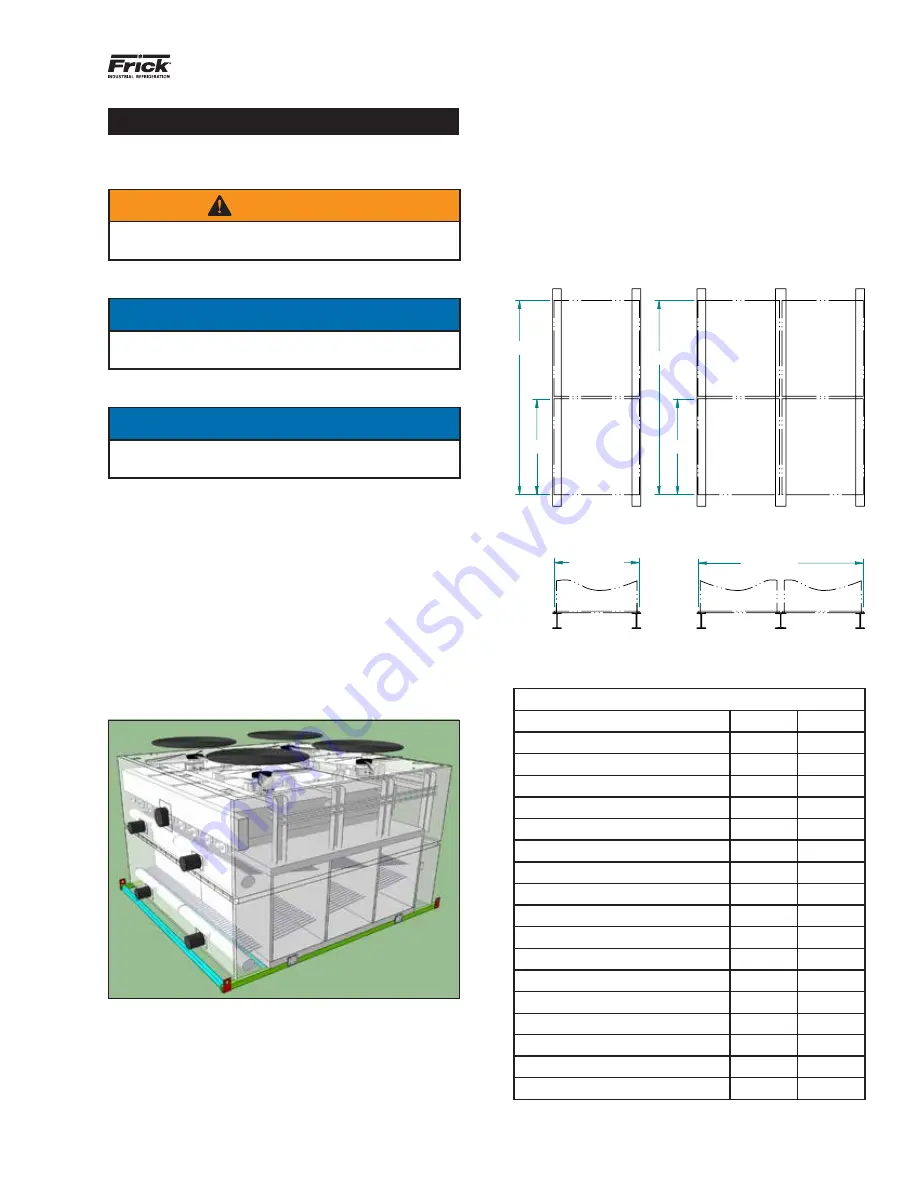
140.010-IOM (APR 2018)
Page 7
IDSC/ECOSS
™
EVAPORATIVE CONDENSERS
INSTALLATION
INSTALLATION
TRANSPORTATION, STORAGE,
UNPACKING AND MOUNTING
WARNING
Crushing danger with falling down! (see Appendix I, 4
Transportation, Storage, Unpacking & Mounting)
TRANSPORTATION
NOTICE
Read and observe all transport signs on the units' pack
-
aging! (see Appendix I, 4.1 Transportation)
STORAGE
NOTICE
Danger of corrosion and dirt build-up! (see Appendix
I, 4.2 Storage)
See additional information in General Information section.
UNPACKING
The two parts of the unit are packed and shipped separately
on their own substructure. See Figure 10.
After removing both sections of the unit from the truck:
ü
remove plastic wrapping
ü
loosen bolts connecting the unit to the substructure
ü
remove clamps, etc.
ü
remove any accessories shipped loose in the basin (boxed)
ü
ensure that delivery is complete and without damage. In
case of damage or missing parts, contact the manufacturer
immediately
Figure 10 - Upper Section of Unit On Substructure
MOUNTING
Condensers will need to be structurally supported with two
parallel I-beams traversing the entire length of the unit.
(See Figure 11) I-beams must be level to within 1/8” over a
6’ span. Shims cannot be used to level the unit as this will
compromise the load bearing surface.
Mounting holes (13/16” diameter) are provided at the base of
the basin section, in the side panel flanges, to enable secur-
ing each unit to the support structure utilizing ¾” diameter
bolts. Refer to the Frick unit certified drawing for the bolt
hole locations.
All support beams and anchoring bolts will be provided
by others and must be selected in accordance with sound
structural engineering standards. When selecting the sup-
port beams, each beam should be calculated with a uniform
load equivalent to 2/3 (66%) of the unit’s operating weight.
A1 & A2
A3 & A4
B3
B4
B2
B1
Figure 11 - IDSC/ECOSS
™
Steel Support Dimensions (See
Table for Dimensions)
IDSC/ECOSS
™
Steel Support Dimensions
10' Wide Models
A1
B1
IDSC 1012-06-10 to -12-30
9' 9¾"
11' 11¾"
IDSC 1018-06-15 to -12-30
9' 9¾"
18' 4"
A2
B2
IDSC 1024-06-20 to -12-60
9' 9¾"
24' 1½"
IDSC 1036-06-20 to -12-80
9' 9¾"
36' 10"
12' Wide Models
A1
B1
IDSC 1212-08-15 to -12-40
11' 10"
11' 11¾"
IDSC 1218-08-20 to -12-50
11' 10"
18' 4"
A2
B2
IDSC 1224-08-30 to -12-80
11' 10"
24' 1½"
IDSC 1236-06-60 to -12-100
11' 10"
36' 10"
24' Wide Models
A3
B3
IDSC 2412-08-30 to -12-80
23' 10"
11' 11¾"
IDSC 2418-06-60 to -12-100
23' 10"
18' 4"
A4
B4
IDSC 2424-10-60 to -12-120
23' 10"
24' 1½"
IDSC 2436-08-80 to -12-200
23' 10"
36' 10"