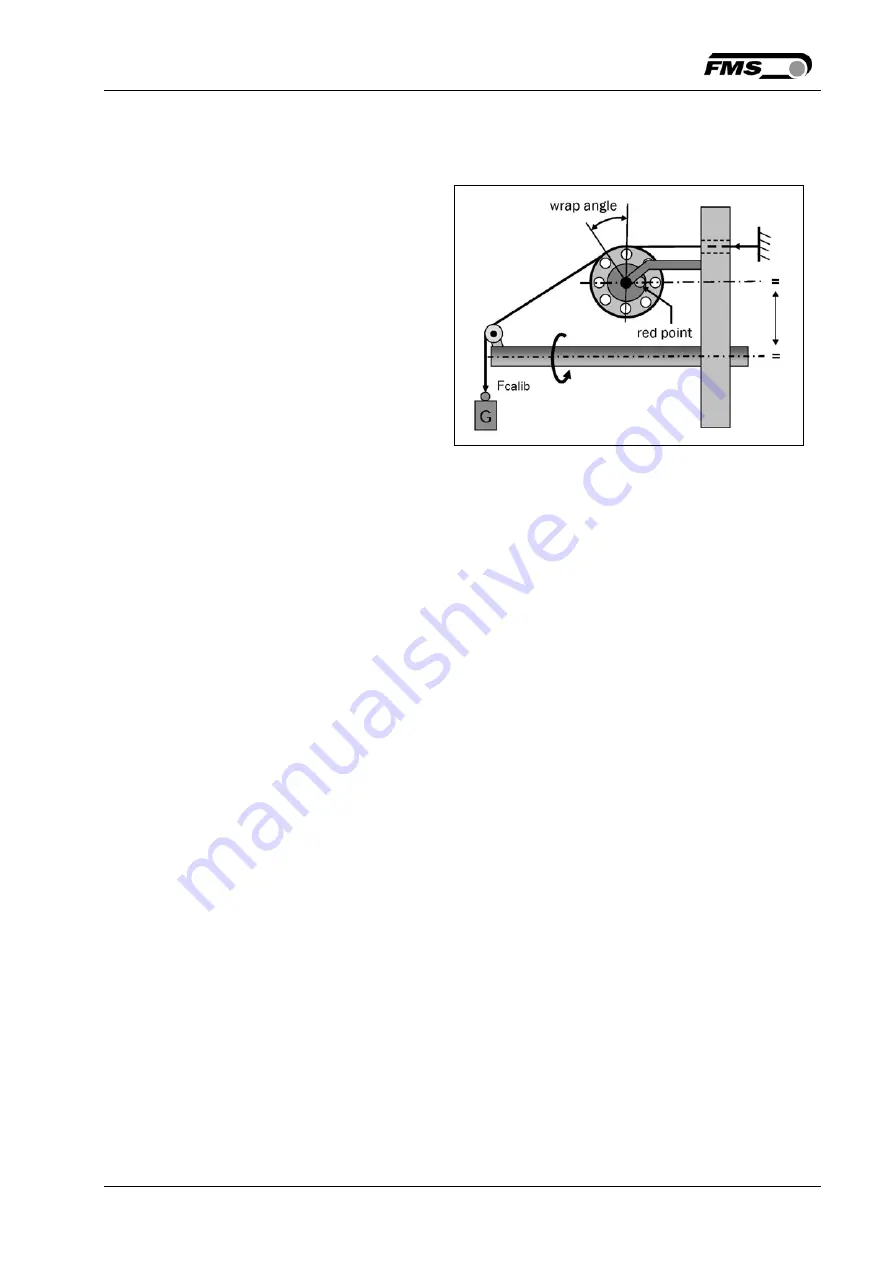
Operation Manual RTM MP System
06.09.2017
21
5.4
Calibration Methods
The Calibrating procedure (setting
the Gain), adjusts the controller
and force sensors so that the
output gives you the actual tension
value. There are two methods of
calibrating the system. The first
method uses a defined weight. The
second method is based on a
calculation method in conjunction
with the FMS Calculator. This
Calculator can be down loaded
from the FMS web page. FMS
recommends using the method
with the weight (see Fig. 13) since
it delivers the most accurate
results.
5.5
Calibration Procedure
1.
The calibration of the sensors must be performed with the PLC
2.
Load a rope on the roller with the weight corresponding to your calibration force.
The roller configuration must correspond to the real material path in the machine
(wrap angle, distances between the rollers etc.).
3.
The RTM MP-system will deliver tension raw data via the corresponding output
4.
Enter the force data in your PLC and calibrate it matching your controlling needs.
5.6
Relay Output for Lost Communication
The relay output on the receiver EMGZ482R.MP becomes active, if the
communication link between receiver and transmitter is lost. For the technical
specification of the relay output see chapter 8 “Technical Data”, Table
EMGZ482R.MP.
Fig. 13: Calibrating the measuring amplifier
RTM00020e
Содержание RTM MP EMGZ443MP.R
Страница 27: ...Operation Manual RTM MP System 06 09 2017 27 ...