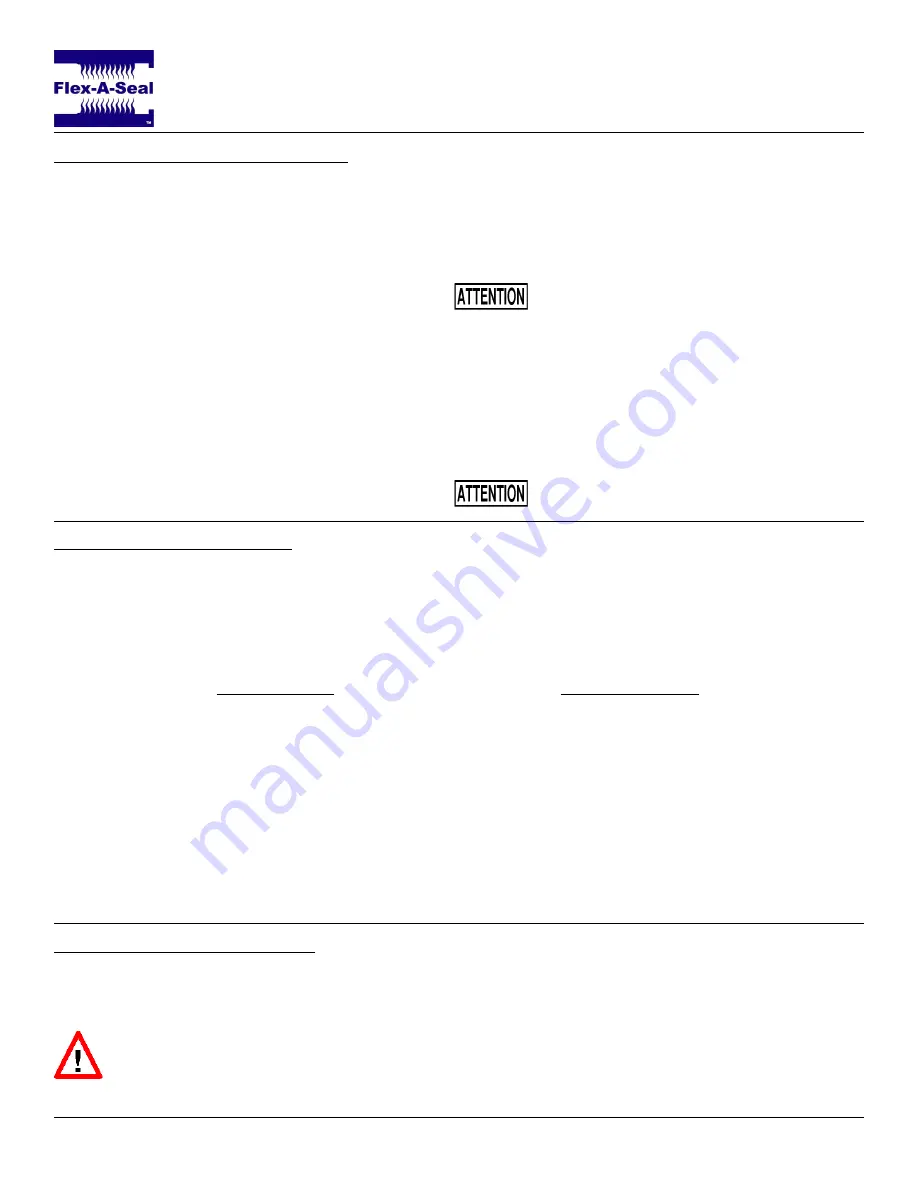
Installation, Operation & Maintenance Guide
Style 58
BEFORE STARTING THE EQUIPMENT
1
. Ensure the pump shaft is properly aligned at
the coupling with the motor.
2
. Check that all gland plate bolts and all screws
are securely fastened.
3
. Once the pump is reassembled, turn the shaft
by hand if possible to check for free rotation, if
not, recheck installation.
4
. Verify that all plumbing and piping plans for the
seal are connected and configured according
to best practice.
5
. Flood the pump, vent all air from the seal
chamber, and check the seal for leakage.
6
. Ensure all plumbing and venting are free of
obstruction and that the chamber is filled with
liquid. Check that all alarms connected to
auxiliary systems are properly functioning to
alert personnel if any issues arise.
Dry-running is a major cause for leakage
and/or failure of mechanical seals. It is
imperative that the seal chamber be
completely vented prior to startup and that
adequate lubrication is supplied to the seal.
7
. Start the pump per the pump manufacturer’s
recommendations, observe for proper
operation, and check for excessive heat at the
seal gland.
Check periodically during operation to
ensure that the seal is not overheating.
OPERATION & MAINTENANCE
If leakage is detected, it should be addressed as soon as possible to prevent hazards and protect personnel.
Leakage could come from a number of leak paths in the seal, or be caused by changes in the pump operation or
condition. Although seals should be inspected regularly for signs of leakage, a properly selected and functioning
mechanical seal will run for extended durations without need for extra attention and should not be disturbed
unnecessarily (i.e. shut down and disassembled without cause). Below is an inexhaustive list of possible causes
of leakage.
Primary Causes
•
Worn seal faces
•
Damaged O-rings
•
Damaged springs
Secondary Causes
•
Change in duty conditions
•
Dry-running
•
Worn bearings
•
Increased vibration
It is important to periodically inspect and maintain flush systems, shaft alignment, and consistent duty
parameters to ensure the seal performs as designed. Often, there is a case of cause & effect with machinery
and processing issues upstream that can cause a seal to leak. Check for the root cause of leakage when
disassembling equipment for inspection or service.
DECOMMISSIONING EQUIPMENT
When decommissioning equipment it is important to ensure that the pump has been fully isolated from the
process and power sources for personnel safety. Pressure and fluid should be fully released before disassembly
of the equipment is to begin.
•
If the equipment has been used with toxic or hazardous fluids, ensure that it is
decontaminated and neutralized before decommission begins. There is often residual fluid
remaining from the draining process so consult the pump OEM for special cases.
Page 5 of 6