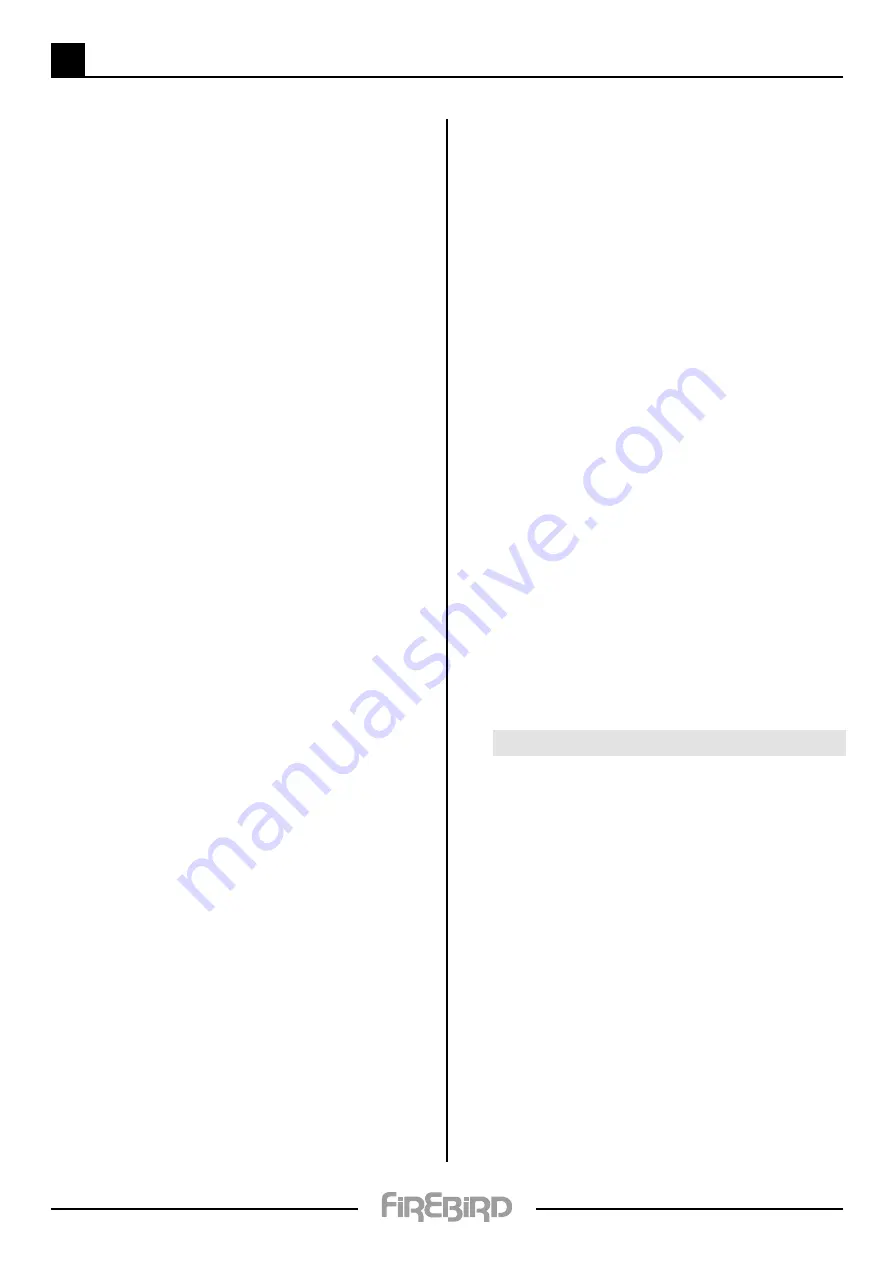
6
servICIng
tHe Burner
Check Diesel nozzle size and replace (see burner section
for details).
ensure correct specification replacement nozzle is
used.
1. Check all diesel filters and replace as necessary.
2. Remove burner and clean blast tube and ensure
that airways are clear.
3. ensure electrodes are clean, dry, not broken and are
set as per burner specifications.
4. Clean fan and photocell.
5. once again check flexible diesel lines and
connections for damage or leaks, replace as
necessary. replace flexible diesel lines every 2
years.
Combustion Check
1. Carry out a combustion analysis.
2. Follow the steps as set out in the burner set-up
section.
3. Check safety operation, pull out the photo cell,
cover and make sure the burner locks out.
4. Check the thermostat operation.
5. allow the boiler to operate for at least two full “on/
off” cycles.
ensure service record is completed.
annual servicing must be carried out by a competent,
qualified engineer, preferably familiar with Firebird
products.
Do not commence service until both the electrical and
diesel supply to the boiler have been safely isolated.
tHe dIesel tank
Check for diesel leaks. Draw off any accumulated water
and sludge from the tank by opening the drain valve.
Turn off the diesel supply and remove the filter bowl,
then wash the element clean with diesel. Fit a new
element if required.
tHe BoIler
Remove combustion access door for access to baffles
and to clean heat exchanger.
Cleaning a Firebird condensing boiler:
1. Remove all baffles, including the tubular baffles in
the condensing section and clean them.
2. Remove the condense trap and clean it, place a tray
under the connection for the trap. Vacuum out any
lose debris from the chamber.
3. Clean the inside of the boiler with a vacuum cleaner.
4. Refit all the baffles and the condensate trap
securely.
5. System pressure should not exceed 2 bar at full
operating temperature. The expansion vessel
should be checked during the annual service to
ensure that it is operating correctly.
Check insulation sealing and the silver foil lining in
combustion access door - replace if necessary. Check
graphite seal and replace if necessary. When refitting
this door be careful not to damage the foil and
insulation by over tightening.
Check that the condensate trap is secure in position,
clean and free of combustion debris. ensure that the
condensate drain is free and not blocked.
expansion vessel pre
-charge pressure should be
checked annually.
23