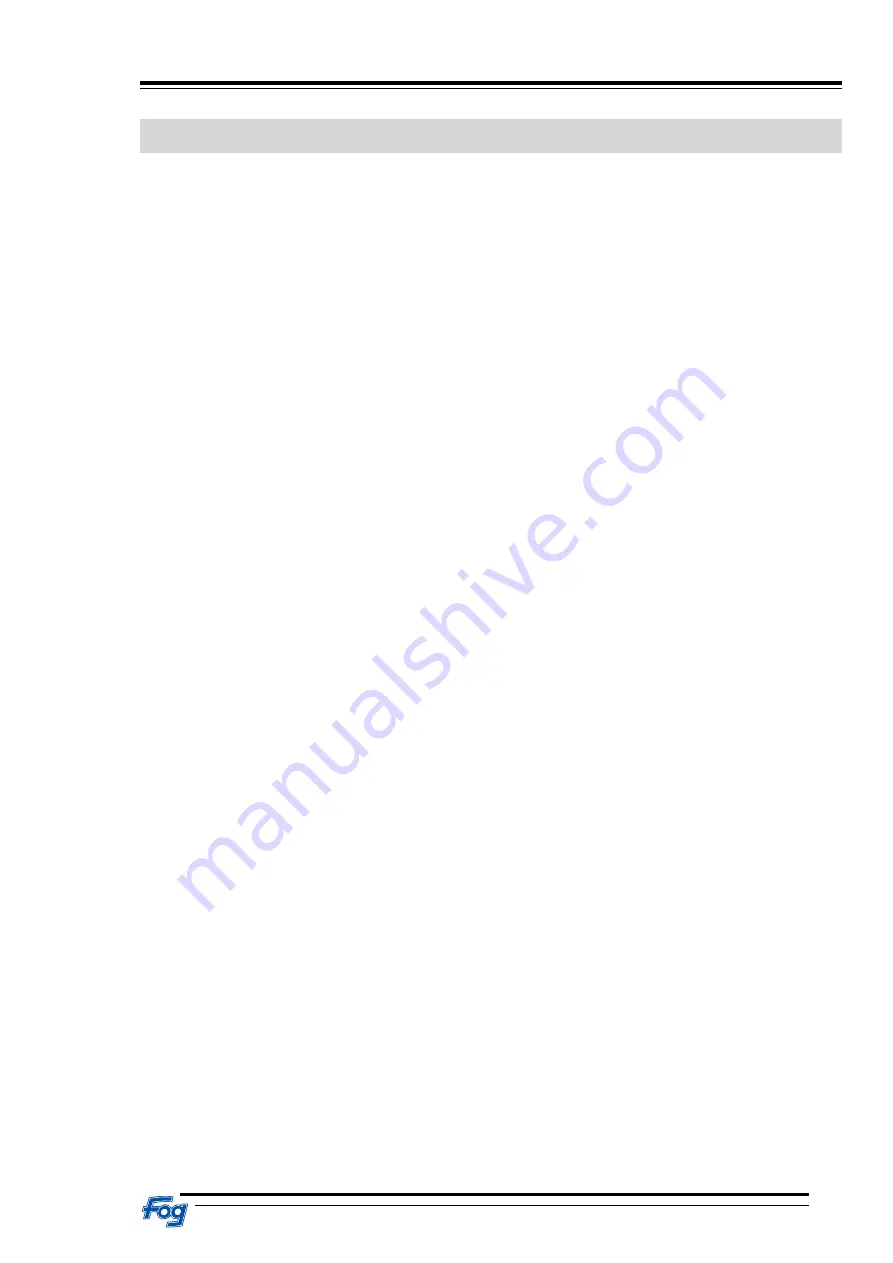
444 9160 / 444 9180 / 442 9020
11
E 219 GB - Issue 1
3. Product Description
This lift consists mainly of two equal lift columns which are driven by an electric motor: the control column
with integrated base plate and the auxiliary column with an integrated base plate. There is no
mechanical connection between the lift columns. Each of the columns contains lifting spindles and a lifting
carriage with the load accepting devices.
The two electrical motors drive the lifting spindles by means of a sturdy and low-noise ribbed V-belt.
Integrated thermo-sensors in the motor coil winder act as an overload monitor.
The spindles house the various types of nuts: - supporting nuts with safety nuts - which are connected with the
two lifting carriages and, depending on the direction of the drive, carry out the up or down movements. The
two lifting carriages are guided by four gliding pieces in each column. The spindle supporting nut system
with carriages are maintenance free for one year if used as repair lift.
The necessary synchronisation of the carriage is guaranteed by an electronic synchronisation monitor. In the
event that the two carriages are not in parallel (for example, due to one-sided load, insufficient lubrication,
etc.) the synchronisation monitor will adjust the deviation within a distance of approx. 10 mm. This is done
by stopping the advanced carriage until the carriage which is lagging behind is at the same level again.
