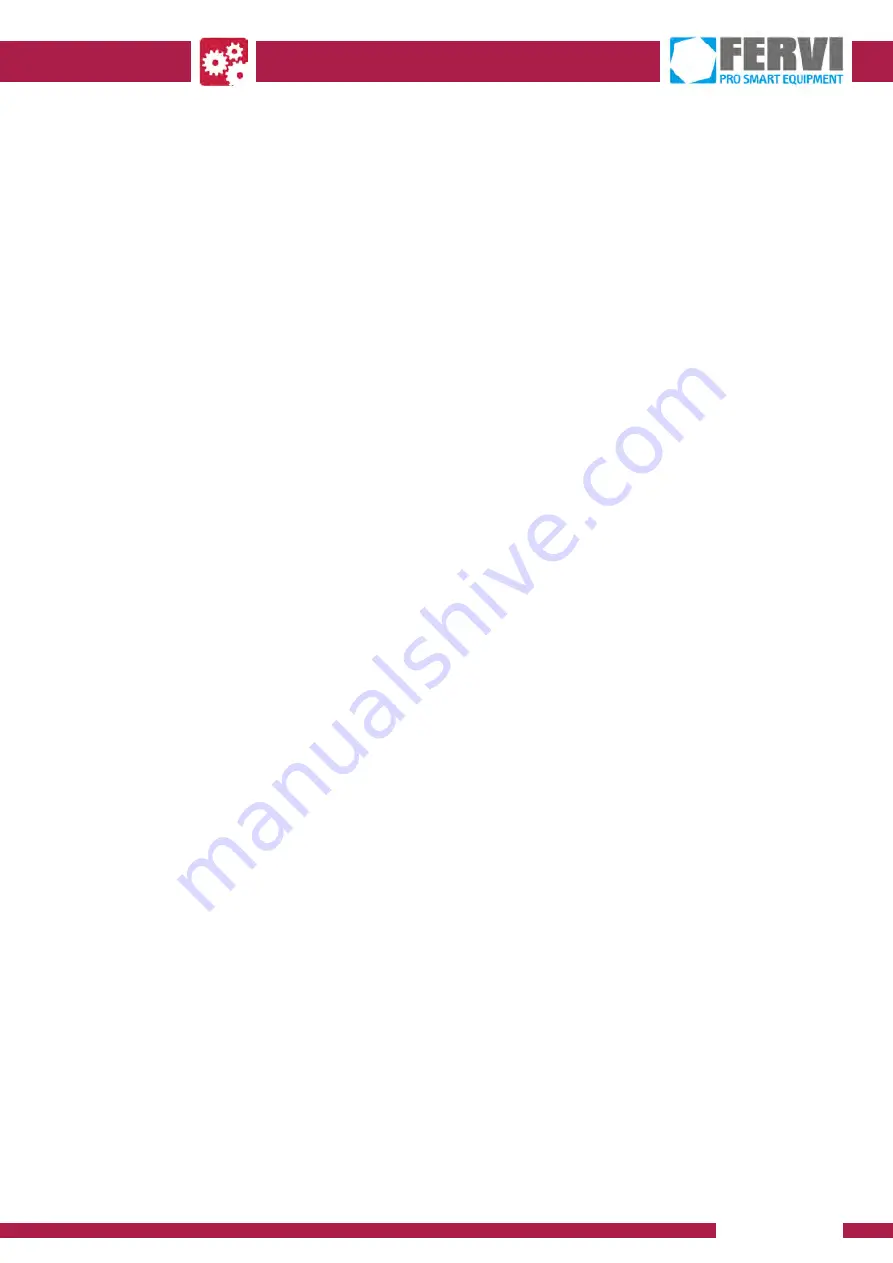
MACCHINE E
ACCESSORI
Pagina 5 di 43
A
ll
rig
h
ts
o
f re
p
ro
du
ct
io
n
a
n
d
d
iv
u
lg
at
io
n
o
f t
h
is
T
ech
n
ical
M
an
u
al
an
d
m
en
tio
n
ed
a
n
d
/
o
r a
tta
ch
ed
d
ocu
m
en
ta
tio
n
, a
re
res
erv
ed
. I
t i
s
st
rict
ly
fo
rb
id
d
en
to
rep
ro
du
ce,
p
u
b
lis
h
o
r d
is
tr
ib
u
te
a
n
y
in
fo
rm
at
io
n
fr
o
m
th
is
m
an
u
al.
C
o
p
yri
gh
t b
y
FE
R
V
I
1
INTRODUCTION
This manual is delivered with the machine, and it must be regarded as an inseparable part of
it.
The manufacturer holds all ownership to material and intellectual property of this manual;
any disclosure or copying, even partial, of this publication without prior written consent is
forbidden.
The purpose of this manual is to convey the necessary knowledge for the use and
maintenance of
Drill press with drive belt Art. 0260
and to create a sense of responsibility
and knowledge of the capabilities and limits of this machine entrusted to the operator.
Operators must be properly trained and prepared; therefore, please make sure this manual is
read and consulted by the staff responsible for commissioning, operating and maintaining the
Drill press with drive belt
. This is to make all operations the safest and most effective
possible for those who carry out these tasks.
Therefore, it is imperative to strictly comply with the requirements in this manual, a
necessary condition for safe and satisfactory operation of the machine.
Prior to installation and use of the
Drill press with drive belt
, the authorized personnel
shall:
carefully read this technical document;
know which protections and safety devices are available on the machines, their location
and how they work.
It is the responsibility of the buyer to ensure that users are properly trained, that they are
aware of all the information and instructions in this document and that they are aware of the
potential risks that exist while working with the
Drill press with drive belt
.
The manufacturer waives any and all responsibility for damage to people and/or
things caused by non-observance of the instructions in this manual.
The
Drill press with drive belt
has been designed and built with mechanical guards and
safety devices designed to protect the operator/user from possible injury. It is strictly
forbidden to modify or remove guards, safety devices and caution labels. If you have to do so
temporarily (for example, for cleaning or repair requirements), please make sure that no one
can use the machine.
Modifications to the machine carried out by the user must be considered their sole
responsibility, therefore the manufacturer waives any and all responsibility for any
damage caused to persons and/or property resulting from maintenance performed
by unqualified personnel and in a manner unlike the operating procedures shown
below.
fervi.com