambient air into a plenum assembly located above the belt, resulting in a downward laminar flow over the entire
surface area of the belt directly under the cooling module. Controlled atmosphere processes should be reviewed to
assure that the product is below its oxidation temperature before reaching the air cooling. Fan speed is controlled via
the control console.
Multiple modules may be joined to obtain required cooling.
Standard on some furnace
configurations, option available on most furnaces.
CMB45
Forced Air Cooling Module.
Supplies fan-driven ambient air for rapid convection cooling of product on the belt. This
1.143 m (45 inch) long, forced air cooling module shall use three top-mounted cross-flow 13.3 m
3
/min (471 cfm) fans
to force ambient air into a plenum assembly located above the belt, resulting in a downward laminar flow over the
entire surface area of the belt directly under the cooling module. Controlled atmosphere processes should be
reviewed to assure that the product is below its oxidation temperature before reaching the air cooling. Fan speed is
controlled via the control console.
Multiple modules may be joined to obtain required cooling.
Standard on some
furnace configurations, option available on most furnaces.
CWWC
Cold Wall Water Cooling Module.
High efficiency, 50.8 cm (20 inch) long, water-cooled module that improves heat
transfer from cooling tunnel, more rapidly reducing the temperature of the product. Includes OI integrated inlet and
outlet water temperature sensors and alarms. Requires water supply and drain. Multiple modules may be joined to
obtain required cooling. Upgrade from CACT.
Standard on some furnace configurations, option available on most
furnaces.
DOCM
Furnace Owner’s Manual.
Installation, startup operating, and troubleshooting instructions for a specific furnace.
Includes specific customer drawings, schematics and engineering calculations.
Standard on all furnaces.
DOCR
Furnace Reference Manual.
Continuous Belt IR Furnace Reference Manual including information on IR furnace
nomenclature, thermal processing; furnace control and software; maintenance, troubleshooting and calibration; and
process engineering.
Standard on all furnaces.
EME
Entrance Emergency Machine Off, Vertical Mount.
Two (2) SEMI approved 40 mm diameter emergency shutoff
buttons are located on either side of the entrance on the vertical face of the furnace approximately 1.27 m (50 inches)
above grade.
Standard on all furnaces.
EMX
Exit Emergency Machine Off, Vertical Mount.
Two (2)
SEMI approved 40 mm diameter emergency shutoff buttons
are located on either side of the exit on the vertical face of the furnace approximately 1.27 m (50 inches) above grade.
Standard on all furnaces.
ENG
English Units of Measure
or US customary units
.
Furnace control software shall depict belt speed in inches per
minute (in/min), gas flow in standard cubic feet per hour (scfh). Temperature units shall be degrees Celcius (°C).
Standard on all furnaces unless
is selected at time of order.
ETM Elapsed
Time
Meter.
Adds a mechanical meter to keep track of the cumulative time the furnace is ON.
Standard on
all furnaces.
FM
Independent Zone Flow Control.
Process Gas is controlled by variable rate flowmeters enclosed behind a clear
panel. Panel access can be restricted by one of three methods: Keyed lock, mechanical latch or fastened by screws
(lock and latch shall both be provided). Atmosphere shall be controlled by manually adjustment of the flowmeters.
Standard on all furnaces.
IE
Intermediate Exhaust Eductor.
An exhaust stack with eductor that is located between selected chambers to
increase control of process gas flow, to promote isolation of specific furnace chambers and to evacuate volatile
emissions off-gassed from product.
Standard on some furnaces.
LOAD Load
Station.
The load station is an area 381 mm long (15 inch) at the entrance of the furnace which provides open
access to accommodate loading of product on the continuous belt for processing by the furnace.
Standard on all
furnaces.
LTR
Left to Right:
Belt moves from left to right as viewed from the operator console. This is the default furnace
configuration.
Standard on all furnaces if
is not specified with original order.
OI Operator
Interface.
Operator Interface also known as MMI (man machine interface), and HMI (human machine
interface). OI refers to the furnace graphical display software that the operator uses to communicate with the furnace
and to observe data collected by the Furnace PLC.
Furnace graphical interface software that allow the user to view and modify furnace operating parameters and
communicate with the PLC.
Standard on most furnaces.
OIT
Operator Interface Terminal.
Furnace computer with
, OIT refers to the furnace computer that the operator uses
to communicate changes to the furnace PLC and to observe data collected by the Furnace PLC.
Furnace computer and monitor are wired to stay “ON”, regardless of control panel ON/OFF pushbuttons, as long as
power is supplied to furnace. This arrangement allows reliable startup and shutdown of the furnace computer, allows
use of the furnace computer without powering up the furnace, and extends furnace computer life and reliability.
