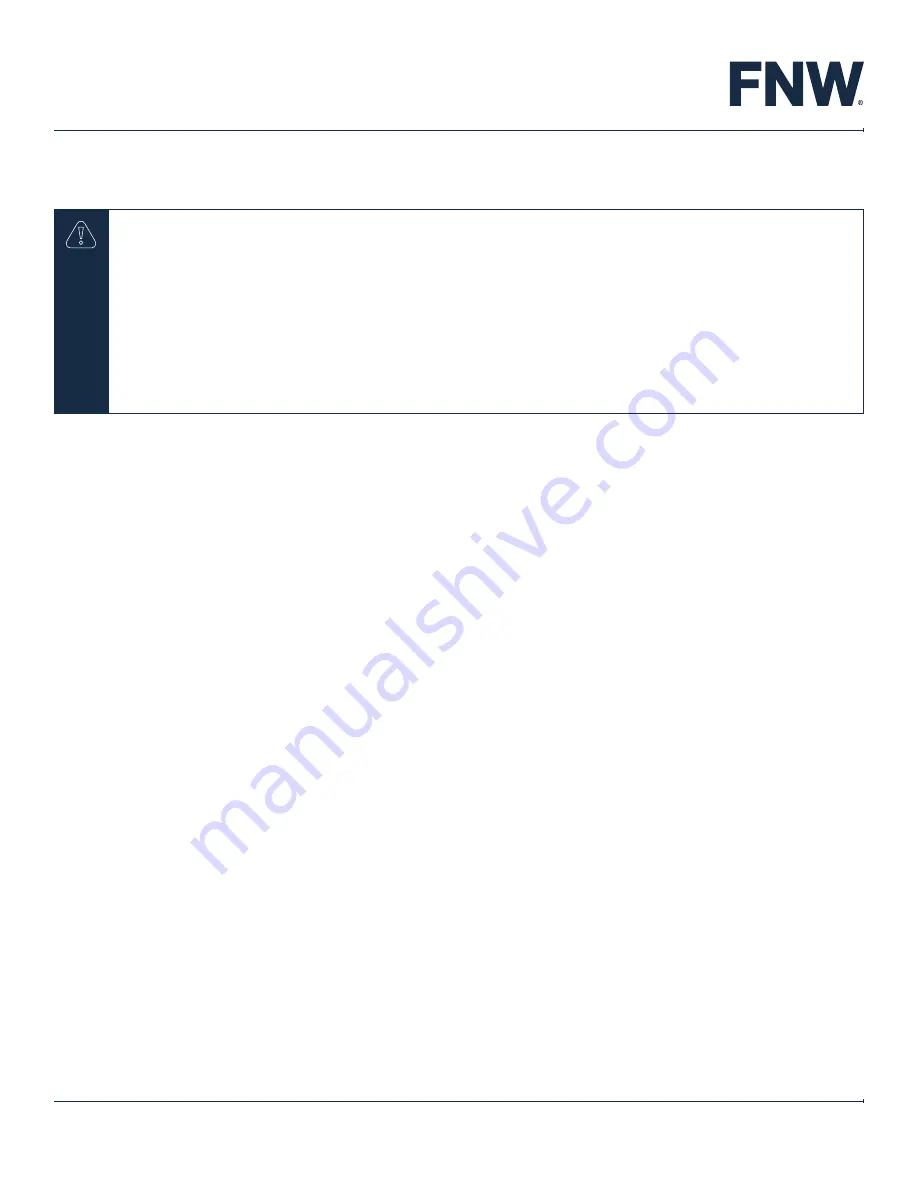
FNW.COM
©2021 Ferguson Enterprises, LLC 0721 2945816
We reserve the right to modify or improve the designs or
specifications of our products at any time without notice.
HIGH PERFORMANCE BUTTERFLY VALVE
FIGURE HPA
10
8. PERIODIC MAINTENANCE
8.1 GENERAL
8.1.1 For extended valve life and better operability,
FNW or manufacturer recommends periodic
inspection and maintenance of the valves as per
the procedure explained below. To avoid valve
failure during operation, all valves in a process
plant should be periodically inspected thoroughly
to detect the wear of disc, seats, seals and even
body. It is recommended that on such occasions
seats, seals and bushings should be replaced.
8.1.2 The type of process, fluids involved, working
conditions and location of the valves in the
process plants will determine the frequency of
periodic inspection/maintenance to be made at
the time of partial or total shutdown of the plant.
Preventive maintenance is essential as failure
to do so may cause an emergency shutdown of
the plant.
8.1.3 Use genuine FNW spare parts only for
maintenance and replacements. Refer to
Section 9.
8.1.4 Studs and nuts fixing pipeline flanges and valves
to be properly tightened and in position, if
found loose.
8.1.5 Gland nuts and bolts to be inspected and ensured
that they are intact and not loosened during
service. Properly tighten the nuts by means of
spanner or wrench if found loose. Over tightening
of gland nut may damage the gland seal packing
and stem.
8.1.6 Once the valve is repaired, it should undergo a
complete set of tests to make sure that the valve is
adequate for required working conditions. Hydro/
Pneumatic tests should be carried out as per the
specifications relevant to the valve (Refer to GAD
or specifications related to order).
8.2 OPERABILITY AND TORQUE
8.2.1 Check for ease of operation of the valve.
8.3 STEM LEAKAGE
8.3.1 Any major leakage at the stem region can easily
be detected by observing for unexpected
pressure drops in the pipeline.
8.3.2 Minor leakage at the stem region may be
detected by using soap bubbles, after removing
the operator (actuator/gear/lever) unit.
CAUTION:
•
For your safety, it is important that these precautions be taken before removal of the valve from the line or
before disassembly.
•
De-pressurize the line before removing the bolting.
•
Wear protective clothing and equipment appropriate for the line fluid.
•
Ensure cavity pressure is relieved.
•
Cycle the valve several times before disassembly to relieve pressure completely.
•
Disconnect valve from supply sources and make sure valve actuation is in fail safe state before performing
any maintenance work.