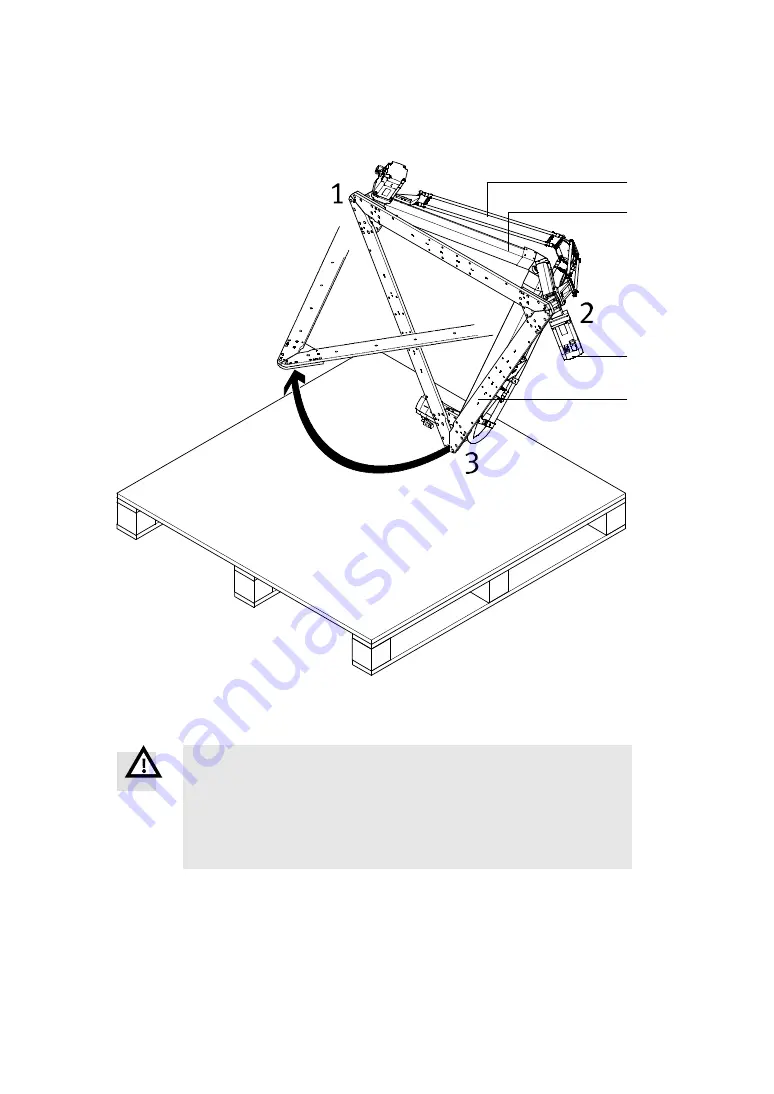
3
Assembly and installation
Festo – GDCP-EXPT-KM-KOMP-EN – 1204a – English
21
Turning and installing the tripod kinematics
1
2
3
4
1
Pair of rods
2
Toothed belt axis
3
Motor
4
Mounting frame
Fig. 3.11
Warning
Crushing of body parts. If improperly fastened, the tripod kinematics can come undone
and fall down.
•
Fasten the tripod kinematics on the frame in accordance with the specifications on
the assembly drawing.
•
Observe the specifications for mounting (
Chapter 3.6 and 3.7).
•
Secure the screw connections.