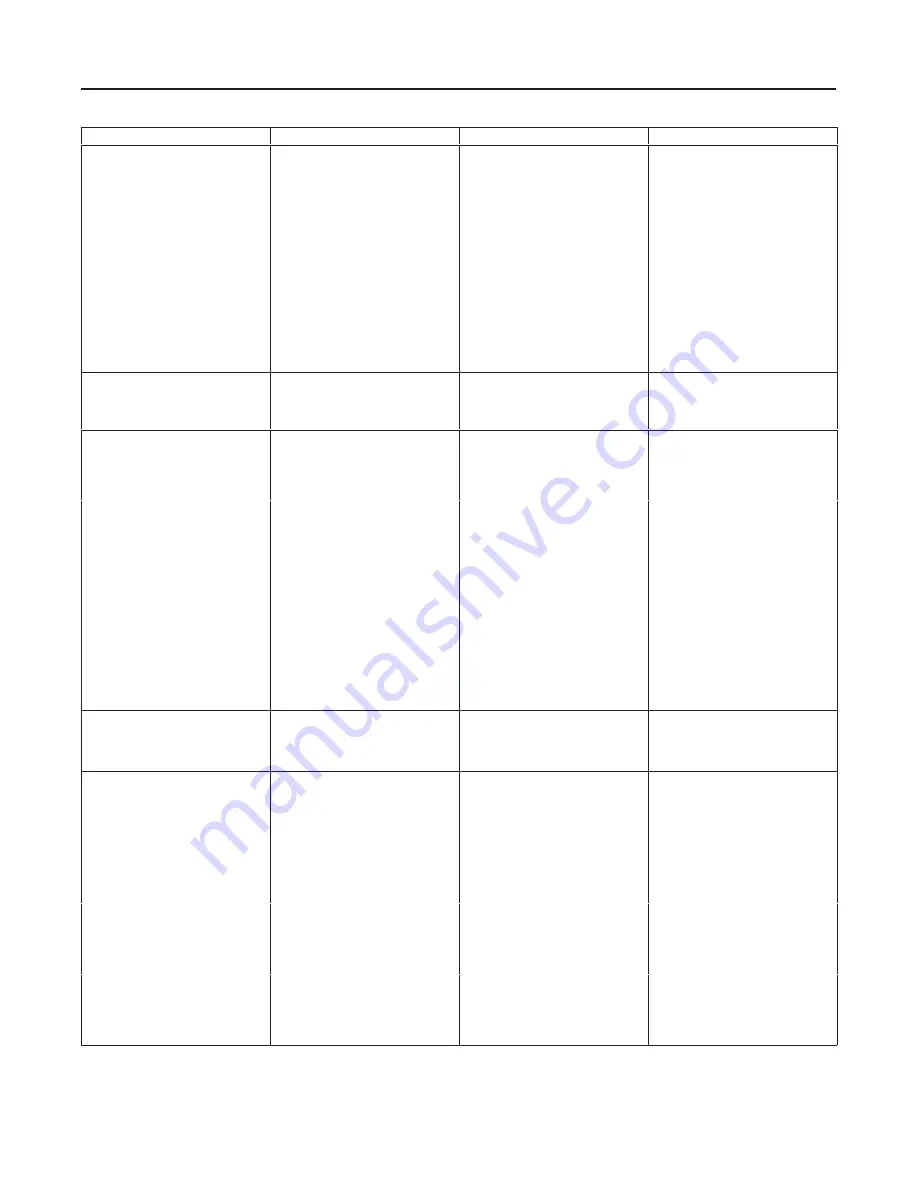
4194A, B, and C Series
5–3
Table 5-1. Troubleshooting Chart (Continued)
Fault
Possible Cause
Check
Correction
2. Controlling off set point as
reflected by process and set point
indicators.
2.7 Reset valve leaks.
2.7 Adjust output to 15 psig (1.0
bar) for a 3 to 15 psig (0.2 to 1.0
bar) output or 30 psig (2.0 bar) for a
6 to 30 psig (0.4 to 2.0 bar) output.