This process can be observed during a lifting action, possibly several times.
The drive is activated depending on the input by means of a key pad on the control panel; it is switched
on via an analogue path measuring counter in the upper and lower end position. After releasing the key
pad these return to “0” position automatically and the movement of the lift is stopped in each position of
the load uptake device.
The lift is fitted with safety devices, for example, the supporting nut break safety device which will transfer the
load to a free running safety nut in the case of a worn thread. During this process a mechanical safety system
is activated which will switch off the lift via the analogue path measuring counter and prevent a restart.
There is also the oscillating arm arrest which locks the lifting arms in their oscillating movement after a
lifting distance from the base position of approximately 100 mm in order to avoid that the supported
vehicle slips of the load bearing de vice.
The foot protection is activated via the analogue path measuring counter which stops the lowering of the
load automatically in the danger area (120 mm above the platform base). By pressing the key pad
“SENKEN” (down) again, the load carrier can be brought back into base position. This down-action in
the danger area will activate a warning signal tone.
The thermo-sensor in the drive motors causes the motors to switch off when they are too hot and after a
cooling-off time (of approx. 10-15 minutes) indicates that the lift can be used again.
An arch, which can be simply assembled, is placed above the control column to the auxiliary column, ,
serving as a safety channel for electrical cables (power supply, monitoring and control cables).
The lifting arms are, depending on the type, constructed resembling a single or double telescope which
can be adjusted to the required working length. The long single telescopic lifting arms in direction “up” at
the back and the short single or double telescopic lifting arms “up” in the front. This ensures that the doors
are free on both sides.
The vehicle to be raised is to be placed in such a way that the front door hinges are in the area of the lift
columns, so that a large door opening angle is created
The aim should be to direct the motor side of the vehicle towards the short oscillating arms (centre of
gravity of the vehicle should be at the centre of the lift if possible).
Содержание 442 9020
Страница 13: ...444 9160 444 9180 442 9020 13 E 219 GB Issue 1 ...
Страница 14: ...444 9160 444 9180 442 9020 E 219 GB Issue 1 14 ...
Страница 15: ...444 9160 444 9180 442 9020 15 E 219 GB Issue 1 ...
Страница 17: ...444 9160 444 9180 442 9020 17 E 219 GB Issue 1 Lifting arms for type 442 9020 ...
Страница 21: ...444 9160 444 9180 442 9020 21 E 219 GB Issue 1 ...
Страница 23: ...444 9160 444 9180 442 9020 23 E 219 GB Issue 1 ...
Страница 42: ...444 9160 444 9180 442 9020 E 219 GB Issue 1 42 13 Electrical diagrams ...
Страница 43: ...444 9160 444 9180 442 9020 43 E 219 GB Issue 1 ...
Страница 44: ...444 9160 444 9180 442 9020 E 219 GB Issue 1 44 ...
Страница 45: ...444 9160 444 9180 442 9020 45 E 219 GB Issue 1 14 Spare parts ...
Страница 46: ...444 9160 444 9180 442 9020 E 219 GB Issue 1 46 ...
Страница 47: ...444 9160 444 9180 442 9020 47 E 219 GB Issue 1 ...
Страница 48: ...444 9160 444 9180 442 9020 E 219 GB Issue 1 48 ...
Страница 49: ...444 9160 444 9180 442 9020 49 E 219 GB Issue 1 ...
Страница 50: ...444 9160 444 9180 442 9020 E 219 GB Issue 1 50 ...
Страница 51: ...444 9160 444 9180 442 9020 51 E 219 GB Issue 1 ...
Страница 52: ...444 9160 444 9180 442 9020 E 219 GB Issue 1 52 ...
Страница 53: ...444 9160 444 9180 442 9020 53 E 219 GB Issue 1 ...
Страница 54: ...444 9160 444 9180 442 9020 E 219 GB Issue 1 54 ...
Страница 55: ...444 9160 444 9180 442 9020 55 E 219 GB Issue 1 ...
Страница 56: ...444 9160 444 9180 442 9020 E 219 GB Issue 1 56 ...
Страница 57: ...444 9160 444 9180 442 9020 57 E 219 GB Issue 1 ...
Страница 58: ...444 9160 444 9180 442 9020 E 219 GB Issue 1 58 ...
Страница 59: ...444 9160 444 9180 442 9020 59 E 219 GB Issue 1 ...
Страница 60: ...444 9160 444 9180 442 9020 E 219 GB Issue 1 60 ...
Страница 61: ...444 9160 444 9180 442 9020 61 E 219 GB Issue 1 15 Service book for Vehicle lifts 4449160 4449180 4429020 ...
Страница 70: ...444 9160 444 9180 442 9020 E 219 GB Issue 1 70 ...
Страница 71: ...444 9160 444 9180 442 9020 71 E 219 GB Issue 1 ...