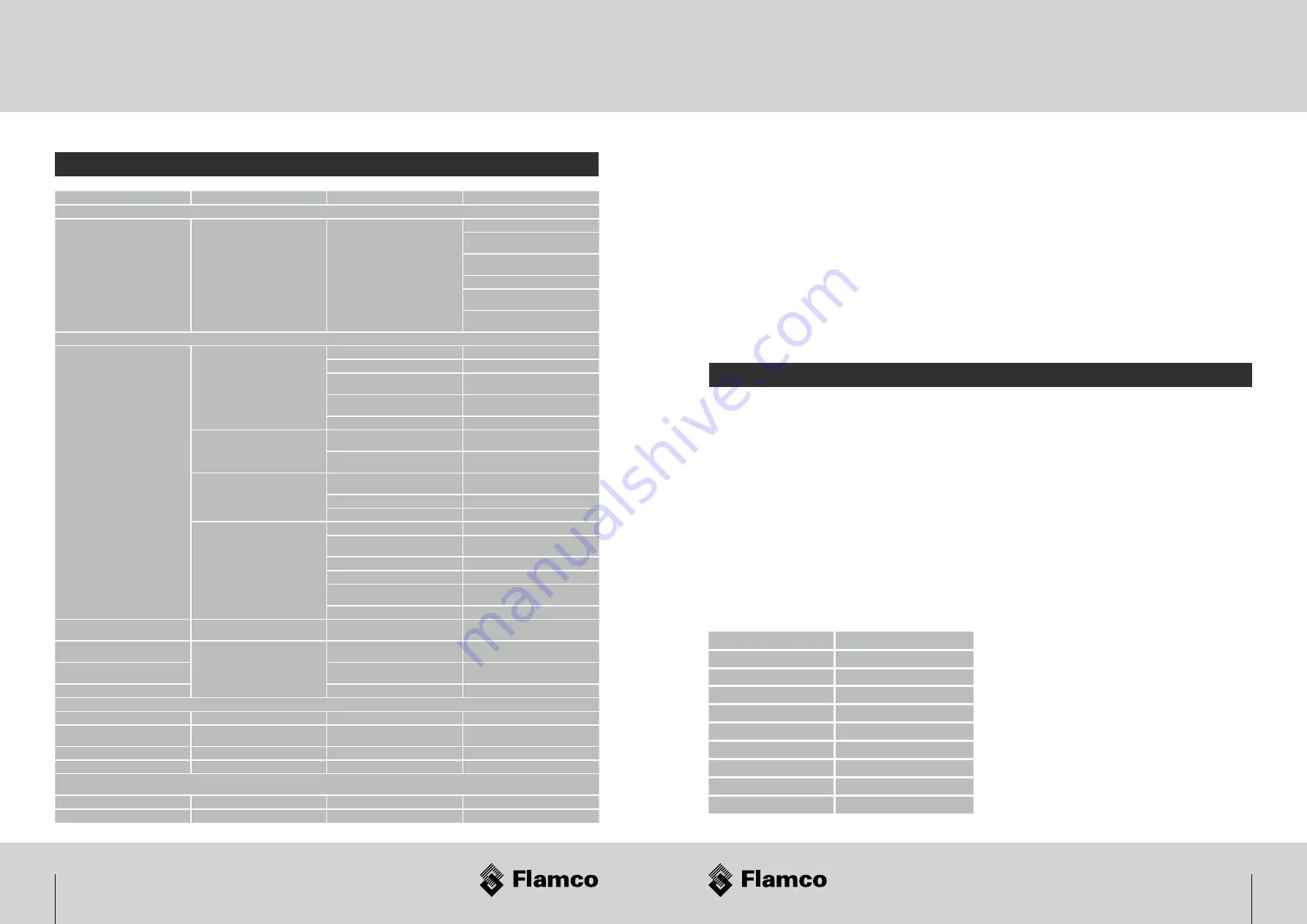
27
26
7.12 Troubleshoot (technician)
7. Service
Complaint
LED indication light
Cause
Solution
No DHW
No DHW
No water pressure
Check/open main water supply valve
# &ޕ*2- ./-$/*-!*-*-- /)+-*+ -
placement
Flow restrictor is clogged or jammed. Replace
ޕ*2- ./-$/*-
'*2. ).*-$.'*"" ѵ +' ޕ*2. ).*-
DHW heat exchanger is clogged. Replace DHW
heat exchanger
Check valve is jammed. Replace check valve
housing including the check valve
DHW not at the right temperature
DHW does not warm up
LED does not light up
HIU is not connected to power source
Connect the HIU to the power supply
No power at power source
Check power source
Power cables not properly connected to
electronic regulator
Connect the power cables to the electronic
regulator
Fuse is broken
Check for any short-circuit problems and
replace fuse (3A)
Failure in electronics
Contact your supplier
- )ޕ.#$)"
Tapping threshold is to low, minimal 1 L/min.
