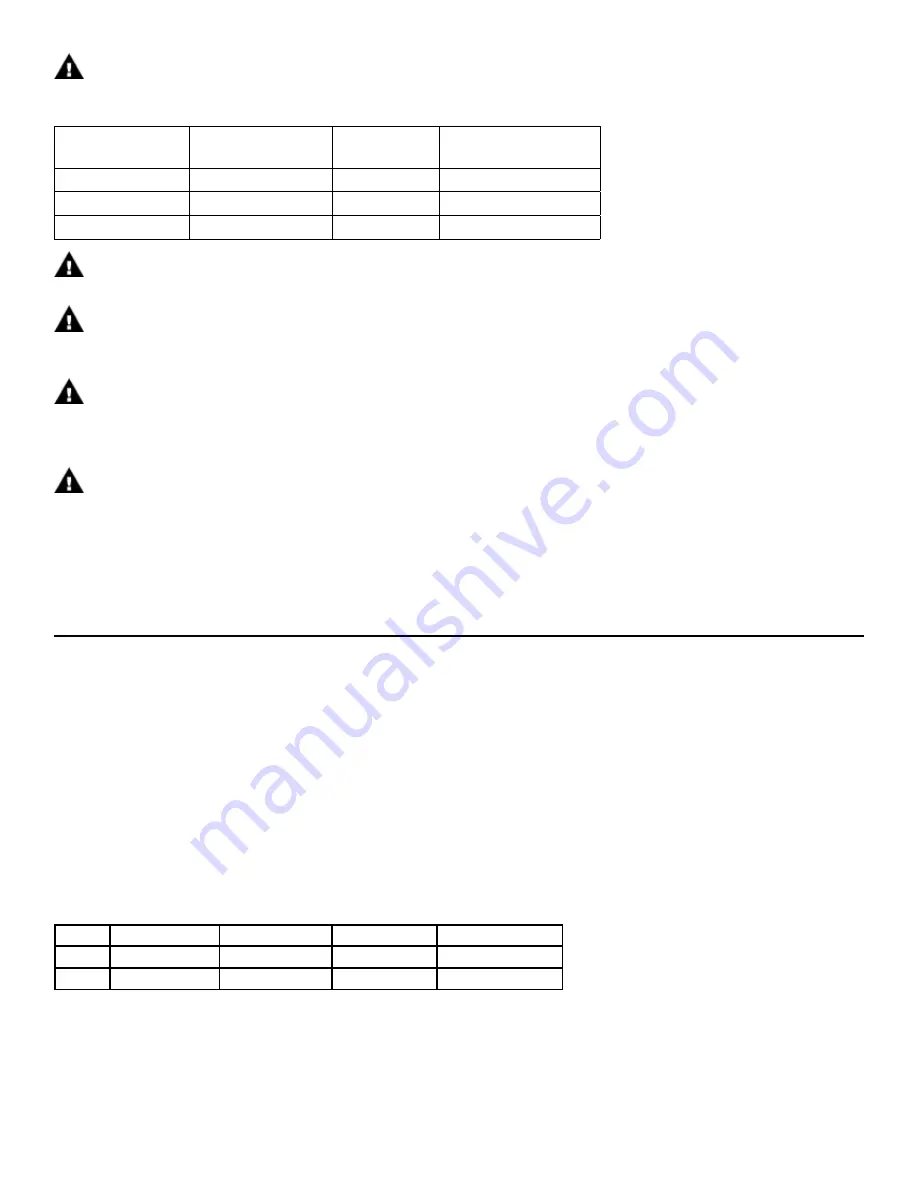
7
DB11/15 Capabilities
Maximum Working Pressure:
90 psi (6.2 bar) (models with o-ring)
Maximum Viscosity:
150 cP
Maximum Temperature:
Polypropylene -180º F (82º C); PVDF – 220º F (104º C)
Note: Maximum temperature is application dependent.
Consult a chemical resistance guide or the chemical manu-
facturer for chemical compatibility and temperature limits.
Maximum Noise Level:
78 dBA (pump only)
Solids: Maximum particle size is 100 microns for slurries and 1/64” (.4 mm) for infrequent particles. Maximum hardness is 80 HS. Maximum concentration
is 10% by weight. If solids are being pumped, it is recommended that the pump have either ceramic or for best results, silicon carbide components. Pumping
solids may lead to increased wear.
Minimum Allowable Flow Rate:
Do not allow the flow rate to drop below the minimum flow rate listed in the chart below:
Model
3450 rpm
1725 rpm
2900 rpm
1450 rpm
DB11
4 gpm (.9 m
3
/hr)
2 gpm (.5 m
3
/hr)
.76 m
3
/hr (3.4 gpm)
.38 m
3/
hr (1.7 gpm)
DB15
5 gpm (1.1 m
3
/hr)
2.5 gpm (.6 m
3
/hr)
.95 m
3
/hr (4.2 gpm)
.48 m
3
/hr (2 gpm)
Maximum Allowable Motor Power:
Do not exceed the maximum power rating for the pump coupling.
Standard coupling for the DB11 is 6-pole; standard coupling for the DB15 is 8-pole.
6-pole coupling
=
2 horsepower (1.5 kW)
8-pole coupling
=
3 horsepower (2.2 kW)
10-pole coupling
=
5 horsepower (4 kW)
Temperature Classification
The surface temperature of the DB Series pumps depends upon the temperature of the fluid that is being pumped. The following chart lists
different fluid temperatures and the corresponding pump surface temperature.
Cleaning
The pump must be cleaned on a regular basis to avoid dust build up greater than 5 mm.
Motor Rotation Test
Pump must be full of liquid with no trapped air in the suction and discharge lines before the rotation of the motor is checked. Do not operate
pump until it is full of liquid.
Start up
The pump must be filled from a flooded suction tank (gravity) or primed with liquid from an outside source. Open the inlet (suction) and dis-
charge valves completely and allow the pump to fill with liquid. Close the discharge valve. Turn the pump on and slowly open the discharge
valve. Adjust the flow rate and pressure by regulating the discharge valve. Do not attempt to adjust the flow with the suction valve.
Maintenance
The recommended maintenance schedule depends upon the nature of the fluid being pumped and the specific application. If the pump is
used on a clean fluid, it is recommended that the pump be removed from service and examined after six months of operation or after 2,000
hours of operation. If the pump is used on fluids with solids, high temperatures or other items that could cause accelerated wear, then this
initial examination should be sooner.
After the initial examination of the internal components and wear items are measured, a specific maintenance schedule can be determined.
For best results, it is recommended that the pump be removed from service annually for examination.
Fluid
Temperature
Maximum Surface
Temperature
Temperature
Class
Maximum Allowable
Surface Temperature
21ºC (70ºF)
55ºC (131ºF)
T6
85ºC
77ºC (170ºF)
76ºC (168ºF)
T5
100ºC
104ºC (220ºF)
84ºC (183ºF)
T4
135ºC
Содержание DB11 series
Страница 1: ...1 ...
Страница 16: ...16 DB11 DB15 Exploded View Parts Diagram ...
Страница 22: ...Part Number 107403 R18 1 10 2018 Order fax 814 459 3460 Tech Service 800 888 3743 ...