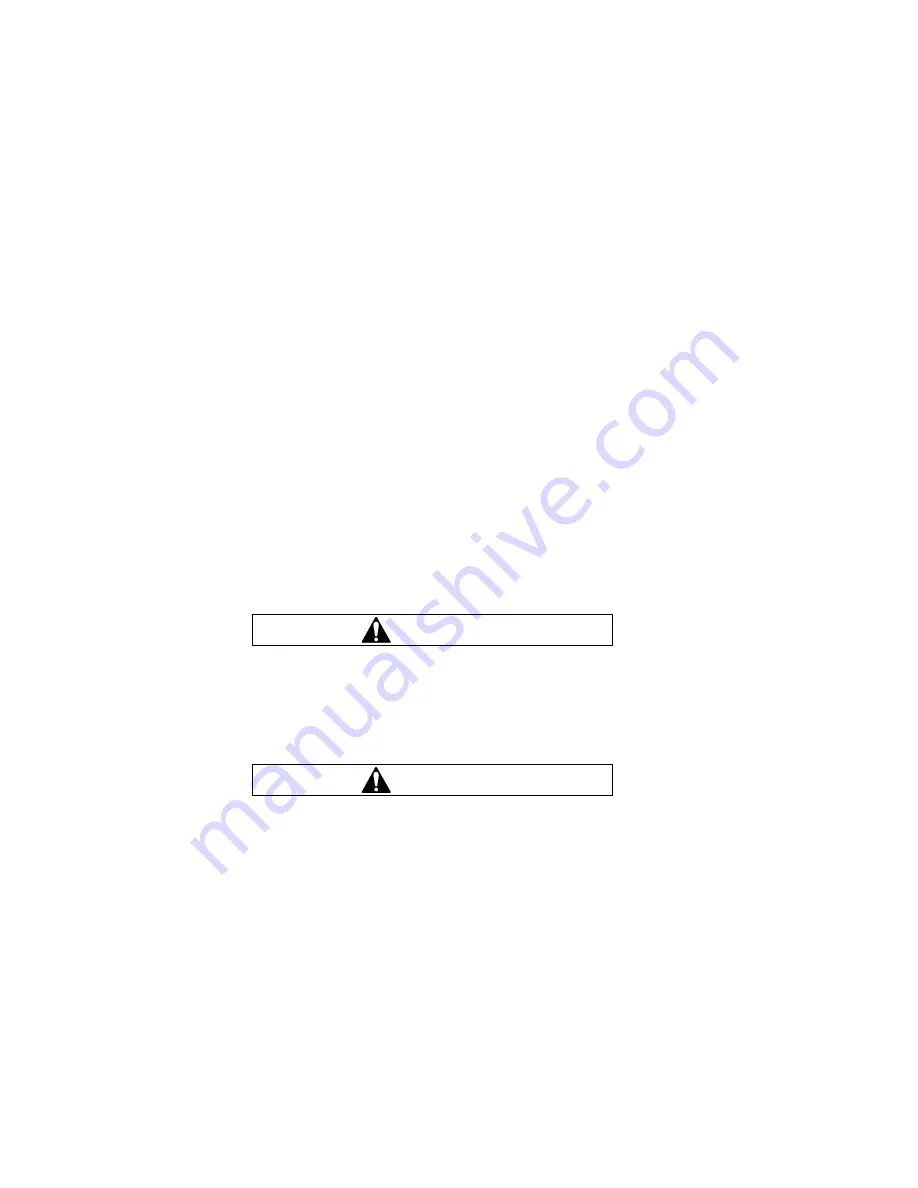
Foreword
Performing scheduled maintenance operations is important in obtaining safe, reliable operation of your vehicle. A
proper maintenance program will also help to minimize downtime and safeguard warranties.
IMPORTANT: The maintenance operations in this manual are
not all-inclusive
. Also refer to other
component and body manufacturers’ instructions for specific inspection and maintenance instructions.
Perform the operations in this maintenance manual at scheduled intervals. Perform the pretrip and post-trip
inspections, and daily/weekly/monthly maintenance, as outlined in the vehicle driver’s manual. Major components,
such as engines, transmissions, and rear axles, are covered in their own maintenance and operation manuals, that
are provided with the vehicle. Perform any maintenance operations listed at the intervals scheduled in those
manuals. Your Freightliner Dealership has the qualified technicians and equipment to perform this maintenance for
you. They can also set up a scheduled maintenance program tailored specifically to your needs. Optionally, they can
assist you in learning how to perform these maintenance procedures.
IMPORTANT: Descriptions and specifications in this manual were in effect at the time of printing.
Freightliner Trucks reserves the right to discontinue models and to change specifications or design at any
time without notice and without incurring obligation. Descriptions and specifications contained in this
publication provide no warranty, expressed or implied, and are subject to revision and editions without
notice.
Refer to
www.Daimler-TrucksNorthAmerica.com
and
for more information, or
contact Daimler Trucks North America LLC at the address below.
Environmental and Safety Concerns and Recommendations
Whenever you see instructions in this manual to discard materials, you should attempt to reclaim and recycle them.
To preserve our environment, follow appropriate environmental rules and regulations when disposing of materials.
Servicing vehicles may result in contact with items known to the state of California to cause harm.
WARNING
Breathing diesel engine exhaust exposes you to chemicals known to the State of California to cause can-
cer and birth defects or other reproductive harm.
Always start and operate the engine in a well-ventilated area. If in an enclosed are, vent the exhaust to the
outside. DO not modify or tamper with the exhaust system. Do not idle the engine except as necessary.
For more information go to
WARNING
Cancer and Reproductive Harm
NOTICE: Parts Replacement Considerations
Do not replace suspension, axle, or steering parts (such as springs, wheels, hubs, and steering gears) with used
parts. Used parts may have been subjected to collisions or improper use and have undetected structural damage.
Содержание BUSINESS CLASS M2 100
Страница 2: ......
Страница 10: ......
Страница 30: ......
Страница 34: ......
Страница 36: ......
Страница 38: ......
Страница 40: ......
Страница 42: ......
Страница 46: ......
Страница 52: ......
Страница 60: ......
Страница 62: ......
Страница 74: ...11 Remove the chocks from the tires Transmission 26 Business Class M2 Maintenance Manual March 2016 26 12 ...
Страница 76: ......
Страница 82: ......
Страница 84: ......
Страница 94: ......
Страница 104: ......
Страница 110: ......
Страница 112: ......
Страница 114: ......
Страница 116: ......
Страница 120: ......
Страница 122: ......
Страница 144: ......
Страница 146: ......
Страница 150: ......
Страница 152: ......
Страница 166: ......
Страница 168: ......
Страница 178: ......
Страница 180: ......
Страница 184: ......
Страница 186: ......
Страница 188: ......
Страница 190: ......
Страница 192: ......
Страница 196: ......
Страница 198: ......