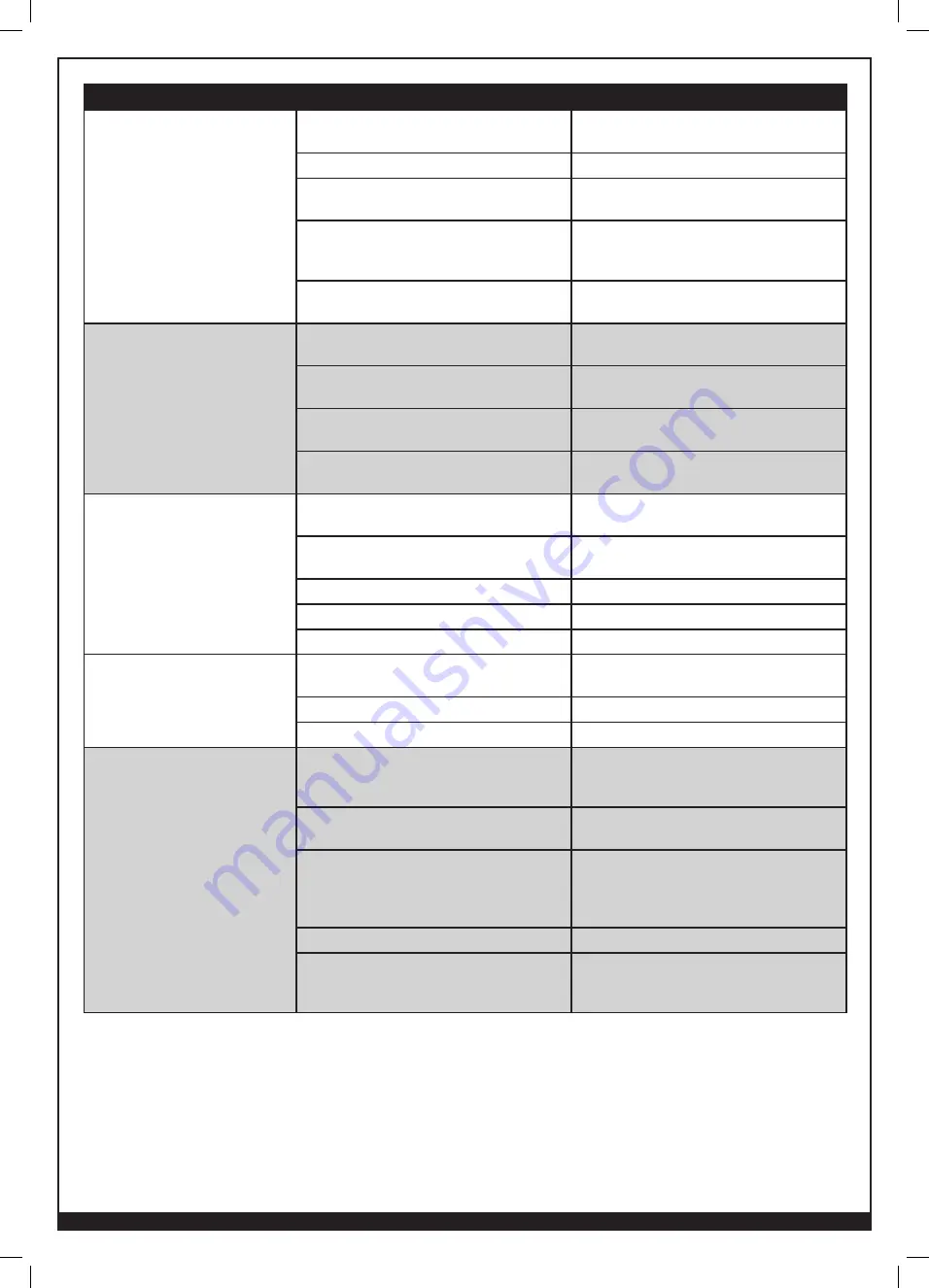
22
WWW.FORNEYIND.COM
PROBLEM
POSSIBLE CAUSE
POSSIBLE SOLUTION
Birdsnesting.
Wire is not aligned with torch neck inlet guide. Ensure that the welding wire is aligned to flow
smoothly onto the torch neck inlet guide.
Wire feed too low.
Increase wire feed speed.
Tension too low / too high.
Use as little tension as necessary for smooth
operation.
Welding wire is fused to contact tip.
Attempt to pull wire out of front of contact tip
with pliers. If necessary, remove contact tip
and cut welding wire. Discard contact tip.
Contact tip is too small for wire diameter.
Always use a contact tip that is one size
larger than the welding wire.
No gas flow.
Machine is in wrong process (SMAW or
GTAW).
Ensure machine is set to MIG mode (manual
2T, manual 4T, synergic 2T, synergic 4T).
Gas cylinder is closed.
Ensure that gas cylinder is fully opened. Set
flowmeter to 25-30CFH.
Gas cylinder is empty.
Ensure that the gas cylinder is not empty. If
necessary, replace gas cylinder.
Blockage in tank valve.
Remove regulator from tank. Purge tank to
clear blockage.
Soot covered / discolored welds.
Wrong shielding gas.
Always use 100% pure argon shielding gas
when welding aluminum.
“Pulling” arc instead of “pushing” arc.
When welding aluminum, push the nozzle in
the direction of the weld rather than pulling.
Gas connection loose; sucking in atmosphere.
Ensure all gas fittings are tight.
Gas flow too low.
Increase gas flow.
Gas flow too high.
Decrease gas flow.
Welding wire fused to contact tip.
Using contact tip that is the same size as
welding wire.
Always use a contact tip that is one size larger
that the welding wire.
Burn Back Time (BBT) set too high.
Turn burn back time (BBT) down.
Wire feed speed too low.
Increase wire feed speed.
Excessive spatter.
Material surface preparation needed.
Always weld on clean bright metal. Aluminum
builds up an oxide layer that is non-conductive
and extremely difficult to melt.
Wrong shielding gas.
Always use 100% pure Argon shielding gas
when welding aluminum.
Not enough shielding gas.
Ensure that gas cylinder is fully open. Set
flow meter to 25-30CFH. Ensure that the gas
cylinder is not empty. If necessary, replace gas
cylinder.
Wire feed too fast.
Decrease wire feed speed.
Stick out too long.
Shorten the distance between the gas nozzle
and the material being welded. Maintain a
distance of 3/8” to 5/8”.