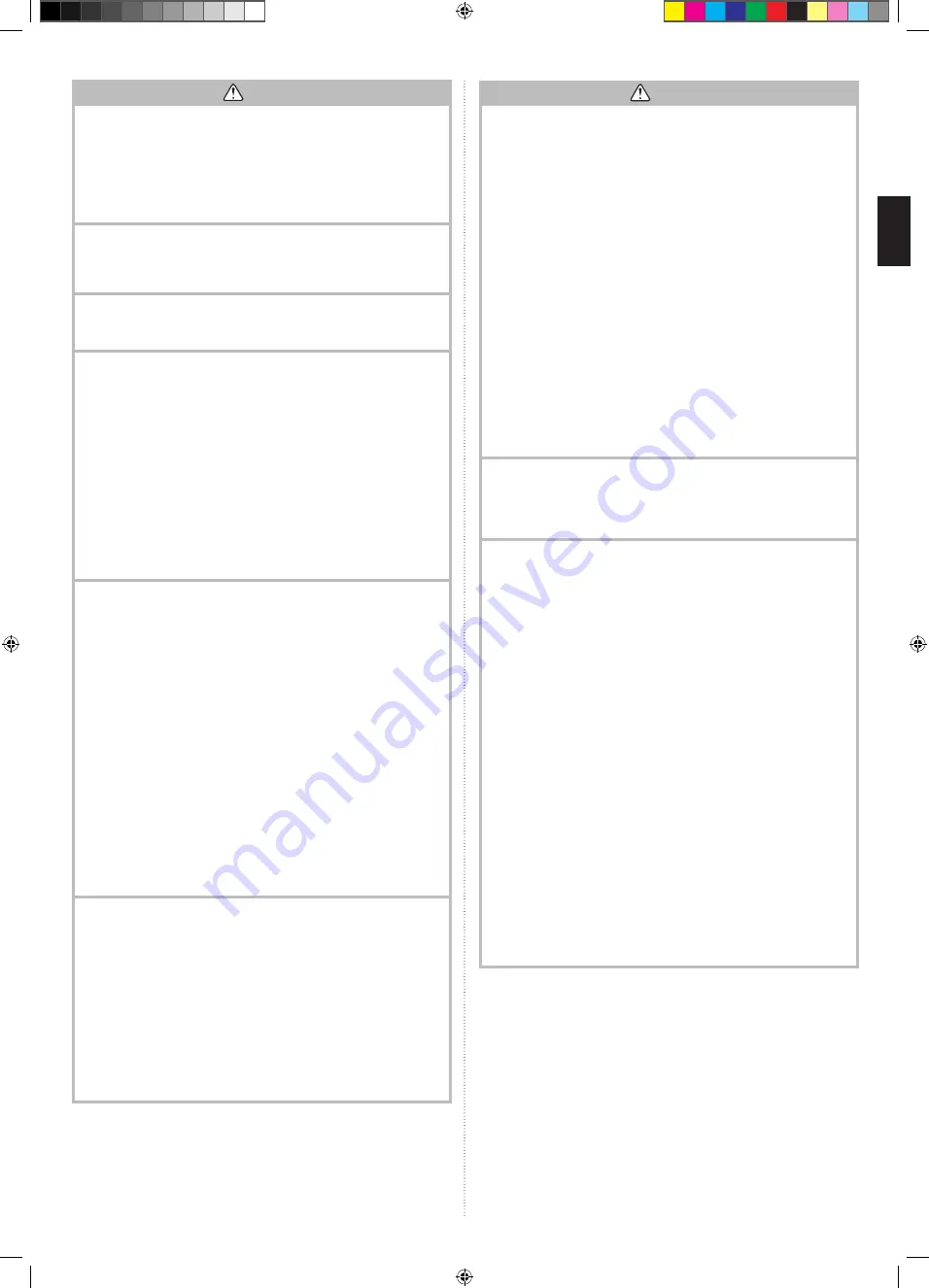
En-3
CAUTION
4-Repair to intrinsically safe components
• Do not apply any permanent inductive or capacitance loads to the circuit without
ensuring that this will not exceed the permissible voltage and current permitted for
the equipment in use.
• Intrinsically safe components are the only types that can be worked on while live in
the presence of a
fl
ammable atmosphere.
• The test apparatus shall be at the correct rating.
• Replace components only with parts speci
fi
ed by the manufacturer.
• Other parts may result in the ignition of refrigerant in the atmosphere from a leak.
5-Cabling
• Check that cabling will not be subject to wear, corrosion, excessive pressure, vibra-
tion, sharp edges or any other adverse environmental effects.
• The check shall also take into account the effects of aging or continual vibration from
sources such as compressors or fans.
6-Detection of
fl
ammable refrigerants
• Under no circumstances shall potential sources of ignition be used in the searching
for or detection of refrigerant leaks.
• A halide torch (or any other detector using a naked
fl
ame) shall not be used.
7-Leak detection methods
• Electronic leak detectors shall be used to detect
fl
ammable refrigerants, but the
sensitivity may not be adequate, or may need re-calibration. (Detection equipment
shall be calibrated in a refrigerant-free area.)
• Ensure that the detector is not a potential source of ignition and is suitable for the
refrigerant used.
• Leak detection equipment shall be set at a percentage of the LFL of the refrigerant
and shall be calibrated to the refrigerant employed and the appropriate percentage
of gas (25 % maximum) is con
fi
rmed.
• Leak detection
fl
uids are suitable for use with most refrigerants but the use of
detergents containing chlorine shall be avoided as the chlorine may react with the
refrigerant and corrode the copper pipe-work.
• If a leak is suspected, all naked
fl
ames shall be removed/extinguished.