Close the reset valve. If the
controller output varies and no
leaks were found in the rest of the
feedback system (Step 2.6), the
reset valve is leaking.
2.7 Replace the reset valve.
2.8 Leak in the remote set point
system (suffix letter M only).
2.8 Adjust remote set point
pressure to 15 psig (1.0 bar). Using
soap solution, check for leaks in
the remote set point element and
tubing assembly.
2.8 Repair or replace parts as
necessary.
2.9 Input element over pressured.
2.9 Check for zero shift.
2.9 Replace input element and
adjust travel stops.
3. Controlling off set point but not
reflected by process and set point
indicators.
3.1 Out of calibration
3.1 Refer to the process indicator,
remote set point (if applicable), and
flapper alignment procedures in
section 3 or 4.
3.1 Adjust as necessary
4. No reset action (4194B and
4194C Series)
4.1 Reset valve is plugged
4.1 Turn the reset valve through its
range several times to remove any
restrictions.
4.1 If reset action returns, no
further action is necessary. If not,
replace the reset valve (4194B
Series) or the rate/reset valve
(4194C Series).
4.2 Reset pressure leak
4.2 Adjust the output to 15 psig (1.0
bar) for a 3 to 15 psig (0.2 to 1.0
bar) output or 30 psig (2.0 bar) for a
6 to 30 psig (0.4 to 2.0 bar) output.
Close the reset valve. If the output
varies and no leaks were found in
the rest of the feedback system
(see Step 2.6), the reset valve is
leaking.
4.2 Replace the reset valve (4194B
Series) or the rate/reset valve
(4194C Series)
4.3 Tubing leak
4.3 With reset valve positioned at
0.01 minutes/repeat, put 15 psig
(1.0 bar) to the output port. Using
soap solution, check for leaks in
the reset bellows and attached
tubing assembly.
4.3 Repair or replace parts as
necessary.
5. Abnormal control point shift
when proportional band is changed.
5.1 Flapper is dirty or pitted
5.1 Inspect the flapper.
5.1 Clean, or replace flapper as
necessary.
5.2 Flapper is out of alignment
5.2 Refer to flapper alignment
procedures in section 3 or 4.
5.2 Align flapper as necessary.
6. Controller will not attain full
output range.
6.1 Output pressure gauge not
functioning
6.1 Measure the output with an
external pressure gauge.
6.1 Replace the gauge if it is
defective.
6.2 Supply pressure not correct
6.2 Check with an external source.
6.2 Repair or replace the supply
pressure regulator, if necessary.
Replace the supply pressure gauge
if necessary.
6.3 Proportional band setting two
wide (4194A Series only)
6.3 Adjust proportional band setting
to 10. Manually cap the nozzle.
Output should increase.
6.3 Use a narrower proportional
band setting (decrease the
proportional band setting).
6.4 Input element or linkage failure
6.4 Inspect the element for
alignment, loose screws and
damaged flexures, links or pivots.
Using soap solution, check the
sensing element for leaks.
6.4 Repair or replace parts as
necessary.
6.5 Leak in nozzle pressure tubing
6.5 Using soap solution, check for
leaks in the nozzle tubing
assembly.
6.5 Replace faulty parts as
necessary. Clean out the relay
primary orifice with the cleanout
wire attached to the relay to ensure
the orifice is not clogged.
–Continued–
Содержание 4194A Series
Страница 6: ...4194A B and C Series 1 6...
Страница 32: ...4194A B and C Series 4 14...
Страница 69: ...4194A B and C Series 5 37 Figure 5 22 Process and Set Point Indicator Assembly 36A6985 C DOC...
Страница 70: ...4194A B and C Series 5 38 Figure5 23 Capsular Element Assembly 58A0706 C DOC...
Страница 72: ...4194A B and C Series 5 40 Figure 5 26 Remote Set Point Assembly Drawing j APPLY LUB SEALANT 36A6988 C DOC...
Страница 74: ...4194A B and C Series 5 42 Figure 5 28 Internal and External Set Point Option 56A9752 S DOC j APPLY LUB ADHESIVE...