has not been reached
Increase tapping to at least 2 L/min. by opening
the tap further
Flow sensor is not installed correctly
# &ޕ*2. ).*-Ѷ- +' ' *-- +'
ޕ*2. ).*-
ޕ.#$)"
Sensor(s) are not connected or lose contact
Check loom connections and connect the
sensors properly, then restart electronics
Sensor(s) defect
Replace broken sensor and restart electronics
Possible defect electronic cables or electronics
Contact your supplier
Supply and return valves are closed
Open supply and return valves
Pressure or temperature of the DH system are
)*/$)*-) 2$/#.+ $ޔ/$*).
Check temperature and pressure of the DH
system
Filter is clogged
# &)' )ޔ'/ -
DHW heat exchanger is clogged
Replace DHW heat exchanger
Cables of the control valves are mixed up
Connect cables properly. Green connector must
be connected to the DHW control valve
Possible defect in control valve
Replace control valve
Option: DHW circulation circuit does not
warm up
LED does not light up
Fuse is broken
Check for any short-circuit problems and
replace fuse (3A)
Power supply cable of the optional DHW
circulation pump unit is not connected
Connect the power supply cable of the optional
DHW circulation pump unit
Optional DHW circulation pump unit is broken
or jammed
Replace DHW circulation pump unit
Failure in electronics
Contact your supplier
Casing will not close properly
Casing does not close properly
Cables are caught in between unit and casing
Keep cables free of any obstructions
Metal bracket holding the heat meter is not
ޔ// *-- /'4
%0./ҝޔ/-& /)/-4"$)
Heat meter is obstructing the casings path
Connect the heat meter properly
Electronics are not properly placed
Check mounting of electronics
Other defects
It is normal for the HIU to generate a light noise during tapping or heating operation. The regulator valves can also make a light humming sound
Rattling sound
*-"- )ޕ.#$)"
Flow sensor not installed correctly
)./''ޕ*2. ).*-+-*+ -'4
Other defects
Contact your supplier
Guidelines for System Conditioning of Heating and Cooling Networks for Flamco Limited - LogoEco Heat Interface
Units (HIU)
Flamco Limited prides itself on bringing to the UK market a proven range of Heating and Cooling Interface Units. To ensure
/#/*0-+-*0/. '$1 -$)- . '*)" 1$/4)+ -!*-() Ѷ/# . "0$ '$) .- .+ $ޔ''42-$// )/*$) ).0-
both the primary and secondary side of the heat network are designed, installed and commissioned to realise the desired
heating comfort levels.
