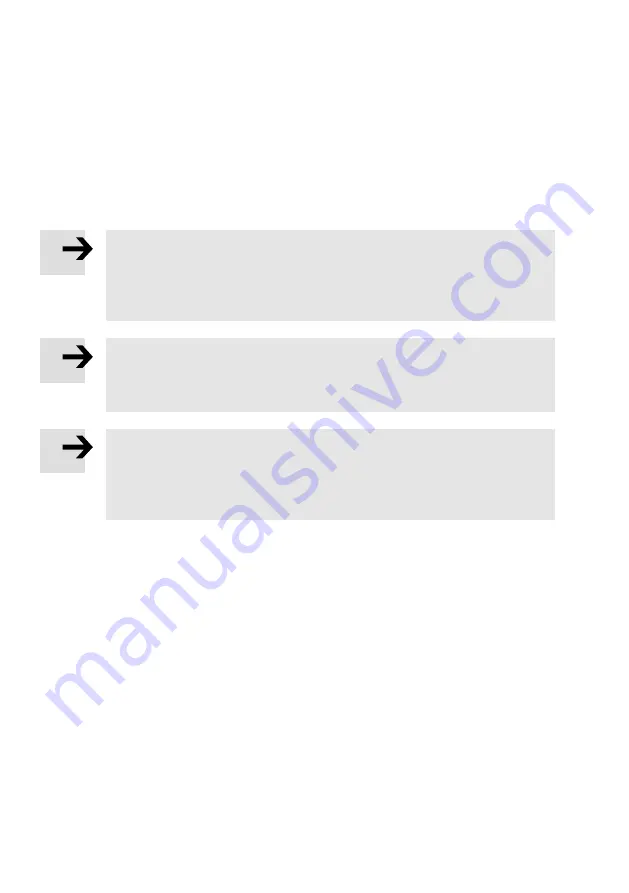
EHMB
6
Festo – EHMB – 2019-05c English
3
Function
The EHMB rotary/lifting module combines 2 movements, rotation and stroke, in one product. A toothed
belt transfers the rotation of a motor to a hollow shaft. The stroke of a pneumatic/electric cylinder is
transferred via a connection bolt
aA
to the drive flange
1
and the grooved shaft guide
6
of the EHMB.
The shafts run in ball bearings. The reference position of the rotation can be detected with the aid of an
inductive proximity sensor in the threaded hole
9
. The position of the stroke is detected on the cylinder.
Note
The EHMB is not braked: If the input torque of the drive motors is not applied, the
rotary/lifting module is freely movable. Generally, self-locking of the complete system
can be achieved by the use of motors with a spring-loaded holding brake or with high
self-braking torque.
Note
Without stop nut
7
and linear drive, the shaft
6
can slip out of the seat
of the EHMB. Then a repair by Festo is required.
If the linear drive is dismantled, make sure that the stop nut is not removed.
Note
The positioning times and permitted mass moments of inertia on the drive depend to
a large extent on the flange-mounted motor.
Use Festo's “PositioningDrives” design tool to determine the best combination of
products (
è
www.festo.com).
Use the following motors from Festo (
è
www.festo.com/catalogue).
Doing this will ensure you are operating two devices that are perfectly harmonised with one another.
When using other motors:
Observe the limit values for torques and rotational speeds (
è
Observe the interface geometries (e.g. for the drive shaft
è
www.festo.com/catalogue).
4
Transport
Take product weight into account (
è