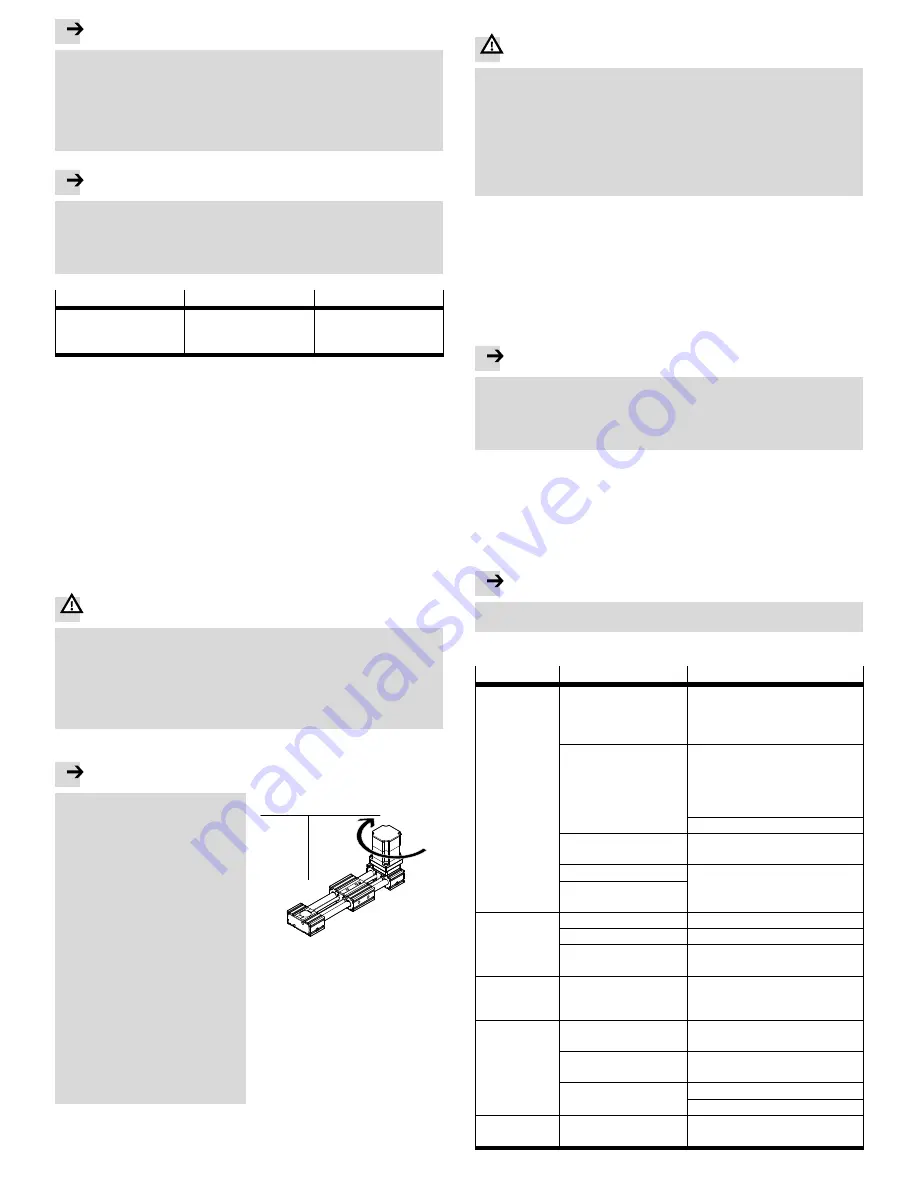
Note
Block-shaped acceleration profiles (without jolt limitation) cause high peaks in
the motive force that can lead to an overloading of the drive. In addition,
positions outside the permissible range may occur as a result of overswing
effects. A jolt-limited acceleration specification reduces vibrations in the entire
system and has a positive effect on stress in the mechanical system.
Check which closed-loop controller settings can be adapted
(e.g. jerk limitation, smoothing of the acceleration profile).
Note
The elasticity of the toothed belt delays the acceleration behaviour of the
ELGR/ELGG and results in larger acceleration values than those set on the
controller (spring effect).
Take into account possible deviations from the acceleration values set on the
controller.
