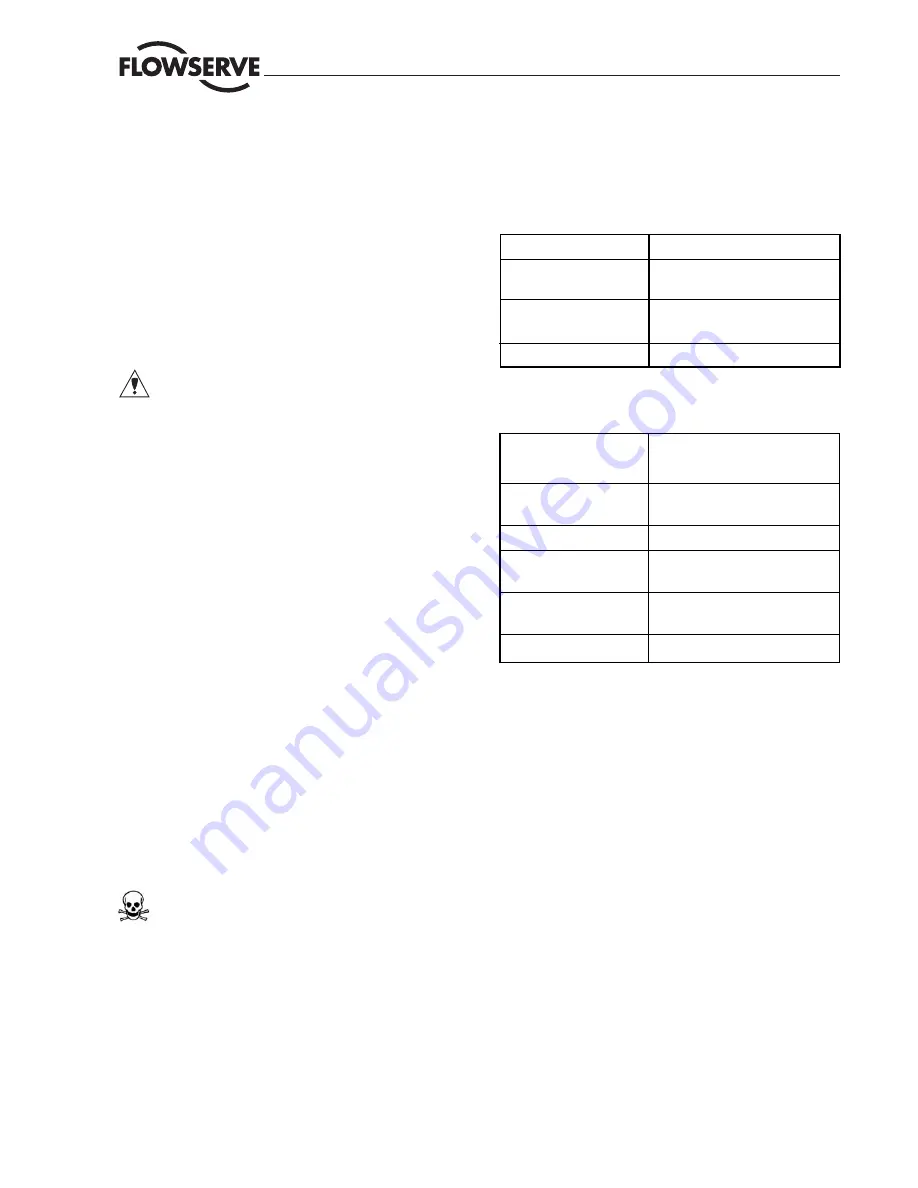
5
Flow Control Division
Kammer Control Valves
6
PRESSURE TESTING PIPING SECTION
The valve has already been pressure-tested by the
manufacturer. When pressure testing a section of the
pipeline with valves installed, observe the following:
6.1
First thoroughly flush newly installed piping systems to
remove all foreign objects.
6.2
Valve opened: The test pressure should not exceed the
value of 1.5 x PN (according to nameplate):
6.3
Valve closed: The test pressure should not exceed the
value 1.1 x PN (according to nameplate).
If a leak occurs on the valve, observe Section 8
“Troubleshooting”.
CAUTION:
If the flange connection with plastic liner
leaks:
First retighten flange connection to torque specified in
Table 1a or 1b in Section 5.6 (installation).
If the flange connection is still leaks:
Loosen flange connection. Check the flange connection
to ensure that it is smooth and parallel.
Check the sealing surfaces on both flanges: When the
inner lining is damaged, replace valve and/or
counterflange.
7
NORMAL OPERATION AND MAINTENANCE
These installation, operating and maintenance
instructions cannot contain all detailed information on
all possible versions for reasons of clarity and, in
particular, cannot take into consideration all imaginable
cases for setup, operation and maintenance. Therefore,
only primarily instructions are contained, which are
required for the intended use in industrial applications.
If anything is not clear, particularly if any detailed
information on the specific product is missing, clarify as
r e q u i r e d w i t h t h e r e s p o n s i b l e F L O W S E R V E
representative.
8
TROUBLESHOOTING
When troubleshooting or during general maintenance,
always observe Section 1 “Safety precautions”.
DANGER:
If a valve contaminated with dangerous
substances has to be removed from the system or
pipeline, decontaminate it properly before performing
further maintenance work.
9
PODUCT DESCRIPTION
9.1
Housing
The body material is made of GGG40.3 (standard), other
body materials are also available from the manufacturer
on request. For valve bodies with plastic liners: See
Table 2b for coating materials.
The liner thickness is at least 5 mm for DN25 and higher
and 3.5 mm for DN15 and DN20.
Table 2a: Body specifications
Body material
0.7043 (GGG40.3)
Pressure class
PN16
End connections
DIN PN 16
(flanged)
ANSI Class 150
Liner thickness
4 – 6 mm
Table 2b: Liner materials
PFA
Perfluoralkoxypolymer
(Standard)
PFA conductive
Perfluoralkoxypolymer,
electrically conductive
PVDF
Polyvinilidenfuoride
ETFE
Ethylene Tetrafluorethylene –
copolymer (Tefzel
®
)
FEP
Tetrafluorethylene –
Perfluorpropylene
PP
Polypropylene
10
BONNET
The bonnet is connected with a form fit to the valve body
providing, on the one hand, a potential compensation
between the housing and bonnet and on the other a
defined compression force for the body seal and
bellows. The bonnet is provided with a blowout safety
system. This means that the valve stem cannot be
pulled or pressed upward out of the bonnet.
11
PLUG AND SEAT
The seat and plug are screwed, i.e. replacement is
possible at any time when the Kvs value changes or for
repair. The plug is screwed to the bellows and secured
against loosening by a PTFE insert. For smaller Kvs
values, a Hastelloy insert can be provided in the plug as
well as in the seat (see Table 3).
The possible material combinations and available Kvs
values and curves are shown in Table 3.