# . "0$ '$) .- )*/*Ȃ - !*-0. *)+*/' Ѷ*( ./$Ѷ)2/ --2*Ȃ.$ *!
/# .4./ (ѵ*' '4!*-/# # /$)")**'$)"$-0$/.ѵ*-!0-/# -"0$) *)2/ -/- /( )/)2/ -
)'4.$.+' . - ! -/*сшҝспрсѶфпҝспрт)чффсѵ
#$'./)*/ 3#0./$1 Ѷ2 *Ȃ -/# . "0$ '$) .
from experience and a practical standpoint, in addition, as a check list to support design review. These guidelines are not
$)/ ) .()/*-4*-ޔ3 $)/# $-++-*#Ѹ(*- *1 -/# 4- $)/ ) ..0++*-/$)"*0( )//$*)/*#$"#'$"#/
good practise and methodology ensuring operation and maintenance activities are kept to a minimum post handover. We
are not specialists in the design, installation and or cleaning and subsequent treatment of water systems but, nevertheless,
contained in the sections below are importance aspects to consider.
8.1 System Design Considerations
• A review of the system should be undertaken post the design stage. The review should focus on the installation,
'*/$*))+$/4*!./-$) -.*/#ޔ3 )/ (+*--4Ѷ$-)".- (*1' 1$ .Ѷ -$./-+.Ѷ$.*'/$*)
valves to ensure that removal of debris from the system which was not removed in the commissioning activity is
managed and that sub sections can be economically isolated to permit maintenance.
• It should be considered at the design stage to include into the design a means ferrite removal. Poorly commissioned
and maintained systems exhibit corrosion. As the majority of systems contain products manufactured from iron, it is
the iron in the form of steel ferrite which creates the tell tale black sludge or blacked water which indicates corrosion
is taking place of components of the system. This corrosion if remaining unchecked, fouls water ways and controls,
erodes system components, reduces system performance and leads to the production of hydrogen in the system
known as “Gassing”. This is also a tell tale sign of system corrosion.
•
.*1 -шпڿ*! -$.$).4./ (.$.! --*0.2 - *(( )/# $)./''/$*)*!-- -/#Ѷ(") /$ޔ'/ -/**/#
remove the ferrite but act as a means of identifying corrosion is taking place and a prompt for remedial action.
•
# - (*1' 1$ $ ''4Ѷ.#*0'#1 ޔ-./+..-/ *!цфڿ -$.- (*1'*-"- / -Ѷ#1 $)*-+*-/ $)/*
$/.//$($3$)"!0)/$*)/**+ )/# .4./ (ޕ0$/*+ -($/-+$- (*1'*!/# -$.Ѷ(*0)/ $)/# *((*)
- /0-)Ѷ($)- /0-)+$+ 2*-&ѵ# ޔ'/ -.#'' *! ,0/ .$5 )+$/4/*''*2.0Ȃ$$ )/ޕ*2-/ )
-$.+/0- !*-/# .4./ (.$5 җ'$) .$5 $.- *(( ) Ҙѵ)4.0#ޔ'/ -.#*0'#1 /# !*''*2$)"(") /$
ޔ './- )"/#+$/4.($)$(0(/* ).0- (3$(0(! --$/ - (*1'ѵ
8. Appendix A
# ޔ'/ -.#*0' /*/# - ,0$- ( )/.*!/#
“Operating and Maintenance” instructions handed over with
/# .4./ (ѵ!)1$.*-4./$& -$.+-*1$ 2$/#/# ޔ'/ -$/
should be attached at a suitable location as to indicate the
+- . ) 2$/#$)/# .4./ (*!/# ޔ'/ -/* ).0- + -$*$
checking & servicing by any attending Service Engineer.
2*0''.*- *(( )/#//# . ޔ'/ -.$)*-+*-/
sight glass, particularly on the larger sizes to provide a visual
means of assessing corrosion without the need to disrupt
the operation of the system for checking.
Line Size
Magnetic Field Strength
DN15
7500 gauss
DN20
9000 gauss
DN25
10500 gauss
DN35
21000 gauss
DN40
21000 gauss
DN50
52500 gauss
DN80
73500 gauss
DN100
73500 gauss
DN150
94500 gauss