• If a leakage of refrigerant is found which requires brazing, all of the refrigerant shall
be recovered from the system, or isolated (by means of shut off valves) in a part of
the system remote from the leak.
Oxygen free nitrogen (OFN) shall then be purged through the system both before
and during the brazing process.
8-Removal and evacuation
• When breaking into the refrigerant circuit to make repairs – or for any other
purpose –conventional procedures shall be used.
However, it is important that best practice is followed since
fl
ammability is a consid-
eration.
The following procedure shall be adhered to:
• remove refrigerant
• purge the circuit with inert gas
• evacuate
• purge again with inert gas
• open the circuit by cutting or brazing
• The refrigerant charge shall be recovered into the correct recovery cylinders.
• The system shall be “
fl
ushed” with OFN to render the unit safe.
• This process may need to be repeated several times.
• Compressed air or oxygen shall not be used for this task.
• Flushing shall be achieved by breaking the vacuum in the system with OFN and
continuing to
fi
ll until the working pressure is achieved, then venting to atmosphere,
and
fi
nally pulling down to a vacuum.
• This process shall be repeated until no refrigerant is within the system.
• When the
fi
nal OFN charge is used, the system shall be vented down to atmospheric
pressure to enable work to take place.
• This operation is absolutely vital if brazing operations on the pipe work are to take
place.
• Ensure that the outlet for the vacuum pump is not close to any ignition sources and
there is ventilation available.
9-Charging procedures
• In addition to conventional charging procedures, the following requirements shall be
followed.
- Ensure that contamination of different refrigerants does not occur when using
charging equipment.
Hoses or lines shall be as short as possible to minimize the amount of refrigerant
contained in them.
- Cylinders shall be kept upright.
- Ensure that the refrigeration system is earthed prior to charging the system with
refrigerant.
- Label the system when charging is complete (if not already).
- Extreme care shall be taken not to over
fi
ll the refrigeration system.
• Prior to recharging the system it shall be pressure tested with OFN.
• The system shall be leak tested on completion of charging but prior to commission-
ing.
• A follow up leak test shall be carried out prior to leaving the site.
CAUTION
10-Decommissioning
• Before carrying out this procedure, it is essential that the technician is completely
familiar with the equipment and all its details.
• It is recommended good practice that all refrigerants are recovered safely.
• Prior to the task being carried out, an oil and refrigerant sample shall be taken in
case analysis is required prior to re-use of reclaimed refrigerant.
• It is essential that electrical power is available before the task is commenced.
a) Become familiar with the equipment and its operation.
b) Isolate system electrically.
c) Before attempting the procedure ensure that:
• mechanical handling equipment is available, if required, for handling refriger-
ant cylinders;
• all personal protective equipment is available and being used correctly;
• the recovery process is supervised at all times by a competent person;
• recovery equipment and cylinders conform to the appropriate standards.
d) Pump down refrigerant system, if possible.
e) If a vacuum is not possible, make a manifold so that refrigerant can be removed
from various parts of the system.
f) Make sure that cylinder is situated on the scales before recovery takes place.
g) Start the recovery machine and operate in accordance with manufacturer’s
instructions.
h) Do not over
fi
ll cylinders. (No more than 80 % volume liquid charge).
i) Do not exceed the maximum working pressure of the cylinder, even temporarily.
j) When the cylinders have been
fi
lled correctly and the process completed, make
sure that the cylinders and the equipment are removed from site promptly and all
isolation valves on the equipment are closed off.
k) Recovered refrigerant shall not be charged into another refrigeration system un-
less it has been cleaned and checked.
11-Labelling
• Equipment shall be labelled stating that it has been de-commissioned and emptied
of refrigerant.
• The label shall be dated and signed.
• Ensure that there are labels on the equipment stating the equipment contains
fl
am-
mable refrigerant.
12-Recovery
• When removing refrigerant from a system, either for servicing or decommissioning, it
is recommended good practice that all refrigerants are removed safely.
• When transferring refrigerant into cylinders, ensure that only appropriate refrigerant
recovery cylinders are employed.
• Ensure that the correct number of cylinders for holding the total system charge are
available.
• All cylinders to be used are designated for the recovered refrigerant and labelled for
that refrigerant (i.e. special cylinders for the recovery of refrigerant).
• Cylinders shall be complete with pressure relief valve and associated shut-off valves
in good working order.
• Empty recovery cylinders are evacuated and, if possible, cooled before recovery
occurs.
• The recovery equipment shall be in good working order with a set of instructions
concerning the equipment that is at hand and shall be suitable for the recovery of
fl
ammable refrigerants.
• In addition, a set of calibrated weighing scales shall be available and in good working
order.
• Hoses shall be complete with leak-free disconnect couplings and in good condition.
• Before using the recovery machine, check that it is in satisfactory working order, has
been properly maintained and that any associated electrical components are sealed
to prevent ignition in the event of a refrigerant release.
Consult manufacturer if in doubt.
• The recovered refrigerant shall be returned to the refrigerant supplier in the correct
recovery cylinder, and the relevant Waste Transfer Note arranged.
• Do not mix refrigerants in recovery units and especially not in cylinders.
• If compressors or compressor oils are to be removed, ensure that they have been
evacuated to an acceptable level to make certain that
fl
ammable refrigerant does not
remain within the lubricant.
• The evacuation process shall be carried out prior to returning the compressor to the
suppliers.
• Only electric heating to the compressor body shall be employed to accelerate this
process.
• When oil is drained from a system, it shall be carried out safely.
9379124119-03_IM.indb 3
9379124119-03_IM.indb 3
2019/2/22 16:51:36
2019/2/22 16:51:36