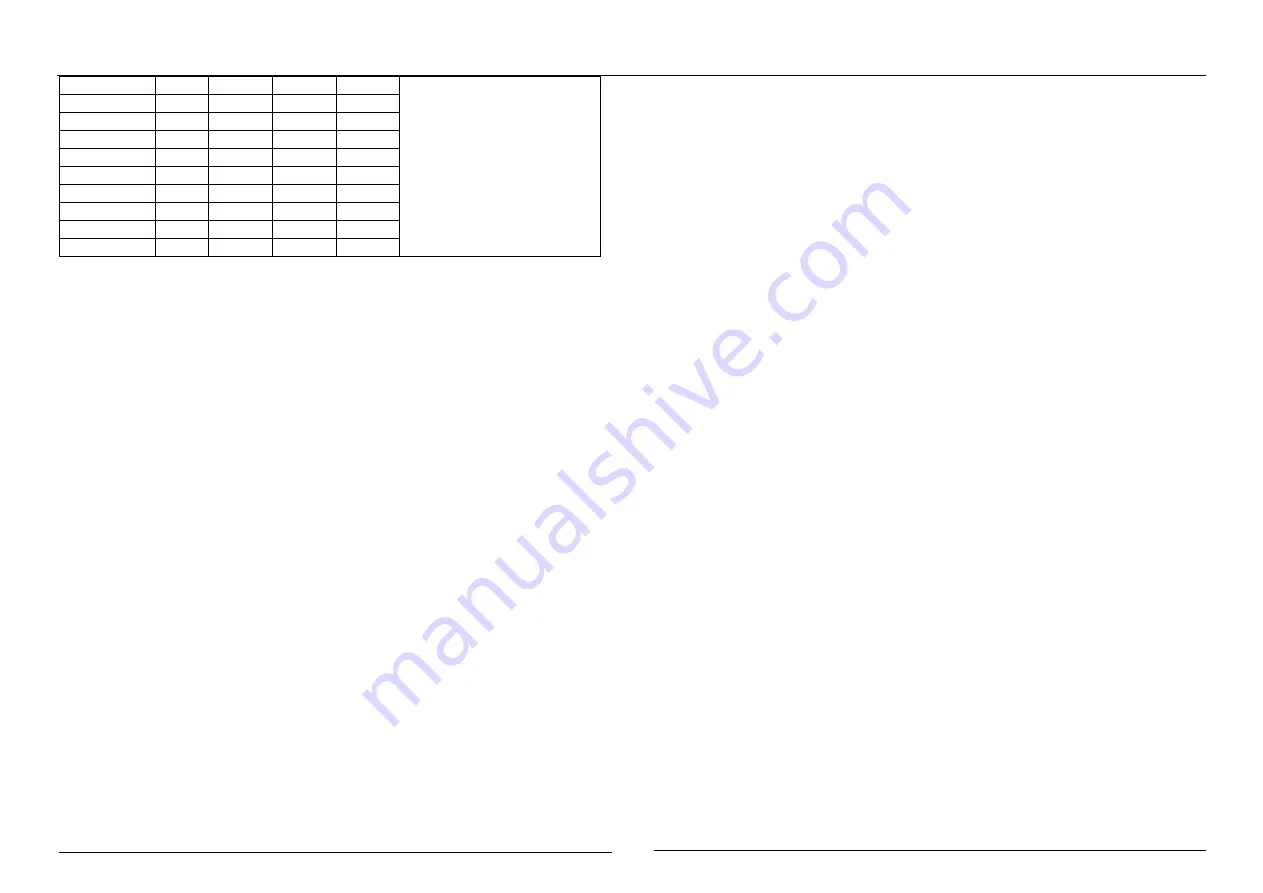
User’s Manual for FD556 Digital 2-Phase Stepper Driver
User’s Manual for FD556 Digital 2-Phase Stepper Driver
11 12
12800
on
off
off
on
ProTuner software or STU
debugger to set the number of
resolutions, the minimum value
is 1, the resolution is 1, and the
maximum value is 51200.
25600
off
off
off
on
1000
on
on
on
off
2000
off
on
on
off
4000
on
off
on
off
5000
off
off
on
off
8000
on
on
off
off
10000
off
on
off
off
20000
on
off
off
off
25000
off
off
off
off
3. Parameter auto-tuning function
If SW4 is toggled return in 1S, each parameter of the motor can be automatically
identified once at each instant of powered-on, and the driver can automatically complete
the auto-tuning of the motor parameters and internal adjustment parameters. To get the
optimized performance, please repower the driver will auto-identify the new motor and
auto-configure related control parameters when the motor power supply voltage and other
conditions change.
Note that pulse can’t be input, the direction signal should not be changed, and the
enable signal can’t be connected at this time.
Ⅴ
.Power Supply Selection
It is important to choose appropriate power supply to make the driver operate
properly and deliver optimal performance. Both unregulated and regulated power
supplies can be used to supply DC power to the FD556S driver. If regulated power
supply is indeed used, voltage ripple peak value after rectification doesn’t exceed its
specified maximum voltage. Therefore, it is suggested to use power supplies with
theoretical output voltage of no more than its defined voltage, leaving room for power
line fluctuation.
If regulated power supplies (such as most switching supplies.) are indeed used, it is
important to have large current output rating to avoid problems like current clamp.
Please Note:
1
)
Power Supply polarity not then reversed.
2
)
Best to use an unregulated power supply.
3
)
if unregulated supply is used, The power supply current output capacity should be
greater than 60% of the driver setting current.
4
)
if regulated supply is used, the average current withdrawn from power supply is more
than or equal to driver current.
5
)
It is recommended to have two or three drives to share one power supply to reduce
cost, if the supply has enough capacity.
Ⅵ
.Motor option
The FD556S can drive any 2-phase and 4-phase of 4, 6, 8-lead hybrid stepping motors,
which is suitable for 1.8°and 0.9°step angle motor. When selecting a motor, it is mainly
determined by the torque and rated current of the motor. The torque is determined by the
size of the motor, the larger the size of the motor, the larger the torque.
While the current is mainly related to the inductance, the small-inductance motor has
good high-speed performance, but larger currents.
1. Motor Option
1
)
Determine load torque, transmission ratio and working speed range.
T
电机
=C
(
Jε+T
负载
)
J
:
Moment of inertia of load
ε
:
Maximum angular acceleration of the load
C
:
Safety factor, recommend 1.2~1.4
T
负载
:
Maximum load torque, Contains resistance torque such as payload, friction,
transmission efficiency.
2
)
What factors determine the motor output torque
●
For a given stepping motor and coil connection, the output torque has the following
characteristics.
●
For a given motor, higher driver current will make the motor to output more torque,
but at the same time causes more copper loss heating in the motor and driver.
●
Higher supply voltage can increase motor torque at higher speeds, thus helpful for
avoiding losing steps.
●
From the torque-frequency characteristic diagram
of the stepper motor, the High-speed
torque is smaller than that of the medium-low speed.