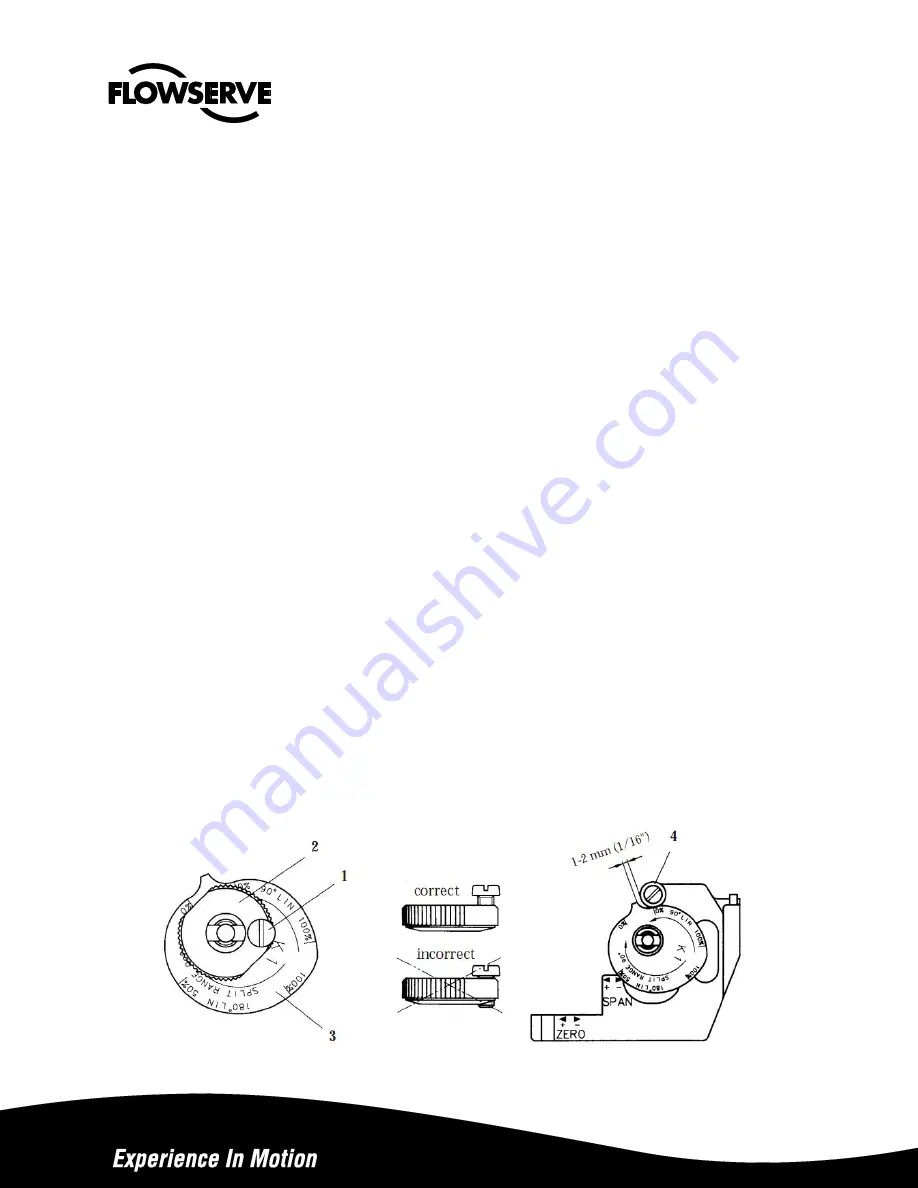
6. Connect supply air to port marked “S”.
7. Connect instrument signal air to the port marked “I” for model 7000 and 7600. For models 7100, 7200, or 7500,
connect 4-20 mA and ground (-). For intrinsically-safe applications (Model 7400 only), see separate intrinsically-safe
I/P IOM for barrier requirements and schematics. The I-P is factory calibrated and cannot be adjusted.
8. Stroke actuator/valve two or three times to align positioner, coupler and actuator. With 50% input (actuator at 45
degrees), tighten all mounting bolts. Stroke actuator/valve again to verify there is no misalignment throughout stroke.
Calibration:
The unit is shipped from the factory pre-calibrated for 90 degree travel (±0.5 degrees rotation – can also be 30/45/60
degrees, see installed cam). For most applications, the valve closed position is much more critical than the valve open
position. Most attention should be made to the valve closed position. Always start calibration procedure by applying
0% input signal, then adjusting zero position.
Caution: Cam pinch points may injure fingers. Be sure to avoid placing fingers and other objects in cam pinch points.
Also avoid touching balance bean and spool while making adjustments as an unpredictable cam rotation may result.
Finally, maintain control of input signal while making adjustments.
After mounting the positioner on the actuator, check cam setting and if needed, perform a cam adjustment:
After mounting the position on the actuator, check cam setting and if needed, perform a cam adjustment:
Cam Adjustment:
1. Remove cove and indicator.
2. Loosen the screw (1) and turn the cam locking nut (2) counter-clockwise until the cam loosens.
3. Adjust the cam (3) as desired making sure that the ball bearing (4) is riding on an active lobe on the cam.
4. To secure the cam, make sure that the screw (1) is backed out form the locking nut (2) then finger tighten the
locking nut and tighten screw (1).
5. Install and adjust the indicator and re-install cover.