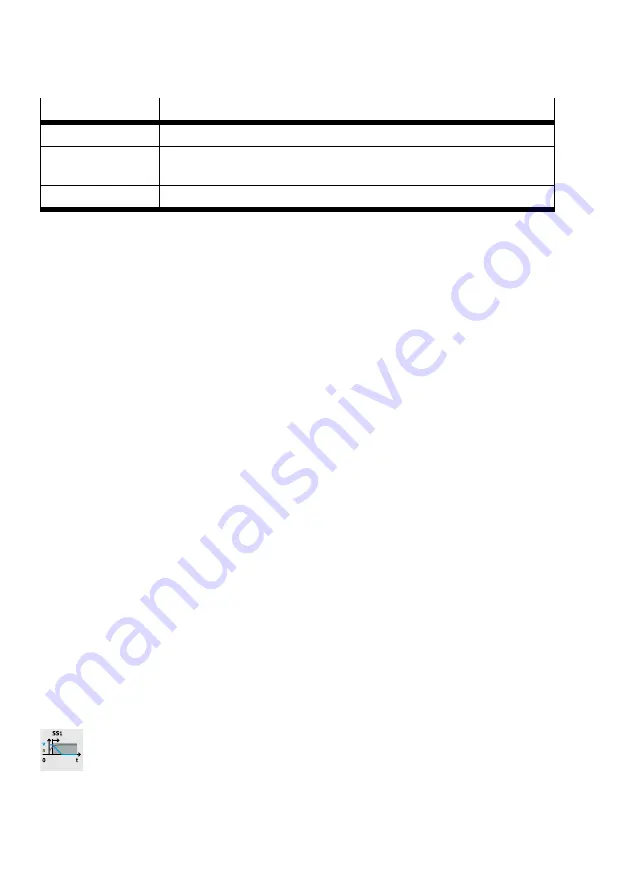
Term/abbreviation
Explanation
SBA
Feedback, SBC active
t
SBA,Out
Max. delay for diagnostic feedback (≤ permissible reaction time when a
safety sub-function is requested
1)
+ 10 ms)
n
Rotational speed
1) See Technical data, safety reference data for SBC
Tab. 6 Legend for SBC timing
Requirements for the brakes
•
Check the brakes used for suitability for the application.
As a rule, the brakes used are holding brakes. This means the brakes are well suited to keeping the
motor at a standstill.
The internal holding brake of the motor is also used for the safety sub-function SBC. Please be aware
of the following constraints:
–
The holding brake must be designed for the load torque to be stopped.
–
The specifications for the holding brakes permit a certain amount of movement until the full hold-
ing torque is reached. This must be taken into account in the design of the vertical axes and con-
figuration of the safety sub-function SBC.
–
“Reserves” should be factored in when selecting the motor plus holding brake, e.g. operation at
no more than 2/3 of the nominal torque. The holding brakes in the motors are usually designed so
that the motor shaft will come to a standstill without coasting at loads below 70 % of the nominal
torque.
–
Depending on the hazard situation, the holding brake must be designed with a correspondingly
higher nominal torque.
–
When designing the holding brake, the additional load torque for the brake test must be con-
sidered.
The number of clamping and braking applications for the clamping unit is limited due to wear.
1. Observe the corresponding specifications in the data sheet.
2. Replace clamping unit before the maximum number of clamping applications is reached.
3. Replace clamping unit if the emergency brake features of the clamping unit have to be used. Pay
attention to the number of permissible emergency braking applications.
Brake test
•
Check whether a brake test is required. The DGUV information sheet “Gravity-loaded axis”
provides information on this.
4.1.4
Safety sub-function SS1
Fig. 8 Symbol for SS1
The function described here implements the safety sub-function SS1 according to EN 61800-5-2.
Product overview
16
Festo — CMMT-AS-...-S1 — 2018-10a