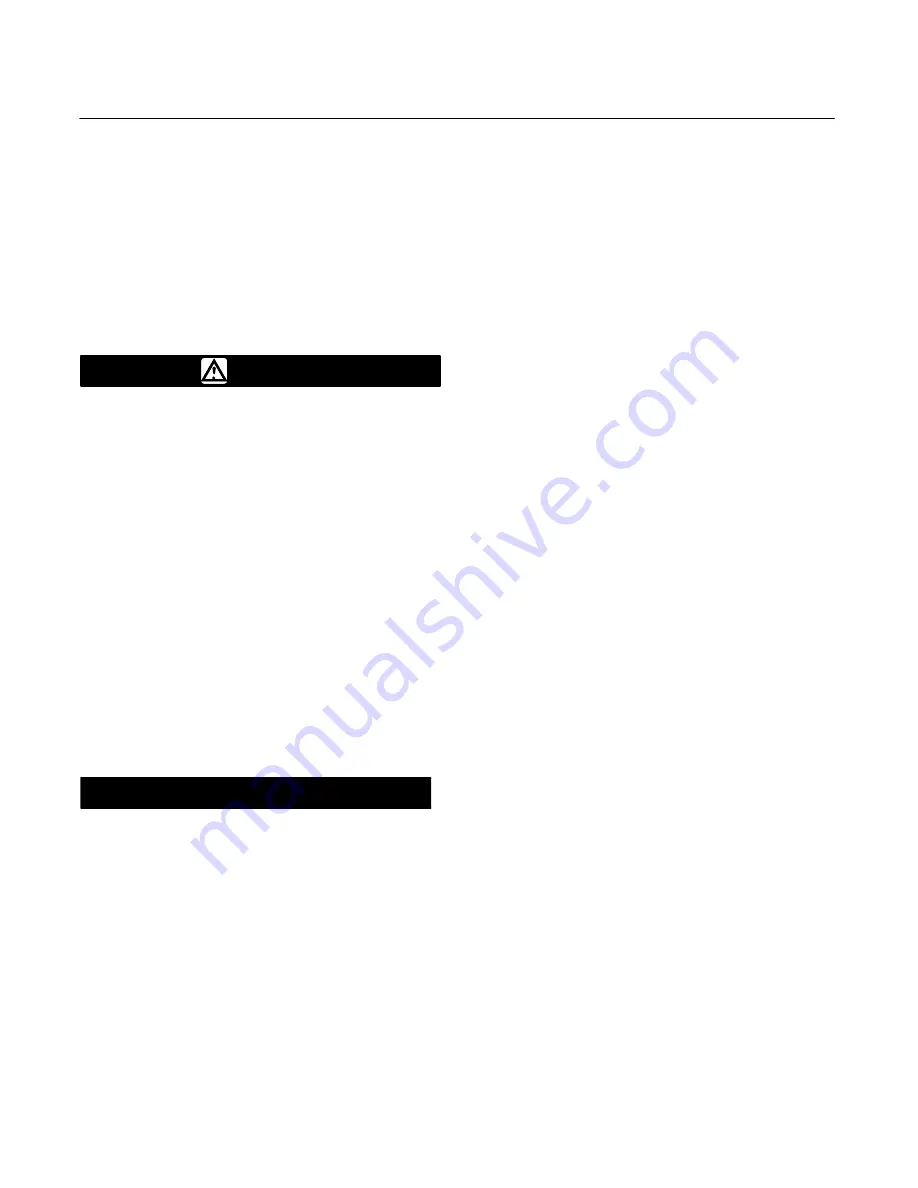
ET Valve
Instruction Manual
Form 5081
June 2002
3
Specifications
Typical specifications for these valves are shown in
table 1.
Installation
WARNING
Always wear protective gloves,
clothing, and eyewear when
performing any installation operations
to avoid personal injury.
Personal injury or equipment damage
caused by sudden release of pressure
may result if the valve assembly is
installed where service conditions
could exceed the limits given in table 1
or on the appropriate nameplates. To
avoid such injury or damage, provide a
relief valve for over-pressure
protection as required by government
or accepted industry codes and good
engineering practices.
Check with your process or safety
engineer for any additional measures
that must be taken to protect against
process media.
CAUTION
When ordered, the valve configuration
and construction materials were
selected to meet particular pressure,
temperature, pressure drop, and
controlled fluid conditions.
Responsibility for the safety of
process media and compatibility of
valve materials with process media
rests solely with the purchaser and
end-user. Since some valve body/trim
material combinations are limited in
their pressure drop and temperature
ranges, do not apply any other
conditions to the valve without first
contacting your Fisher sales office.
Fisher does not assume final
responsibility for the selection, use, or
maintenance of any product. Final
responsibility for the selection, use,
and maintenance of any Fisher
product remains with the purchaser
and end-user.
1. Before installing the valve, inspect the valve and
associated equipment for any damage and any
foreign material.
2. Make certain the valve body interior is clean, that
pipelines are free of foreign material, and that the
valve is oriented so that pipeline flow is in the same
direction as the arrow on the side of the valve.
3. The control valve assembly may be installed in
any orientation unless limited by seismic criteria.
However, the normal method is with the actuator
vertical above the valve. Other positions may result
in uneven valve plug and cage wear, and improper
operation. With some valves, the actuator may also
need to be supported when it is not vertical. For
more information, consult your Fisher sales office.
4. Use accepted piping and welding practices when
installing the valve in the line. For flanged valves,
use a suitable gasket between the valve and pipeline
flanges.
Note
Depending on valve body materials
used, post weld heat treating may be
required. If so, damage to internal
elastomeric and plastic parts, as well
as internal metal parts is possible.
Shrink-fit pieces and threaded
connections may also loosen. In
general, if post weld heat treating is to
be performed, all trim parts should be
removed. Contact your Fisher sales
office for additional information.
5. With a leak-off bonnet construction, remove the
pipe plugs (keys 14 and 16, figure 14) to hook up the
leak-off piping. If continuous operation is required
during inspection or maintenance, install a
three-valve bypass around the control valve
assembly.
6. If the actuator and valve are shipped separately,
refer to the actuator mounting procedure in the
appropriate actuator instruction manual.