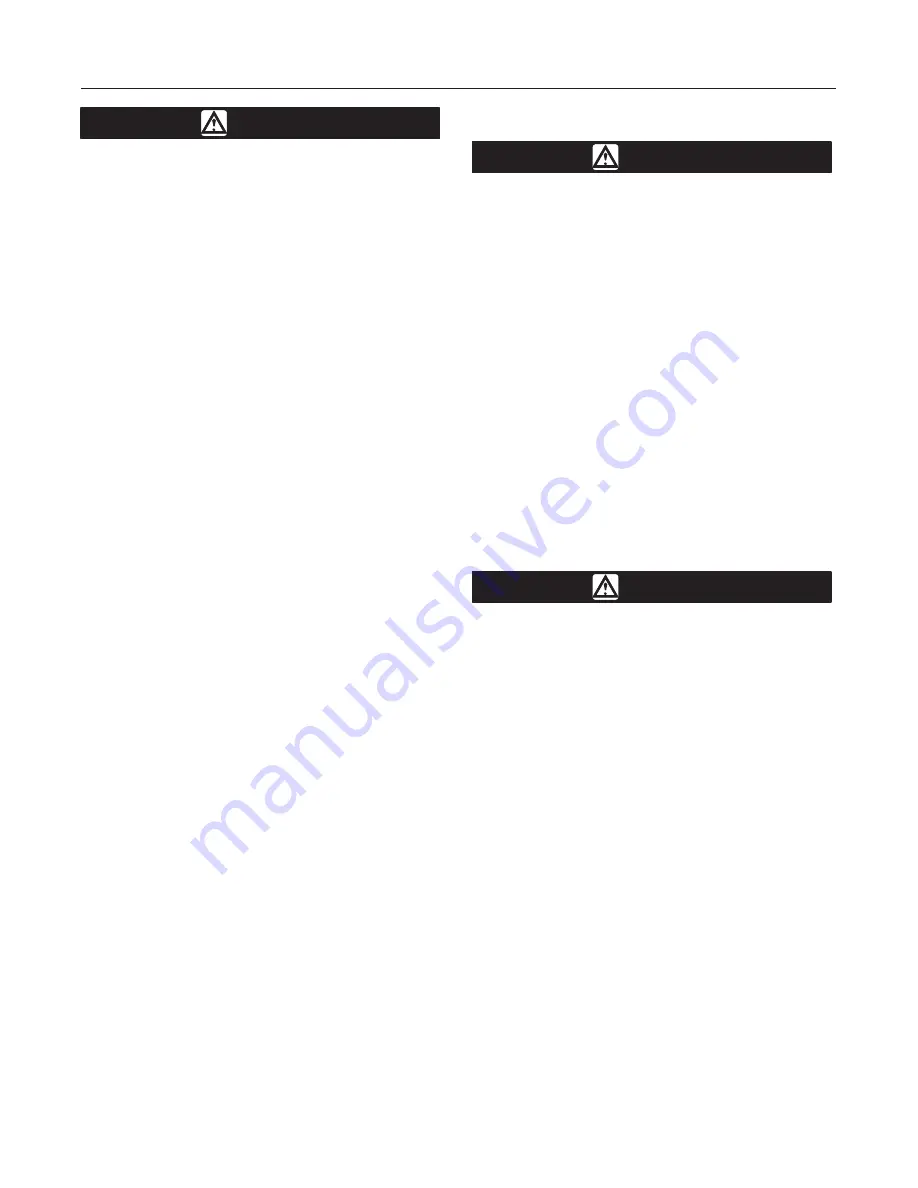
Model A31A
8
CAUTION
To avoid damage to the valve disk dur-
ing installation, the valve must be in the
fully closed position. If the Model A31A
valve is equipped with a fail-open actua-
tor, remove the actuator before instal-
ling the valve/actuator assembly or
cycle the valve into the fully closed
position. Then, take appropriate steps to
be sure that the actuator does not cause
the valve to open during installation.
1. See figure 4 for recommended valve orientation.
D
For Wafer-Style Valves: Install the lower flange
bolts first to form a cradle for the valve (see figure 4).
See table 5 for flange bolt specifications.
D
For Single-Flange Valves: Position the valve
between the flanges. Be sure to leave enough room
for the flange gaskets. Install the lower flange bolts.
2. For all Valves: Select the appropriate gaskets for
the application. Flat sheet, spiral wound, or other gas-
ket types, made to the ANSI B16.5 standard or user’s
standard, can be used on Model A31A valves depend-
ing on the service conditions of the application.
3. For Wafer-Style Valves: Properly orient the valve
according to the specific application. Place the valve in
the line so the flow properly enters the valve as indi-
cated by the flow tag. Then, install the valve and the
gaskets between the flanges into the cradle formed by
the flange bolts.
4. Install the remaining flange bolts.
D
For Wafer-Style Valves: Make sure the gaskets
are centered on the gasket sealing surfaces of the
flange and body.
5. For all Valves:Tighten the flange bolts in an alter-
nating criss-cross fashion to a torque value of one-
fourth of the final bolting torque. Repeat this procedure
several times, increasing the torque value each time
by a fourth of the final desired torque. After applying
the final torque value, tighten each flange bolt again to
allow for gasket compression.
Packing Adjustment and Shaft Bonding
WARNING
Personal injury could result from pack-
ing leakage. Valve packing was tight-
ened before shipment; however, the
packing might require some readjust-
ment to meet specific service condi-
tions.
1. For PTFE or graphite packing: Tighten standard
packing follower nuts only enough to prevent shaft
leakage. Excessive tightening of packing will acceler-
ate wear and could produce higher rotating friction
loads on the valve stem. If necessary, refer to the
Packing Maintenance section.
2. For ENVIRO-SEAL Packing Systems: will not
require this initial re-adjustment. Refer to the separate
ENVIRO-SEAL Packing System–Rotary Valves In-
struction Manual, Form 5305 for repair and adjustment
procedures.
3. For hazardous atmosphere or oxygen service
valves, read the following Warning, and provide the
bonding strap assembly mentioned below if the valve
is used in an explosive atmosphere.
WARNING
The valve drive shaft is not necessarily
grounded to the pipeline when installed.
Personal injury or property damage
could result, if the process fluid or the
atmosphere around the valve is flam-
mable, from an explosion caused by a
discharge of static electricity from the
valve components. If the valve is
installed in a hazardous area, electrical-
ly bond the drive shaft to the valve.
Note
The packing is composed of all conduc-
tive packing rings (graphite ribbon
packing) to electrically bond the shaft to
the valve for hazardous area service or
non-conductive PTFE packing rings. For
oxygen service applications, provide al-
ternate shaft-to-valve body bonding ac-
cording to the following step.
4. Attach the bonding strap assembly (key 131, figure
6) to the shaft with the clamp (key 130, figure 6).
5. Connect the other end of the bonding strap assem-
bly to the valve flange cap screws.
6. For more information, refer to the
Packing Mainte-
nance section below.