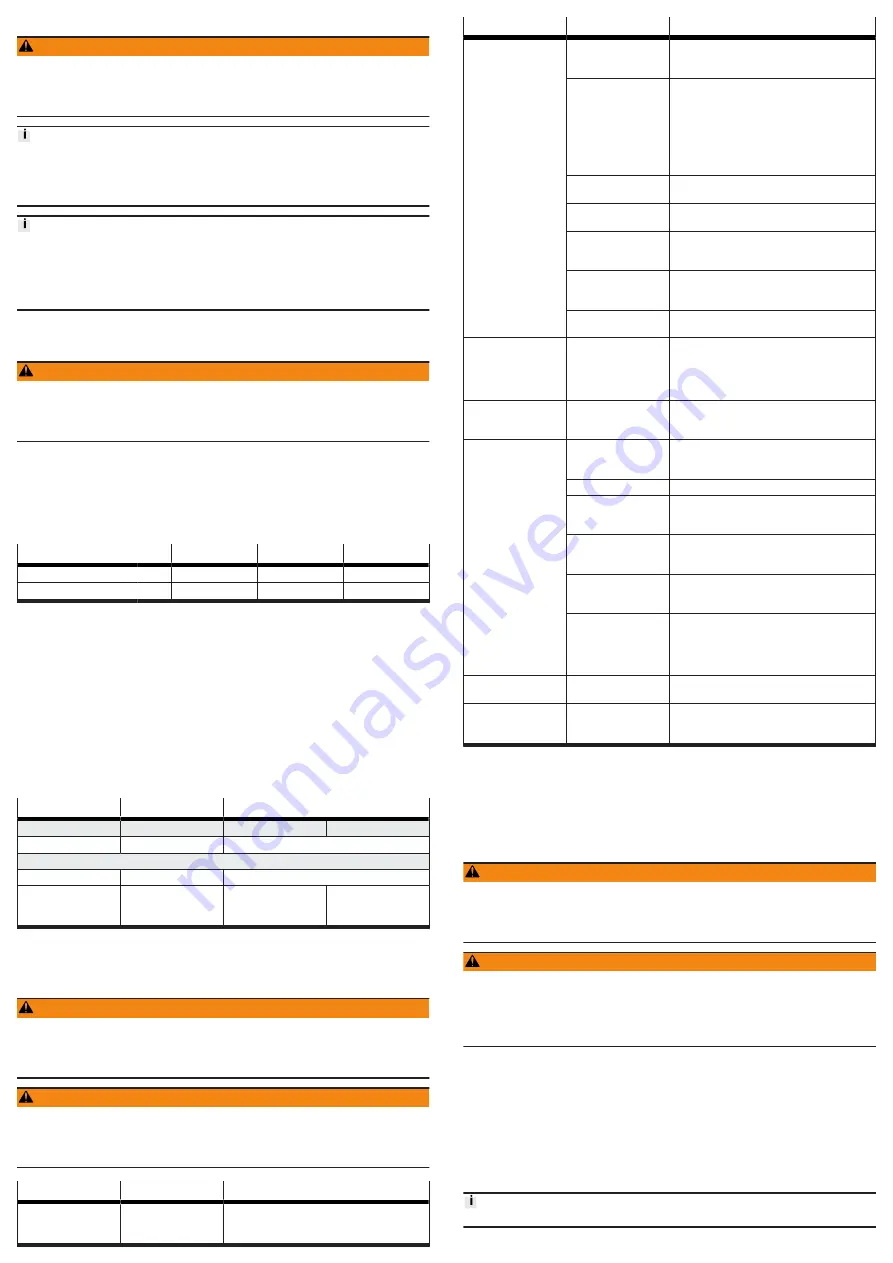
8
Operation
WARNING
Risk of injury due to unexpected movement of components.
• Protect the positioning range from unwanted intervention.
• Keep foreign objects out of the positioning range.
• Perform commissioning with low dynamic response.
Torque on the Piston Rod
During commissioning and operation, the piston rod may only be operated
without torque.
If external torques occur, an external guide must be used.
Lubrication Run During Operation
Observe the following lubrication travel intervals.
• With working stroke less than 2 x spindle pitch... P:
• Perform a lubrication run within 10 travel cycles with a minimum stroke of
≥2.5 x spindle pitch.
9
Maintenance
9.1
Safety
WARNING
Unexpected movement of components.
Injury due to impacts or crushing.
• Before working on the product, switch off the control and secure it to prevent it
from being switched back on accidentally.
9.2
Checking the cylinder elements
Checking the reversing backlash (ESBF-LS only)
•
Check the reversing backlash of the piston rod at every maintenance interval
(e.g. lubrication interval).
If the maximum permissible reversing backlash is exceeded, the cylinder
should be replaced.
