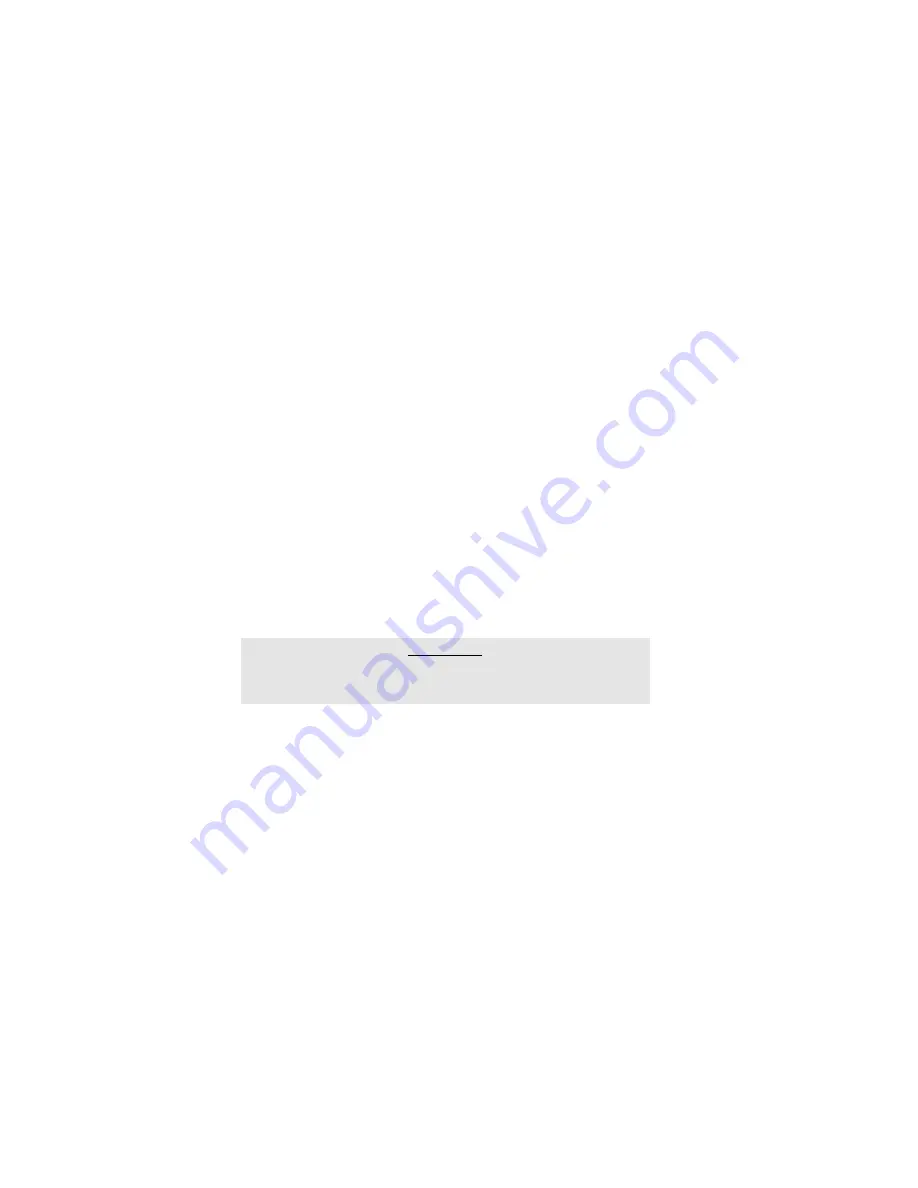
SVCN 7 INSTALLATION, OPERATION, & MAINTENANCE
1. Inspect all parts for cracks, corrosion, or other damage, which could lead to failure of the
part.
2. All painted surfaces should be inspected and touched up as necessary.
3. Inspect all abutting machined surfaces, gasket seating surfaces, and O-ring grooves and faces.
These surfaces must be perfectly smooth and free of damage, foreign matter, or corrosion.
Clean or replace these parts as necessary.
4. Check shaft (1) for straightness (see paragraph 4.4.3, “Checking Shaft Straightness”, below).
5. Inspect impeller (34) for cracks, damage, or erosion. Also check the impeller bore for correct
fit with the shaft (see paragraph 4.4.4, “Checking Fit Between Impeller Bore and Shaft”,
below). If eroded or damaged, the impeller must be repaired or replaced before final
assembly. If the impeller is repaired, it must be dynamically balanced before final assembly.
6. Inspect wearing surfaces of wear rings (26A/B, 200A/B), seal spacer sleeve (599) or shaft
sleeve, and packing box bushing (610) for damage, scouring, or erosion. Also check running
clearances of these parts (see paragraph 4.4.5, “Checking Running Clearances”, below).
7. If your pump is equipped with an inducer (3186), then inspect the inducer and the suction
nozzle insert (2852) for excessive wear, scouring, or erosion.
8. The mechanical seal (3213A) (if installed) should be disassembled and inspected in
accordance with the manufacturer’s instructions located in the back of this manual.
Specifically, the stationary and rotating seal faces should be inspected for wear or cracking
and replaced as necessary. When reassembling the seal, all old gaskets and O-rings should be
discarded and replaced with new parts.
4.4.3 CHECKING SHAFT STRAIGHTNESS
CAUTION
Application of heat to straighten shaft will cause more
distortion.
When making the check do not turn the shaft in its lathe centers. It is possible for the lathe centers of
a straight shaft to be off center slightly, resulting in a false indication of a bent shaft. Set shaft in soft-
faced V-blocks or precision rollers and check straightness by taking dial indicator readings all along
the shaft while it is rotated. Total runout of shaft must not exceed 0.0015 in (0.04 mm). If runout is
exceeded, the shaft must be cold-straightened or replaced.
4.4.4 CHECKING FIT BETWEEN IMPELLER BORE AND SHAFT
NOTE
A three-point micrometer is the preferred instrument for
measuring bore; a stick micrometer is its alternate. When
measuring with the three-point micrometer, measure close to
the keyway. With stick micrometer, measure three places at
120-degree intervals.
The fit between the impeller bore and the shaft must be correct or vibration can occur. To check the
fit, use a micrometer to measure diameter of bore under thickest metal near each end of the impeller
keyway and the corresponding diameter of shaft. Then subtract the diameter of the shaft from the
diameter of the impeller bore and divide by two to obtain the clearance. The clearance should be
DO2604-13
- 4-6 -
Содержание SVCN 7
Страница 2: ...SVCN 7 PUMP INSTALLATION OPERATION MAINTENANCE 1 ...
Страница 15: ......
Страница 57: ......
Страница 60: ...SVCN 7 INSTALLATION OPERATION MAINTENANCE 5 3 DO2604 13 ...