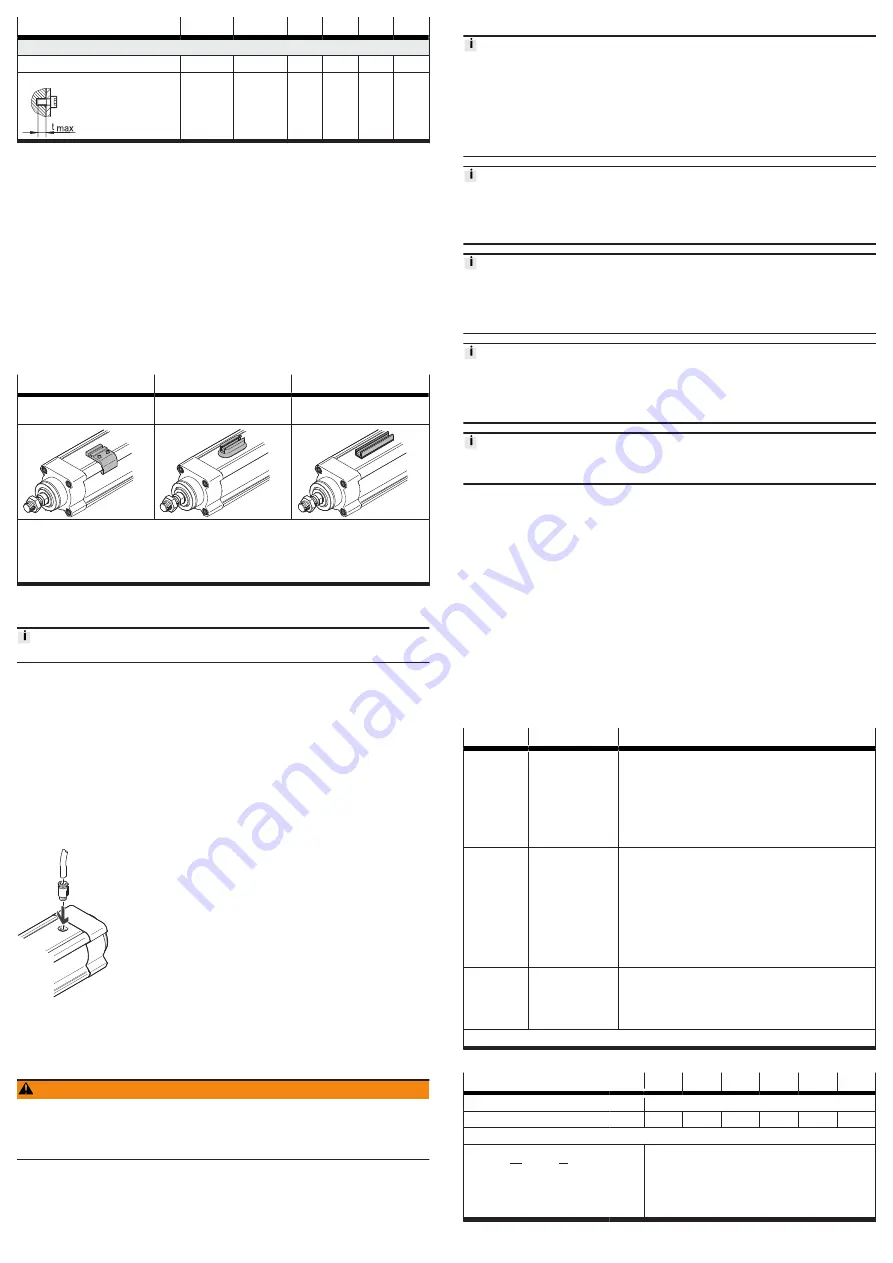
Size
32
40
50
63
80
100
Piston rod with female thread ESBF -...- F
Screw, lock nut
M6
M8
M10
M10
M12
M12
Max. screw-in depth t
max
[mm]
12
12
16
16
20
20
Tab. 8: Information on attachment components
6.6
Mounting accessories
Requirement
–
No collision with mounting and sensor components in the movement space of
the attachment component.
–
Protection against uncontrolled overtravel of the end positions.
–
Referencing to reference switch or end position.
–
Query of end positions or intermediate positions.
–
Avoidance of hard impacts at the end positions.
–
Prevention of contamination in the slots.
1. Select accessories
2. Mount the sensor (reference or query):
–
Mount the sensor rail or mounting kit (depending on the type of mounting).
–
Align sensor and mount it at the switching position.
