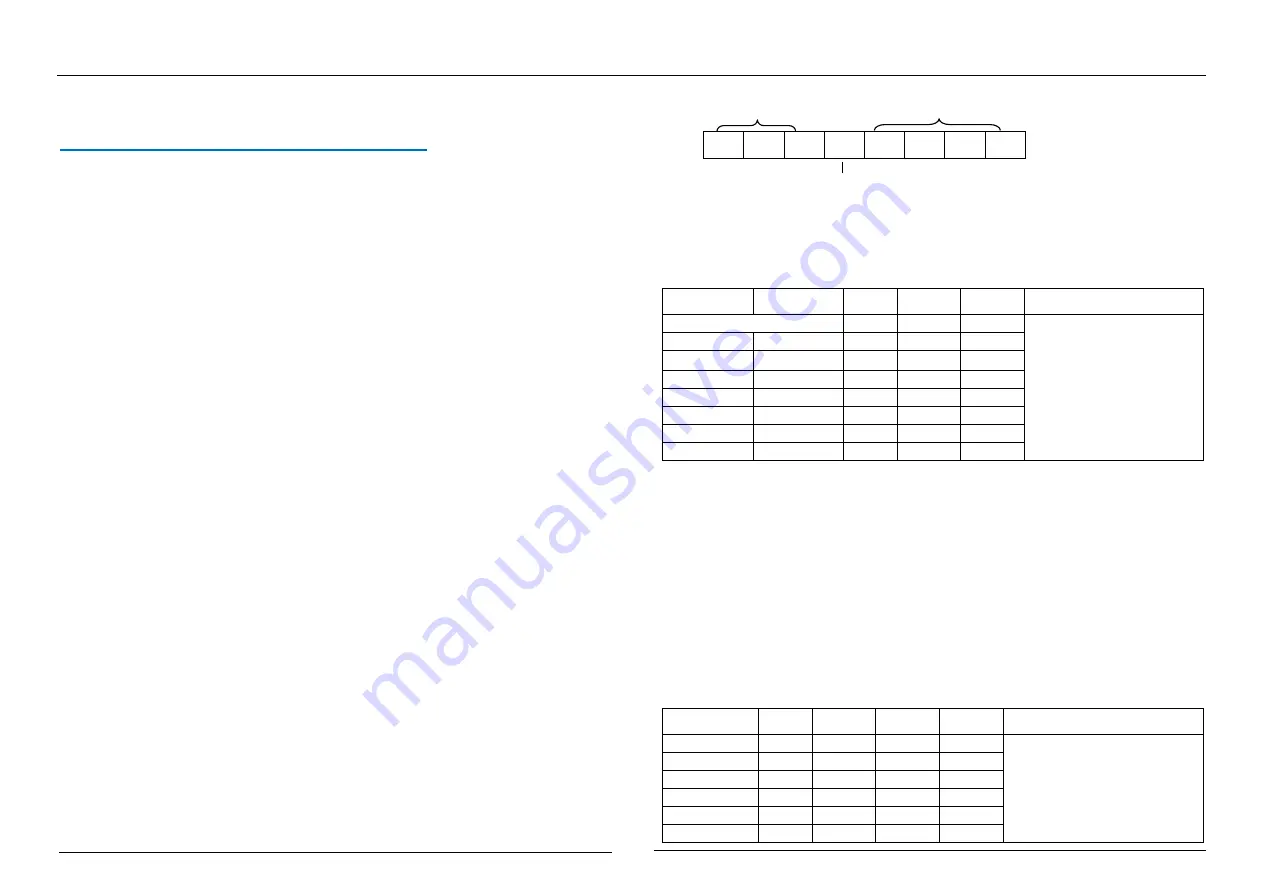
User’s Manual for FD556 Digital 2-Phase Stepper Driver
User’s Manual for FD556 Digital 2-Phase Stepper Driver
9 10
4
)
t4: Low level width not less than 2us.
4. Control Signal Mode Setting
Pulse trigger edge and single/double pulse selection:
By PC software (ProTuner
software) or STU debugger set the rising or falling edge trigger of the pulse is a valid,
and set single or double pulse mode. In the double-pulse mode, the signal at the direction
control terminal must be kept high or left floating.
5. Wire Connection
1) In order to improve anti-interference performance of the driver, it is recommended to
use twisted pair shield cable, and the shield is shorted to ground, Except for special
requirements, the shielded wire of the control signal cable is also shorted to
single-ended ground. The upper end of the shielded wire is grounded, and the driver
end is floating. Only allowed on the same point grounding in the same machine, If it
is not a real ground wire, the interference may be serious, and the shielding layer is
not connected at the time.
2) To prevent noise incurred in PUL/DIR signal, pulse/direction signal wires and motor
wires should not be tied up together. It is better to separate them by at least 10 cm,
otherwise the disturbing signals generated by motor will easily disturb pulse direction
signals, causing motor position error, system instability and other failures.
3) If a power supply several drivers, parallel connection is recommend instead of
daisy-chaining.
4) It is prohibited to pull and plug power connector P2 while the driver is powered ON,
because there is high current flowing through motor coils (even when motor is at
standstill). Pulling or plugging power connector P2 with power on will cause
extremely high back-EMF voltage surge, which may damage the driver.
5) It is strictly forbidden to add lead to the terminal after adding tin, otherwise the
terminal may be damaged due to the increased contact resistance.
6)
Lug must not be exposed outside the terminal to prevent accidental short circuit and
damage to the driver.
Ⅳ
. Driver Current Output, Selecting Microstep Resolution
and Parameter auto-tuning function
This FD556S driver uses an 8-bit DIP switch to set microstep resolution, motor
dynamic current, standstill half-current, motor parameters and internal adjustment
parameters auto-tuning, as shown below:
SW1 SW2
SW3 SW4 SW5
SW6 SW7 SW8
1 Current Setting
1
)
Dynamic current Setting
Peak Current
RMS Current SW1
SW2
SW3
Current Setting
Default[1.0A]
off
off
off
When SW1,SW2.SW3 are
set to off, it can be set to the
required current by PC
Software, Maximum value is
4.2A and resolution is 0.1A,
If it is not set, the default is
1A.
2.1A
1.5A
on
off
off
2.7A
1.9A
off
on
off
3.2A
2.3A
on
on
off
3.8A
2.7A
off
off
on
4.3A
3.1A
on
off
on
4.9A
3.5A
off
on
on
5.6A
4.0A
on
on
on
2
)
Standstill Current Setting
SW4 is used for this purpose. off means that the standstill current is set to be half of
the selected dynamic current, and on means that standstill current is set to be the same as
the selected dynamic current. In general SW4 should be set to off to enable the heat
generation of the motor and driver to be reduced and the reliability to be improved. The
current automatically reduced to 60% of dynamic current setting 400 millisecond after
the last pulse. Theoretically, This will reduce motor heating to 30% (due to P=I2*R)) of
the original value.
2. Microstep Resolution Selection
Steps/rev.
SW5
SW6
SW7
SW8
Resolution Description
Default[3600]
on
on
on
on
。
When SW5,SW6,SW7 and
SW8 are on, the driver uses the
default number of resolution
within the driver. Use PC
400
off
on
on
on
800
on
off
on
on
1600
off
off
on
on
3200
on
on
off
on
6400
off
on
off
on
Microstep Resolution Setting
Half Current/Full Current Parameter Setting
Dynamic current Setting