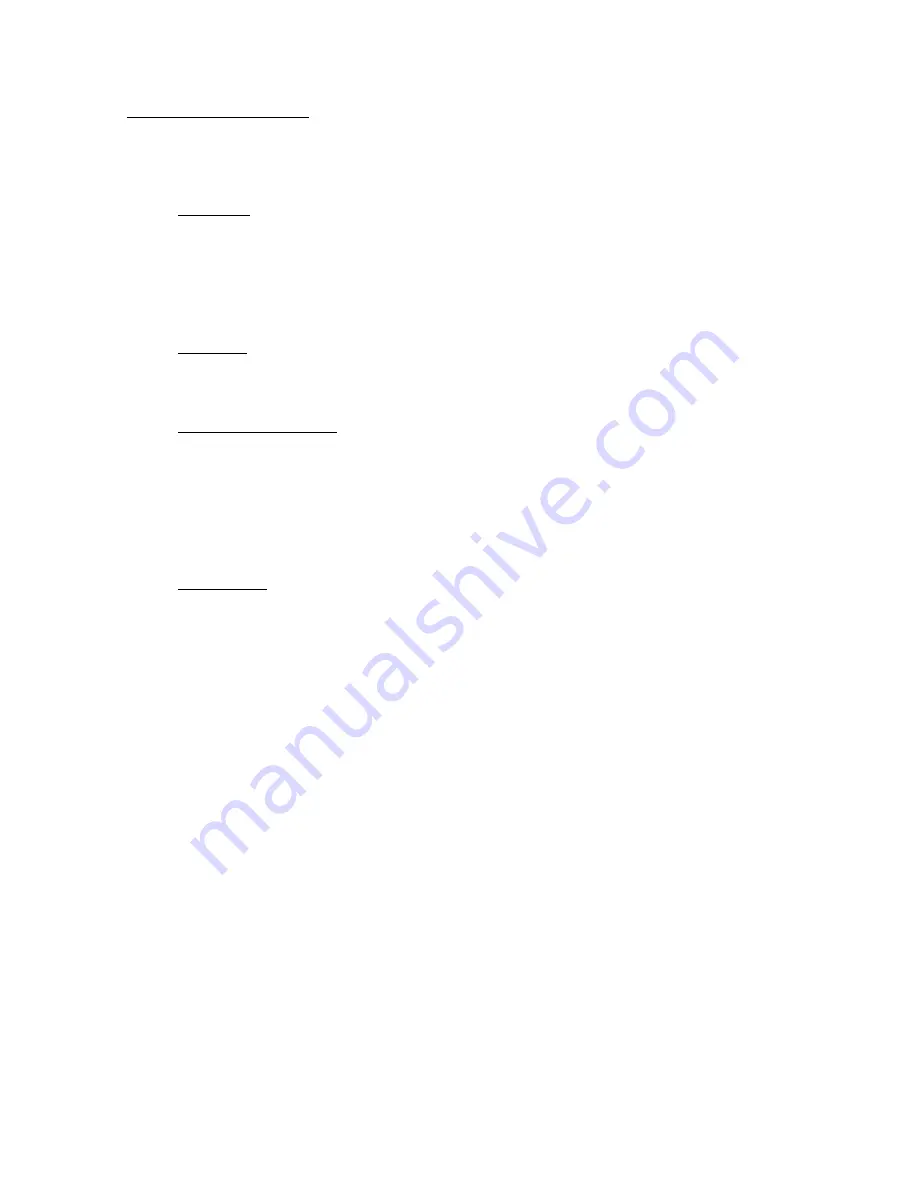
USERS’ RESPONSIBILITY
Card situated near the unit indicating a) name & address of the installer or person responsible
for service of the system
b)
nature of refrigerant, chemical formula & designation number
c)
instructions for shutting down the system in case of emergency
d)
maximum allowable pressures
Log Book recording: a) all details of maintenance and repair work
b) the quantities and kind of refrigerant (new, reused or recycled) refrigerant
which have been charged on each occasion, the quantity transferred from the system on
each occasion and the source of the reused refrigerant
c)changes and replacements of components to the system
d)
results of all periodic routine tests
e)
significant periods of non-use
inspection: a) should be carried out after repair or significant alterations
b)
should be carried out after reinstalling on another site
c)
refrigerated equipment should be P.A.T tested (Portable Appliance Test) to the
legal requirements
maintenance & repair : each refrigeration system must be subjected to preventative
maintenance every three months
a) the parties concerned for the refrigerating system must ensure that the system is
inspected, regularly supervised and maintained in a satisfactory manner
b)
the parties concerned shall also be responsible when the system is used by another
person unless a division of responsibility has been agreed upon
c)
regular maintenance or adjustment of the refrigerating system can only be carried out
by a qualified refrigeration engineer
maintenance shall be carried out every three months by a qualified refrigeration engineer
and will include the following procedures:
a)
clean condensers
b)
clean drains
c)
clean evaporators
d)
clean all fan blades
e)
test condenser & evaporator fan motors
f)
clean & check condensate trays
g)
check condensate heater
h)
check all controls & panel
i)
check defrost system
j)
test defrost time clock
k)
check all pipework
l)
check gas pressure on compressors
m)
test Klixon overload
n)
test capacitors
o)
test contactors
p)
test transformer
q)
chek all electrical connections & wiring condition
r)
check fuses & electrical sockets
s)
check customer’s power supply
t)
check condition of electrical control panel including signs of overheating of all
electrical components and wiring loom. Repair or replace as necessary
u)
check tightness of all terminals
v)
check integrity of seals on components
In the interest of continual product development we reserve the right to change any of the
details and specifications without notice.
Page 10