Instruction manuals
Mounting kit SMB
Mounting kit CRSMB
Sensor rail SAMH
–
mounting on profile lug
–
central mounting on the pro-
file
–
central mounting on the pro-
file
–
Protect the sensor from external magnetic or ferritic influences (e.g. min. 10 mm distance to slot
nuts).
–
Preferably use hardware limit switches with normally closed function (protection guaranteed even
in case of sensor failure).
Instruction manual
Tab. 9: Overview of sensor mountings
Connecting pressure compensation (ESBF -...- S1 only)
The standard version of the ESBF is supplied with a press-fitted sinter filter.
The pressure compensation port permits the reduction of negative or excess
pressure in the cylinder interior. Pressure compensation may only take place in
clean ambient air.
Alternatives to pressure compensation via the environment:
–
Operation in a dust-free and dry area
–
Connection to a large expansion tank
–
Connection of sealing air (for example excess pressure with maximum 0.2 bar).
Position of the pressure compensation port:
–
ESBF-32/40/50: in the drive cover
–
ESBF-63/80/100: in the cylinder profile
1. Remove protective cap.
2. Mount the screw fitting and connect the hose.
Fig. 3: Mount fitting (example: cylinder profile connection)
7
Commissioning
7.1
Safety
WARNING
Risk of injury due to unexpected movement of components.
• Protect the positioning range from unwanted intervention.
• Keep foreign objects out of the positioning range.
• Perform commissioning with low dynamic response.
7.2
Performing commissioning
Block-shaped acceleration profiles (without jerk limitation) can have the following
effects:
• High mechanical loads on the lead screw due to high force peaks.
• Overshooting effects during positioning.
• Swinging up of the entire system
Recommendation: Reduce high force peaks in the acceleration and deceleration
phases by using the jerk limitation.
When the motor is removed, the motor encoder loses its absolute reference to the
reference mark (e.g. by turning the motor drive shaft).
• Carry out a homing run after every motor mounting in order to establish the
absolute reference between the motor encoder and the reference mark.
Torque on the Piston Rod
During commissioning and operation, the piston rod may only be operated
without torque.
If external torques occur, an external guide must be used.
Running noises during operation
Identically constructed axes can generate different running noises depending on
the parameterisation, mode of operation, type of mounting, installation environ-
ment and components.
For use with reduced particle emission
• Clean product
Requirement
–
Mounting of the drive system checked.
–
Installation and wiring of the motor checked.
–
No foreign objects in the movement space of the drive system.
–
Maximum permissible feed force and drive torque not exceeded as a function
of acceleration, deceleration (e.g. stop function, quick stop), velocity, moving
mass and mounting position.
–
Cylinder not mechanically overloaded and dynamic setpoint deviation not
exceeded (e.g. overrunning the end position) due to force and torque peaks
or overshoot effects.
Limit overloads and overruns by jerk limitation, lower acceleration and deceler-
ation setpoints or optimised controller settings.
–
Control and homing travel at reduced velocity, acceleration and deceleration
setpoint values.
–
No test run to mechanical end stops.
–
Software end positions ≥0.25 mm away from the mechanical stops.
Steps
Purpose
Note
1. Check
travel
Determine the
direction of travel of
the piston rod
–
Direction of movement of piston rod (clockwise spindle):
–
Retracting: rotate cylinder drive shaft clockwise.
–
Extending: rotate cylinder drive shaft anti-clockwise.
–
The direction of motion of the piston rod for positive and
negative position values depends on the mounting posi-
tion of the motor on the cylinder.
–
Set a required reversal of direction of rotation via parame-
ters in the controller or controller.
2. Homing
Determination of
the reference point
and adjustment of
the dimensional ref-
erence system
–
during the initial
start-up proce-
dure
–
after replacement
of the motor
Permissible reference points:
–
towards reference switch.
Travel at reduced velocity
–
against the end position on the motor side.
do not exceed maximum values
Further information
è
Instruction manual of the drive
3. Test run
Checking the oper-
ating conditions
Check application requirements:
–
Piston rod runs through the complete travel cycle in the
specified time.
–
The piston rod stops travel when a limit switch or software
end position is reached.
After a successful test run, the drive system is ready for operation.
Tab. 10: Commissioning steps
Size
32
40
50
63
80
100
Max. stop velocity
[m/s]
0.01
Max. stop energy
[mJ]
0.03
0.05
0.07
0.15
0.38
0.60
Calculation of the maximum stop energy
•
!"
=
$
%
2 &m +
'
(
'
)
*
–
v = max. stop velocity
–
m = mass of all linear moving components
–
J
R
= mass moment of inertia of all rotating compo-
nents
–
J
L
= mass moment of inertia per kg payload
Tab. 11: Speed and energy at the end positions