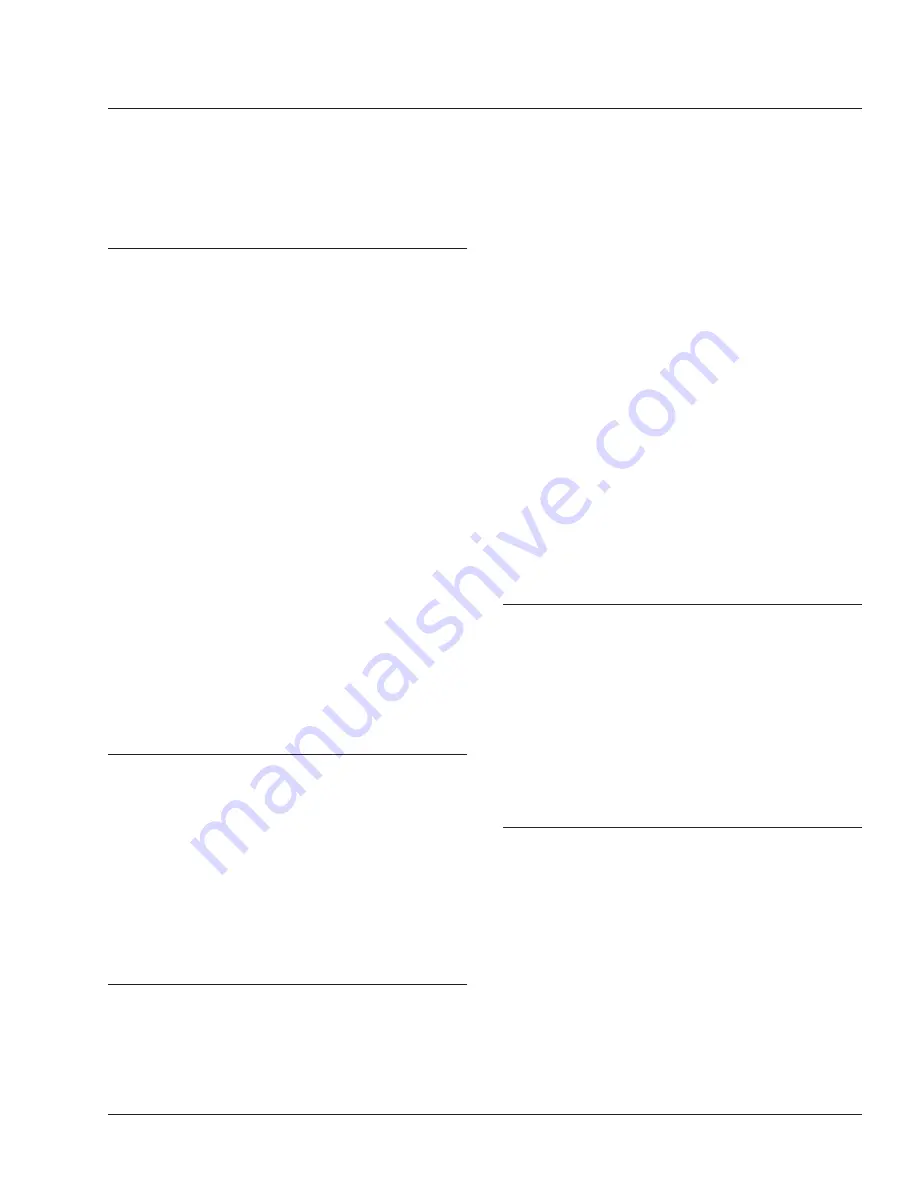
42–01 Air Dryer Checking,
Bendix AD–9
During cold-weather operation, check the operation
of the end cover heater and thermostat assembly.
1.
With the ignition switch in the ON position, check
for voltage to the heater and thermostat assem-
bly. Unplug the electrical connector at the air
dryer, and place the test leads of a voltmeter on
each of the pins of the male connector. If there is
no voltage, look for a blown fuse, broken wires,
or corrosion in the vehicle wiring harness. Check
that a good ground path exists.
2.
Check the thermostat and heater operation. Turn
the ignition switch to the OFF position and cool
the end cover assembly to below 40°F (4°C).
Using an ohmmeter, check the resistance be-
tween the electrical pins in the female connector.
The resistance should be 1.5 to 3.0 ohms for the
12-volt heater assembly.
Warm the end cover assembly to over 90°F
(32°C) and again check the resistance. It should
exceed 1000 ohms. If it does, the thermostat and
heater assembly is operating properly. If it does
not, replace the purge-valve housing assembly,
which includes the heater and thermostat assem-
bly.
42–02 Air Dryer Desiccant
Replacing, Bendix AD–9
The desiccant change interval may vary from vehicle
to vehicle. Although typical desiccant cartridge life is
three years, many will perform adequately for a
longer period of time. To take maximum advantage of
desiccant life and ensure that replacement occurs
only when necessary, disassemble, clean, and in-
spect the air dryer. Replace the desiccant cartridge if
necessary. For instructions, see Group 42 of the
School Bus Chassis Workshop Manual
.
42–03 Air Dryer Inspecting,
Bendix AD–9
1.
Check the reservoirs for moisture. A small
amount (teaspoon or less) is normal. Larger
amounts may mean that the desiccant needs to
be replaced. Check the mounting and connecting
lines.
2.
Tighten the fasteners that attach the air dryer to
the vehicle. Use the following torque values.
28 lbf·ft (38 N·m) for SAE grade 5, 3/8–16 fas-
teners.
135 lbf·ft (183 N·m) for SAE grade 5, 5/8–11 fas-
teners.
Check all air lines, fittings, and electrical connec-
tions for damage, leakage, or looseness.
3.
Replace damaged or leaking parts, and tighten
loose fittings or electrical connections.
42–04 Air Reservoir Automatic
Drain Valve
Disassembling,
Cleaning, and
Inspecting, Bendix DV–2
Disassemble the drain valve, clean the parts with
mineral spirits, and inspect the parts. Replace all rub-
ber parts and any worn or damaged parts; use only
genuine Bendix replacement parts or kits. Assemble
and install the valve, then check for proper operation
and leakage. For instructions, see Group 42 of the
School Bus Chassis Workshop Manual
.
42–05 Automatic Slack
Adjuster Lubricating and
Checking, Meritor
1.
Lubricate the slack adjusters using high-
temperature, water-proof grease NLGI grade 1,
Texaco Thermotex EP 1, Shell Darina No. 1,
Marathon 528 heavy-duty, Sunaplex No. 1 EP,
Amdex No. 1 EP, or Philube B No. 1. It should
be smooth-textured, corrosion-resistant grease,
free of fillers and abrasives. See
2.
Check the boots for cuts, tears, etc., and replace
them if necessary.
3.
Check the brake shoe lining wear to determine
the proper reline time.
Brakes
42
School Bus Chassis Maintenance Manual, March 2003
42/1