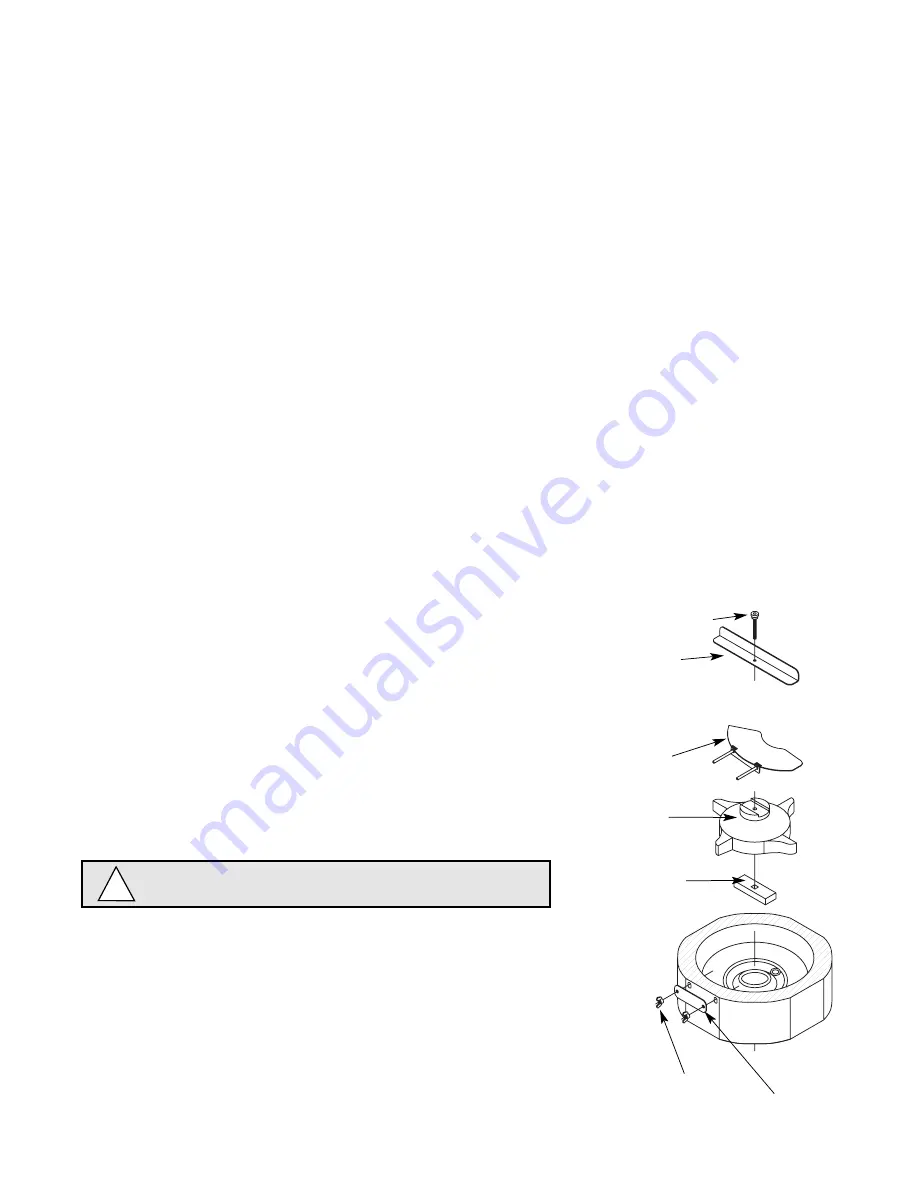
10
Dispenser cleaning: start-up and quarterly intervals
1. Remove all ice from storage hopper.
2. Remove top and front cover (see page 30).
3. Remove center thumbscrew, locking plate, two wingnuts and
backing plate from front of storage hopper.
4. Remove stud assembly, agitator, spacer, baffle, wheel and drive
bar in this sequence.
User information
How the dispenser works
Follett’s 12 series automatic-load ice and water dispensers are equipped with Follett’s 400 lb (181kg)/day
icemaker. In the continuous icemaking process, water freezes to the inside wall of the evaporator. A rotating
stainless steel auger carries the ice to the top of the evaporator where it is compressed and extruded through an
outlet port. The ice is then pushed through a tube to the storage hopper. When the hopper is full, a bin thermostat
opens and shuts the icemaker off. When the dispense mechanism is activated, a dispense motor is turned on,
causing the wheel to turn. This moves ice to the dispense chute where it drops by gravity into the container held
below the chute.
How the SensorSAFE accessory works
Follett’s SensorSAFE accessory maximizes sanitation and minimizes the possibility of cross-contamination by
eliminating physical contact between the cup or container and dispenser. Sensors in the panel use reflected
infrared light to detect the presence of the container and send a signal to a control board which then activates the
appropriate components for ice or water dispensing.
The SensorSAFE package includes a cleaning switch under the left side of the front cover which
temporarily shuts off dispensing to allow cleaning of the panel and lenses. If the switch is not turned back on after
cleaning, the dispenser automatically resets after two minutes for normal operation.
SensorSAFE also includes a time limit safety feature which automatically stops ice dispensing after
one minute of continuous dispensing. Dispensing can be resumed by moving the container away from
the dispenser and returning it to the activation zone.
Cleaning and sanitizing procedures
Solution A:
Prepare cleaning solution (200 ppm of available
chlorine content) of Ecolab Mikro-chlor Cleaner or
equal chlorinated detergent. Solution temperature
must be 75
˚
F – 125
˚
F (24
˚
C – 52
˚
C).
Solution B:
Prepare sanitizing solution (50 ppm of available
chlorine content) of Ecolab Mikro-chlor Cleaner or
equal chlorinated detergent. Solution temperature must
be 75
˚
F – 125
˚
F (24
˚
C – 52
˚
C).
Follett recommends the periodic cleaning schedule below to ensure the
quality of ice provided. Use only recommended cleaning solutions. Do
not use solvents, abrasive cleaners, metal scrapers or sharp objects.
Warning – Always disconnect power before cleaning.
!
stud assembly
agitator
wheel
drive bar
baffle
backing
plate
wingnut