Size
32
40
50
Spindle pitch ...P
2.5
3
4
Max. reversing backlash
[mm]
0.62
0.75
1
Tab. 12: Maximum permissible reversing backlash, ESBF-LS-32/40/50
9.3
Cleaning
–
If the piston rod is dirty, clean it with a clean, soft and lint-free cloth without
cleaning agents and then apply the lubricant thinly to the piston rod.
–
Clean the other product components with a clean, soft cloth and non-abrasive
cleaning agents.
For use with reduced particle emission:
–
Remove abraded particles and dirt from the product:
–
Prior to initial commissioning.
–
Regularly during operation.
9.4
Lubrication
Lubrication Interval and Accessories
Lubrication
Lead screw
Piston rod
ESBF-...
ESBF-...
ESBF-...-F1
Lubrication interval
Lubrication for life
If required, e.g. if the grease layer is too low.
Accessories
Lubrication point
—
Surface
Lubricant
—
Roller bearing grease
LUB-KC1
Roller bearing grease,
suitable for use in the
food industry LUB-E1
Tab. 13: Overview of Lubrication Intervals and Accessories
10
Malfunctions
10.1
Fault Clearance
WARNING
Unexpected movement of components.
Injury due to impacts or crushing.
• Before working on the product, switch off the control and secure it to prevent it
from being switched back on accidentally.
WARNING
Risk of injury due to unexpected movement of components.
• Protect the positioning range from unwanted intervention.
• Keep foreign objects out of the positioning range.
• Perform commissioning with low dynamic response.
Malfunction
Possible cause
Remedy
Wear on the lead screw
ESBF-LS.
Reversing backlash is
too large.
–
Contact local Festo Service.
–
Replace cylinder
Malfunction
Possible cause
Remedy
Loud running noises
or vibrations or rough
running of the cylinder.
Coupling distance too
short.
Observe permissible coupling spacings
è
Instruction manual for motor mounting kit,
Tensions
–
Install the cylinder so it is free of tension. Note
the flatness of the contact surface
–
Change the layout of the attachment compo-
nent (e.g. payload).
–
Align cylinder and attached guide element par-
allel to each other.
–
Use external guide.
Current controller set-
tings.
Optimise controller data (e.g. velocity, accelera-
tion, ...).
Resonant oscillation of
the cylinder.
Change the travel velocity.
Wear on bearing or
guide.
–
Contact local Festo Service.
–
Replace cylinder
Reversing backlash is
too large.
–
Contact local Festo Service.
–
Replace cylinder
Insufficient lubrication
of the piston rod.
Lubricate the piston rod
Lubrication Intervals and Accessories.
Oscillations at the
piston rod.
Operation at the reso-
nance point of the cyl-
inder.
–
Change the travel velocity.
–
Change the acceleration.
–
Increase the cylinder rigidity (for example
shorter support distances).
–
Change the payload geometry.
Long oscillations of the
profile.
Resonant frequency of
profile and payload too
low.
–
Increase the cylinder rigidity (for example
shorter support distances).
–
Change the payload geometry.
Piston rod does not
move.
Coupling slips.
Check the mounting of the shaft-hub connection
è
Instruction manual for the motor mounting
Loads too high.
Reduce forces and torques. Consider dynamics.
Threaded drive
blocked.
–
Contact local Festo Service.
–
Replace cylinder
Pre-tension of toothed
belt too high in parallel
kit.
Reduce the pretension of the toothed
belt
è
Instruction manual for parallel kit,
Operation at the lower
ambient temperature
limit.
–
Optimise controller data (e.g. velocity, acceler-
ation, ...).
–
Use gear unit.
Piston rod stuck in the
mechanical end posi-
tion.
Manually Releasing a Jam:
–
Switch off the controller and safeguard it from
being switched on again unintentionally.
–
Remove motor and motor mounting kit.
–
Rotate drive shaft freely.
Overruns the end posi-
tion.
Sensor does not
switch.
Check sensor, installation and parameterisation.
Idling torque too high.
Wear in the drive train.
–
Contact local Festo Service.
–
Replace cylinder
Tab. 14: Overview of Fault Clearance
10.2
Repair
–
Observe the instructions for dismantling
–
Send the electric cylinder to the Festo repair service.
–
Information about spare parts and accessories
11
Disassembly
WARNING
Unexpected movement of components.
Injury due to impacts or crushing.
• Before working on the product, switch off the control and secure it to prevent it
from being switched back on accidentally.
WARNING
Risk of Injury due to Unexpected Movement of Components
For vertical or slanted mounting position: when power is off, moving parts can
travel or fall uncontrolled into the lower end position.
• Bring moving parts of the product into a safe end position or secure them
against falling.
1. Disconnect electrical installations.
2. Remove the mounted attachment component.
3. Remove the attached accessories.
4. Remove motor and mounting kit.
5. Remove the mounting attachments.
6. Observe transport information
12
Technical data
12.1
Technical data, mechanical
Use the Festo sizing software for sizing the drive