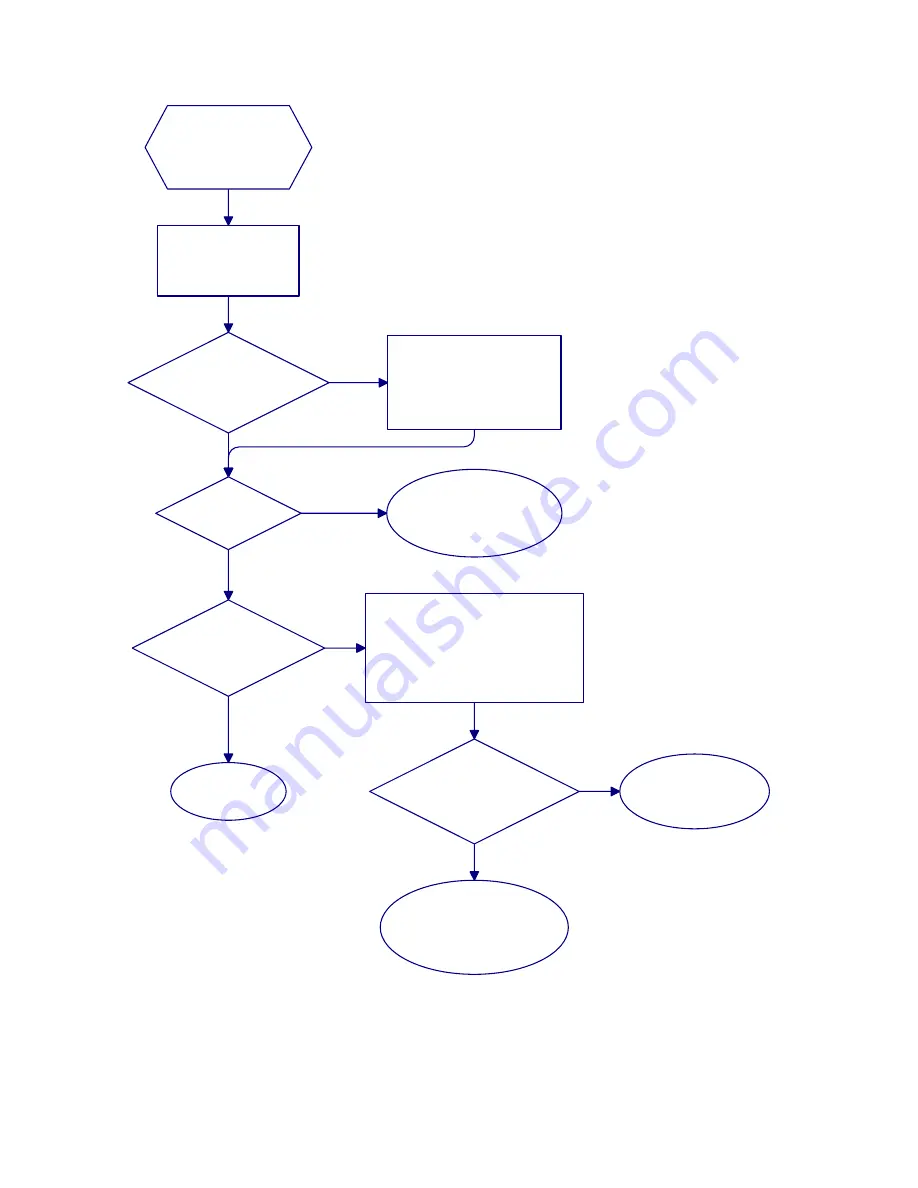
5-4
WATER NOT HEATING.
AUTOFILL (IF INSTALLED)
WORKED PROPERLY.
Press the Temperature
Check button twice to
display setpoint.
Has the correct setpoint
been programmed?
Did burners
light?
Did water reach
setpoint temperature?
Problem
resolved.
Insert a good grade thermometer into
cookpot with tip near temperature
probe and wait two minutes. Press
the Temperature Check button once to
display cookpot temperature.
Is temperature
displayed reasonably
close to thermometer
reading?
Temperature control
features are working properly.
If water still fails to reach
setpoint, call FASC.
There is a problem in
temperature probe
circuit. Call FASC.
Refer to troubleshooting
guide "BURNERS DO NOT
LIGHT".
Program setpoint in
accordance with instructions
in Chapter 3.
Yes
No
Yes
No
Yes
No
Yes
No
Содержание FBR18LP
Страница 3: ......
Страница 61: ...7 10...