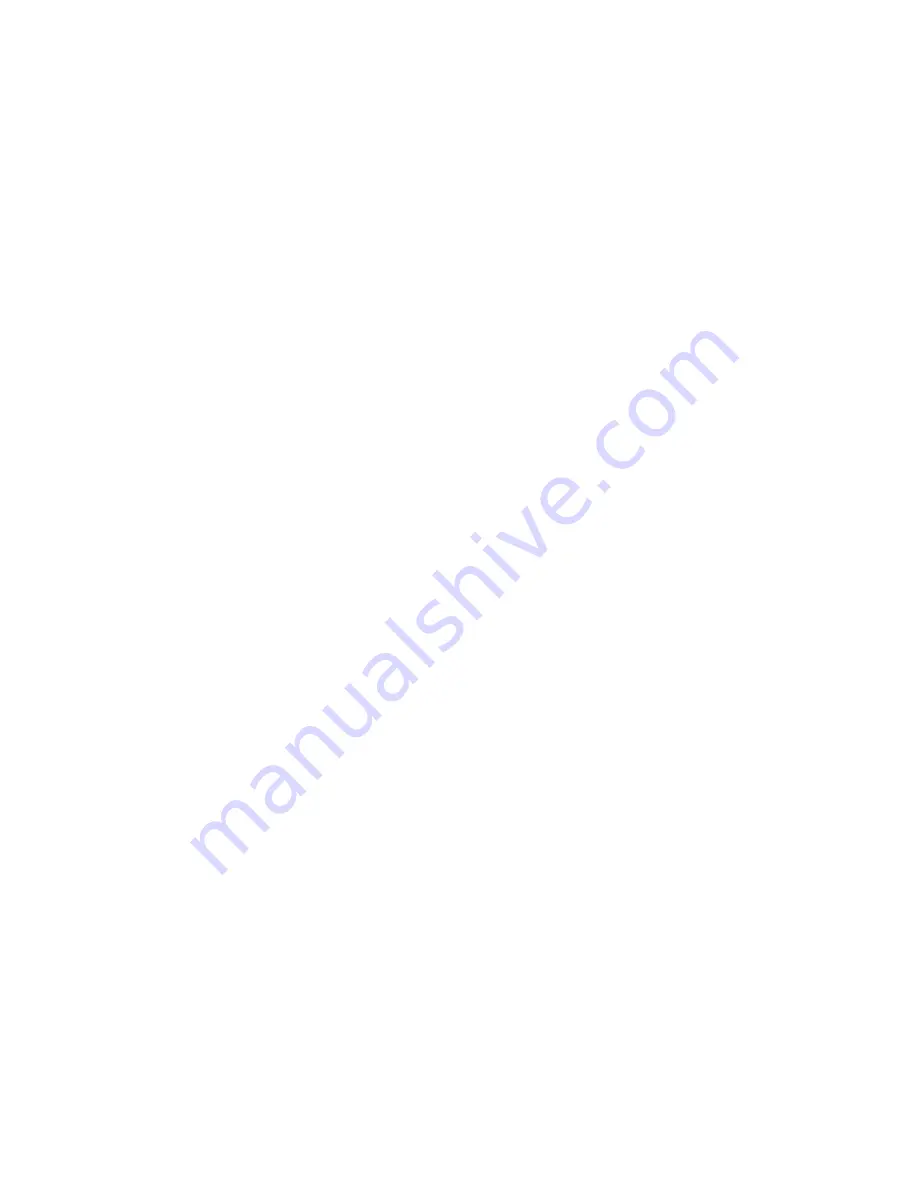
38
7.12 Replacement Of Low Ambient Heater - “B”
Model
This element is mounted in the floor of the divider and is not replaceable. If it should be found to be open
circuit, a replacement low ambient heater can be fitted to the return air grill.
7.13 Replacement Of Low Ambient Heater - “B”
Model (In Return Air Grill)
This element is mounted in the return grill of the divider. It is of the blanket wire type on an aluminium tape
stuck to the grill itself.
1. Unplug the refrigerator from the power supply.
2. Remove all the PC shelving and crisper bins.
3. Remove the PC duct cover.
4. Remove the PC air return grill and unplug the element from the harness.
5. Peel off the old element and replace with the new.
6. Refit in reverse order.
7.14 Evaporator
Replacement
The evaporator is located in the FC compartment mounted on the back wall on its own carrier, with a grill
covering a fan motor which is housed in the front cover.
Having determined that the evaporator needs replacing:
1. Unplug the refrigerator from the power supply
.
2. Recover the refrigerant.
3. Remove the FC door.
4. Remove the evaporator coil cover.
5. Clean both suction and capillary pipes with emery cloth.
6. With the tube cutter, cut the suction pipe as close as possible to the induction brazed joint (cutting the
suction capillary side of the joint).
7. With a file or knife cut the capillary where it enters the transition joint on the evaporator.
8. With the element wiring disconnected, the evaporator can be removed.
9. Take the replacement evaporator and fit it to the carrier, fitting the defrost element assembly and the 2
heat shrink sleeving onto the pipes.
10.Align the evaporator and joints ready to be soldered into position.
11.Lay the product on its back.
12.Place a protective covering over the back of the liner to protect it should solder drop onto it while the
joint connections are being made.
13.Having fitted the suction and capillary lines together with a protective heat shrink sleeving placed on
the pipe first away from the heated area, heat the “J” type soldering iron to temperature with the oxy-
acetylene or LPG. This should be cleaned and tinned prior to the soldering operation.
14.Hook the iron over the joint area and allow the pipework to heat while applying the solder. Once the
joint appears to have a full puddle of solder around the joint area, remove the iron and allow the joint
to cool.
15.The same applies for the capillary, applying more heat to the transition joint as it is heavier in material
than the capillary.
16.Pressure test both joints.
17.Fit heat shrink sleeving over the joint and heat, having placed damp rags around the area of the ABS
liner as heating the heat shrink can cause the liner to be overheated. It is also important to keep the
thermal fuse in the element circuit away from the heat gun, as heat from the heat gun can cause the
thermal fuse to go open circuit.
Note: The solder used to solder these FC joints is a special solder containing 5% antimony and 95% tin and
is supplied with the evaporator kit. Also, the solder contains a special flux as a resin core in itself. No other
type of solder should ever be used.
Содержание 790 Active Smart
Страница 1: ...790 ACTIVE SMART REFRIGERATOR FREEZER 517800...
Страница 2: ...2...
Страница 42: ...42 8 WIRING DIAGRAM...