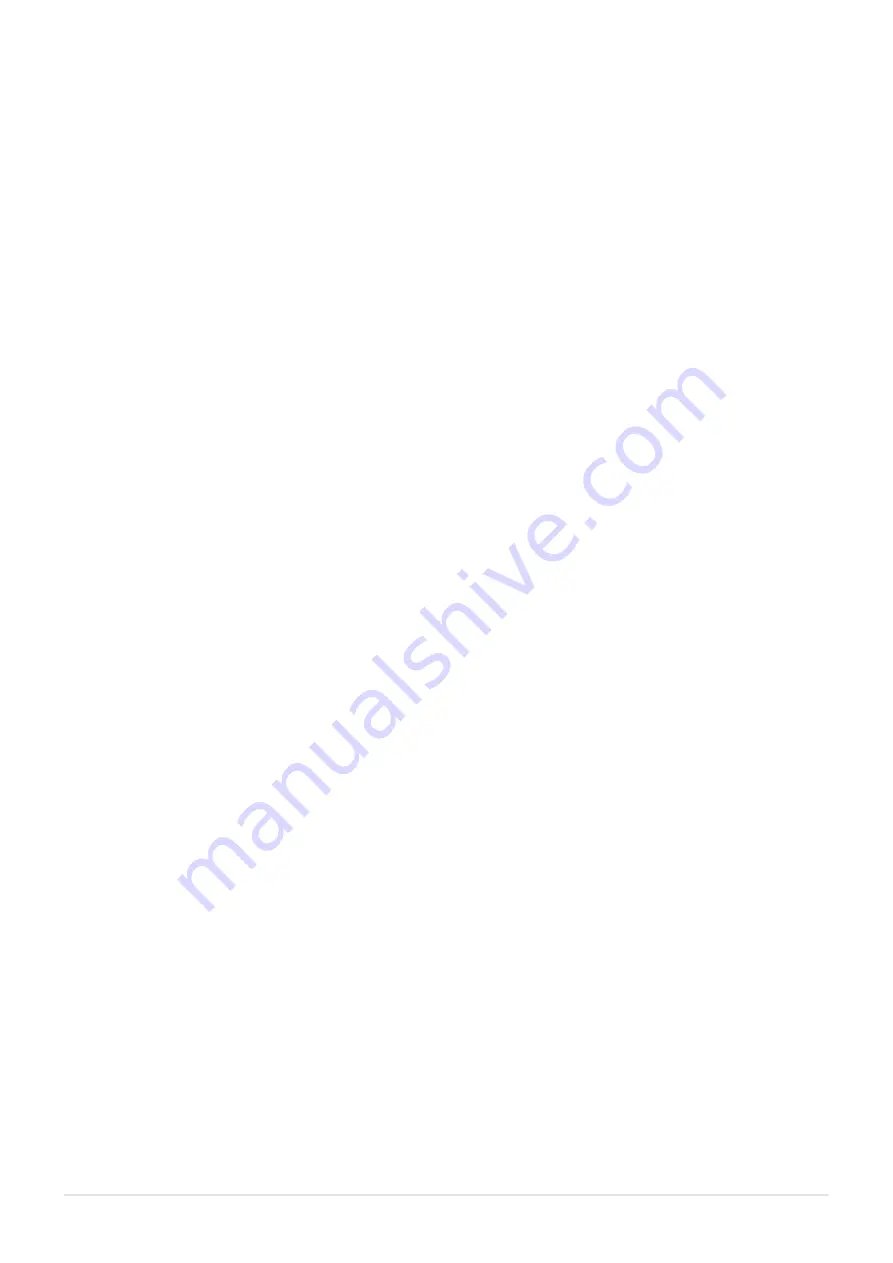
MSB Flintec
26 November 2014
Welding procedure
The following procedure guides the welder through the recommended proceedure for welding brackets and bearing
plates to frame members.
WARNING:
All welding, metal working, and assembly must be performed by a qualified person using proper tools and
safe work habits. When welding, use a procedure that assures a sound, good quality weld. Over welding may cause
distortion and damage; under welding may not develop sufficient strength.
CAUTION:
Take precautions to ensure that the vehicle electrical system is not damaged by the welding. Attach ground
strap directly to vehicle frame member (not load cell body) to which the bearing plates are being welded to prevent
electrical flow through load cell.
Welding Process:
Use a low hydrogen process and AWS E7018 rod or equivalent. The bearing plate may be welded
using SMAW stick, GMAW spray transfer, or FCAW. The user should not use GMAW short circuit transfer.
Weld Configuration: The bracket plates shall be attached using a single or multipass fillet weld sequence
Deposited Weld Metal Fillet Sizes: The finish multipass fillet assembly shall be a minimum of 8 mm (1/3”).
Preheat: The bearing plate and the base metal mounting surface shall be warmed in preparation for welding to
reduce shrinkage stress. Any suitable torch arrangement is satisfactory. Spot heating shall be avoided. The preheat
temperature shall be a MINIMUM of 20°C (68°F) and a MAXIMUM of 65° C (150°F).
Cleaning Before Welding:
Bracket components and bearing plates shall be visually inspected to verify that there is no oil, grease, dirt, paint or other
foreign substance that will reduce the weld quality. Wehere brackets are welded to the body and/or chassis, mounting
surfaces should be prepared using and angle grinder or power wire brush to remove all paint, primer, or other surface
coating. An area the size of the bearing plate plus 25 mm (1") should be cleaned and ground to bare base metal.
In process Cleaning:
Each fillet shall be visually inspected with all slag cover removed, before proceeding with the next bead. A stiff wire
brush or needle scaler may be used for slag removal.
Final Inspection:
Long service life depends on quality application of the fillet welds and THE FINAL SIZE OF THE FILLET. There shall
be no undercut on either the upper leg (on the bearing plate) or the lower leg (frame base metal). Any undercut shall
be repaired with an additional fillet or contoured by grinding to remove the mechanical notch. Visually inspect all weld
stops and starts. Weld craters should be filled. All weld stops shall be staggered. A light coat of primer and paint may
be applied after final inspection. Periodic Inspection: These primary load carrying fillet welds should be inspected
during routine maintenance.
11
WARNING:
HEAT FROM WELDING MAY LOOSEN BOLTS. THEREFORE,
ALL TORQUE VALUES SHOULD BE RECHECKED AFTER
INSTALLATION WHEN ALL WELDS HAVE COOLED.