1. Check travel
2. Homing
3. Test run
Determining the
approach direction of the
motor
Comparing the real
situation with the image
in the controller
Checking the overall
behaviour
Fig. 13 : Definitions
1. Start
check travel
with low dynamic response.
In spite of equal control, even motors of the same type sometimes turn in the
opposite direction due to the circuitry.
2. Start
homing
in accordance with the operating instructions for your motor drive
system with low dynamic response to the reference switch.
3. Start a
test run
with low dynamic response.
4. Check whether the ELGR/ELGG fulfils the following requirements:
– The slide must be able to move through the complete intended positioning
cycle.
– The slide must stop as soon as it reaches a limit switch.
5. In the event that the proximity sensors fail to respond:
è
Chapter 11 “Fault
clearance” and the operating instructions for the proximity sensors.
7
Operation
Warning
Payloads can cause personal injury and material damage (risk of crushing).
Make sure that:
– nobody can place his/her hand in the path of the moving components
(e.g. through a protective guard),
– there are no foreign objects in the path of the moving components.
It should not be possible to touch the ELGR/ELGG until the load has come to a
complete standstill.
If the motor turns in the wrong direction:
Note
When a motor with absolute value
encoder is dismantled
(e.g. when turning the motor around),
the reference position is lost.
Start homing in accordance with
the chapter “Commissioning” to
re-reference the positioning cycle.
For the ELGR with the OMS variant
(Optimized Motion Series), the previ
ous parameter set of the OMS system
is invalid when moving the motor. A
new parameter set is essential.
Load the new parameter set
according to the new motor
position (M) into the controller
(
è
www.festo.com).
Repeat the commissioning process
with the new parameter set. Com
missioning with the OMS identifica
tion number specified on the
product is no longer possible.
Fig. 14
FL
FR
RL
RR
(M)
8
Maintenance and care
Warning
Payloads can cause personal injury and material damage (risk of crushing).
If a toothed belt breaks in combination with a vertically or diagonally fitted
ELGR/ELGG, the work load will fall down.
If there is evidence of wear, return the ELGR/ELGG to Festo for repair.
Signals from the control system can cause unintentional movement of the
ELGR/ELGG.
Switch off the control system when conducting any work on the ELGR/ELGG
and secure it from being restarted accidentally.
Cleaning and maintenance:
Clean the ELGR/ELGG as required with a soft cloth.
Any media which will not damage the material may be used as cleaning agents.
Relubrication of the ELGR/ELGG is not permissible.
Regularly check the play in the plain-bearing guide according to your
application. Depending on the load, the guide backlash rises with increasing
duration of operation.
9
Disassembly and repair
Note
Retensioning of the toothed belt reduces its service life considerably. In addi
tion, the technical data, e.g. the feed constant, change.
Make sure that the toothed belt is not retensioned.
The pretension of the toothed belt is designed in such a way that it does not
need to be retensioned over its service life.
Recommendation: Send the ELGR/ELGG to our repair service.
This way the required fine tuning and tests will be taken into special considera
tion.
Information about spare parts and accessories can be found at:
www.festo.com/spareparts
10
Accessories
Note
Please select the corresponding accessories from our catalogue
è
www.festo.com/catalogue
11
Fault clearance
Malfunction
Possible cause
Remedy
Squeaking
noises,
vibrations or
rough running
The coupling is mounted
too tight
Comply with the permissible
coupling distances (
è
Assembly
instructions for the motor
mounting kit)
Tension
Install the ELGR/ELGG so it is free
from tension (observe the
evenness of the bearing surface
è
Chapter 5.1 Mechanical
installation)
Modify travel speed
Incorrect regulator
settings
Modify the regulator parameters
Defective bearing
Return the ELGR/ELGG to Festo for
repair
Toothed belt or slide
elements worn
Slide does not
move
Loads too high
Reduce load mass
Guide jammed
Reduce torques
Clamping hub spins
Check mounting of the motor
mounting kit (coupling)
Slide travels
beyond the end
position
The proximity sensors do
not react
Check the mounting level of the
proximity sensors, connections and
controller
Toothed belt
jumps off
Toothed belt
pretensioning too low
Return the ELGR/ELGG to Festo for
repair
Incorrect regulator
settings
Change the regulator parameters
Loads too high
Reduce load mass
Reduce travel speed
Stroke of ELGG
too low
Incorrect position of the
central support
Attach the central support at the
exact central position
Fig. 15