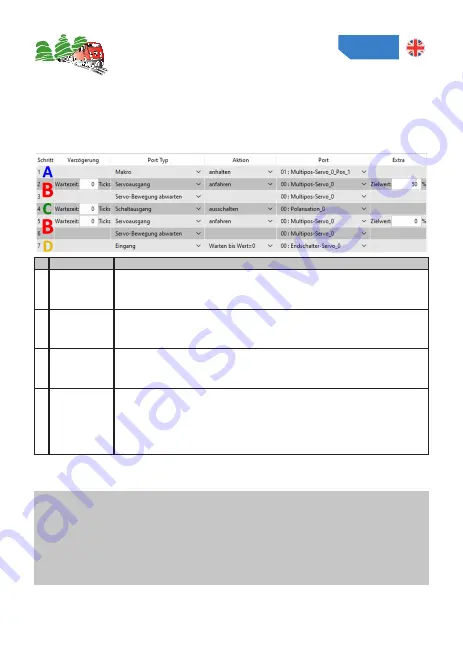
Manual ReadyServoTurn
© 2022 FichtelBahn®
Manual Version 1.0
Technical changes and errors reserved
Page 24
FichtelBahn
Line
R
eady
Macro example:
Servo 0 is moved from target position 100% to target position 0%, the associated frog
polarisation is reversed by relay 0 and the servo movement is monitored via input 0.
As an example, the following illustration shows the associated macro generated by the
configurator. The sequence consists of 4 actions marked with A, B, C, D.
Function
Description
A
Conflict protection The first macro step terminates the opposing macro, which is responsible for the opposite movement
of the turnout from 0% to 100%. This step is very useful if an executed switch command is followed
by an immediate counter command and the servo has a long turnaround time. In this case, the op
-
posing macro is aborted and not executed to the end.
B
Servo movement
In the second step, servo 0 is moved from its current position to the target position of 50% with
the servo settings from servo 0. The 4th macro step is only started when the servo has reached the
calculated target position of 50%. The function in macro step 3 is responsible for this delay (wait).
Similarly, macro steps 5 and 6 continue the servo movement to the 0% end position.
C
Switch relay
Macro step 4 stops the servo movement exactly at the middle position of the servo movement and
switches the state from relay ON to relay OFF. This intermediate step at 50% of the servo movement
is important because it ensures that the point blades have no contact with one side of the rail and
can be switched over safely.
D
Feedback
The last macro step ensures that the macro is not terminated if the position feedback is not set to
“true”. If no movement occurs due to a technical error in the servo or its mechanics, then the current
value = 1, is not changed to the new value = 0. In this case the macro step waits for the value = 0 and
the macro cannot be terminated. The host that triggered the switching command via an accessory
does not receive an accessory feedback “Macro completed” from the module and therfore the route
could not be reserved or set. An accessory could also report back an error condition. (see feedback
in the Accessories category)
Please notice:
The sequences with the node configurator could have discrepancies with the connected inputs, polarity
or servo direction. In this case, you could change the mechanics or the polarity of the connection.
However, it is much easier if you adjust the settings in the created macro in such a case:
the relay switches the wrong polarity
--> swap action “Turn off” to “Turn on”.
the servo moves in the wrong direction
--> change the target position from 0% to 100%.
the input reacts to the wrong state
--> swap action “Wait until value=0” to value=1
The opposing macro from the target position 0% to 100% has the same structure, except that it has
inverted settings.