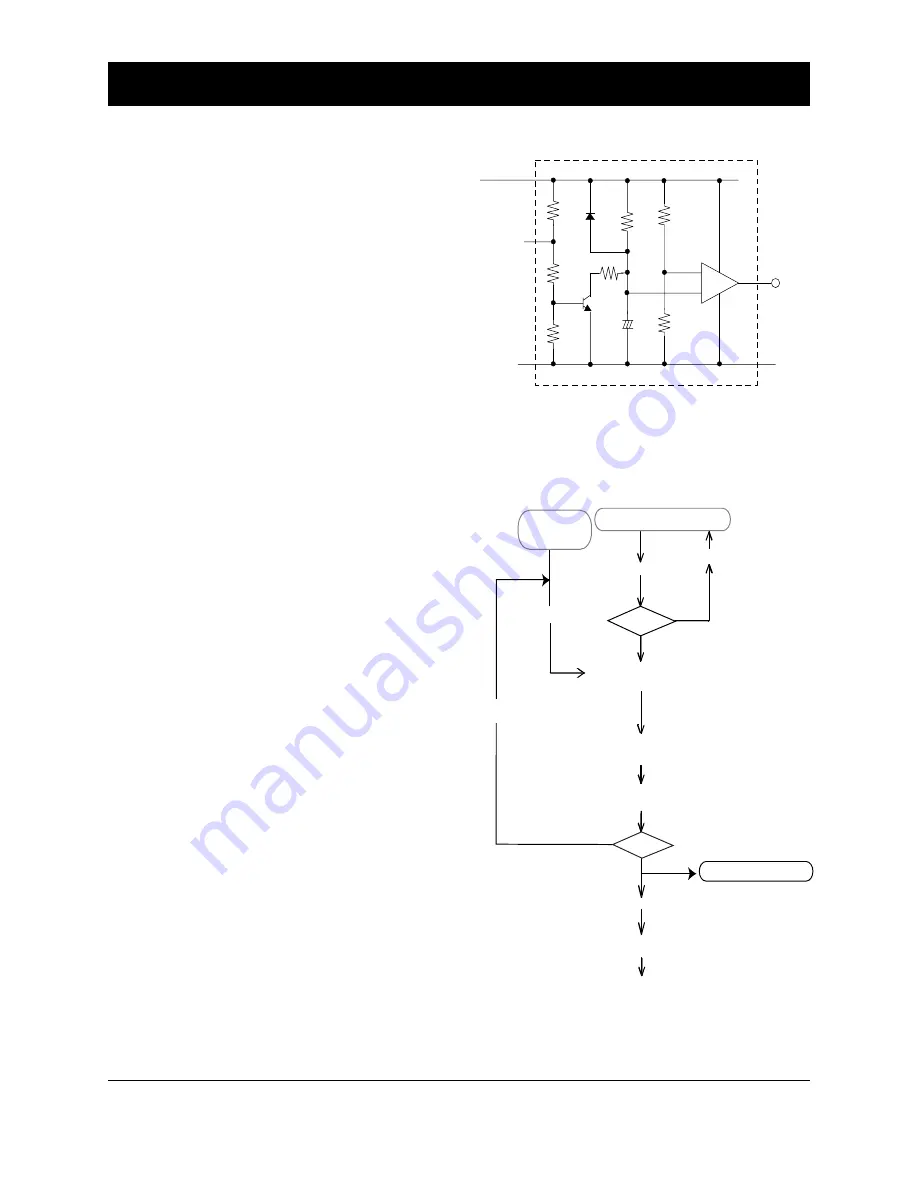
Revised
08/03
5
APPLICATION NOTES FOR TGS2611
Figure 8 - Manufacturing process flowchart
1-8
Alarm delay circuit
To prevent false alarms caused by transient
interference gases such as alcohol in cooking
vapors, a delay circuit modification such as that
shown in Figure 7 can be used. The alarm signal
generated by this circuit should be connected to
the comparator in the basic circuit (see Figure
1). The recommended timer period for alarm
delay is 15 seconds--the timer function should
be created by selecting the proper combination
of C
4
and R
15
.
1-9
Application circuit
An application circuit which incorporates all of
the advice included in Secs. 1-1 through 1-8 can
be seen in Appendix 1.
2. Manufacturing Process (
see Fig. 8
)
2-1
Handling and storage of sensors
Prior to usage, sensors should be stored at room
temperature in a sealed bag containing normal
clean air. During manufacturing, sensors should
be handled in a clean air environment and at
room temperature. Clean air refers to air free of
contaminants, excessive dust, solvent vapors,
etc. Room temperature should be 20~25˚C.
2-2
R
L
selection
Choose the proper resistor for R
L
by referring to
the ID number of the sensor and Table 1.
2-3
PCB assembly
Flux should be sufficiently dried before sensors
are assembled onto the PCB to avoid any
contamination of the sensor by flux vapors.
2-4
Sensor assembly
Manual soldering of the sensor to the PCB is
strongly advised. Solders composed of
Sn63:Pb37 or Sn60:Pb40 with non-chloric resin
flux (MIL: RMA Grade; for example, Almit KR-
19) are recommended for usage.
2-5
Final assembly
Avoid any shock or vibration which may be
caused by air driven tools. This may cause
breakage of the sensor’s lead wires or other
physical damage to the sensor.
Figure 7 - Alarm delay circuit
+
-
V
C
GND
+
Alarm signal
(Active = 'L')
15 sec. time delay circuit
Delayed alarm
signal
(Active = 'L')
R
8
R
12
R
13
Tr
C
4
R
10
R
9
R
15
D
6
IC
3
R
14
OK
Acceptance of
classified sensor
*3
(PCB, casing etc.)
(
≥
48 hours)
NG
OK
NG
PCB Assembly
Repair
PCB Test
Sensor and R
L
Assembly
Final Assembly
Preheating
Packing
Storage
Shipping
Acceptance of components
Quality control sampling
*Alarm concentration
*Long term stability
RL selection
(manual soldering)
Investigation
Gas Test