Standard on most furnaces.
OSXP
XP Operating System.
Microsoft WindowsXP™ operating system on the
Содержание LA-309
Страница 5: ...10 004 676 110000 v WARRANTY Warranty goes here ...
Страница 6: ...vi LA 309 Owner s Manual ...
Страница 12: ...Contents xii LA 309 Owner s Manual ...
Страница 20: ...Section 1 1 8 LA 309 Owner s Manual ...
Страница 68: ...Section 3 3 28 LA 309 Owner s Manual ...
Страница 70: ...Section 4 4 2 LA 309 Owner s Manual ...
Страница 72: ...Section 4 4 4 LA 309 Owner s Manual ...
Страница 98: ...Section 5 5 2 LA 309 Owner s Manual ...
Страница 100: ...Section 5 5 4 LA 309 Owner s Manual ...
Страница 106: ...Section 5 5 10 LA 309 Owner s Manual ...
Страница 108: ...Section 5 5 12 LA 309 Owner s Manual ...
Страница 110: ...Section 5 5 14 LA 309 Owner s Manual ...
Страница 112: ...Section 6 6 2 LA 309 Owner s Manual ...
Страница 114: ......
Страница 115: ......
Страница 126: ...Section 7 1 Fiberfrax Cements MSDS 042006 Owner s Manual ...
Страница 139: ...MSDS 2 Fiberfrax Duraboard MSDS 042006 MATERIAL SAFETY DATA SHEETS ...
Страница 140: ...Section 7 2 Fiberfrax Duraboard MSDS 042006 Owner s Manual ...
Страница 153: ...MSDS 3 Fiberfrax Fibers MSDS 042006 MATERIAL SAFETY DATA SHEETS ...
Страница 154: ...Section 7 3 Fiberfrax Fibers MSDS 042006 Owner s Manual ...
Страница 167: ...MSDS 4 Fiberfrax Papers MSDS 042006 MATERIAL SAFETY DATA SHEETS ...
Страница 168: ...Section 7 4 Fiberfrax Papers MSDS 042006 Owner s Manual ...
Страница 181: ...MSDS 5 Magnaform MSDS 050406 MATERIAL SAFETY DATA SHEETS ...
Страница 182: ...Section 7 5 Magnaform MSDS 050406 Owner s Manual ...
Страница 183: ......
Страница 184: ......
Страница 185: ...Section 7 6 RTU Silicone Red Hi Temp 042006 Owner s Manual ...
Страница 186: ...MSDS 6 RTU Silicone Red Hi Temp 042006 MATERIAL SAFETY DATA SHEETS ...
Страница 189: ...Section 7 7 Kaowool Insulation MSDS 050406 Owner s Manual ...
Страница 190: ...MSDS 7 Kaowool Insulation MSDS 050406 MATERIAL SAFETY DATA SHEETS ...
Страница 201: ...Material Safety Data Sheets 7 15 Notes ...
Страница 202: ...Section 7 7 16 Owner s Manual ...
Страница 203: ...8 1 Section 8 APPENDIX A 8 1 TEC10 INTERFACE MODULE CALIBRATION 8 2 675 110001 FURNACE DRIVE MOTOR AND CONTROL ...
Страница 204: ...Section 8 Owner s Manual ...
Страница 206: ...Section 8 Owner s Manual ...
Страница 212: ...iv Operation and Troubleshooting ...
Страница 214: ...vi Operation and Troubleshooting ...
Страница 224: ...Page 10 Operation and Troubleshooting ...
Страница 231: ...9 1 Section 9 APPENDIX B 9 1 EC913 CALIBRATION REPORT 9 2 SERIES EC900 OXYGEN ANALYZERS ...
Страница 232: ...Section 8 Owner s Manual ...
Страница 233: ......
Страница 234: ...Section 8 Owner s Manual ...
Страница 276: ...EC900 Series Operation Manual V 4 1 www systechillinois com Page 39 Appendix 1 Drawing Number B900 176 ...
Страница 277: ...EC900 Series Operation Manual V 4 1 www systechillinois com Page 40 Appendix 2 Drawing Number B 920 043 ...
Страница 278: ...EC900 Series Operation Manual V 4 1 www systechillinois com Page 41 Appendix 3 Drawing Number B 900 180 ...
Страница 279: ...Section 8 Owner s Manual ...
Страница 281: ...MSDS MATERIAL SAFETY DATA SHEETS ...
Страница 282: ...16 Notes ...