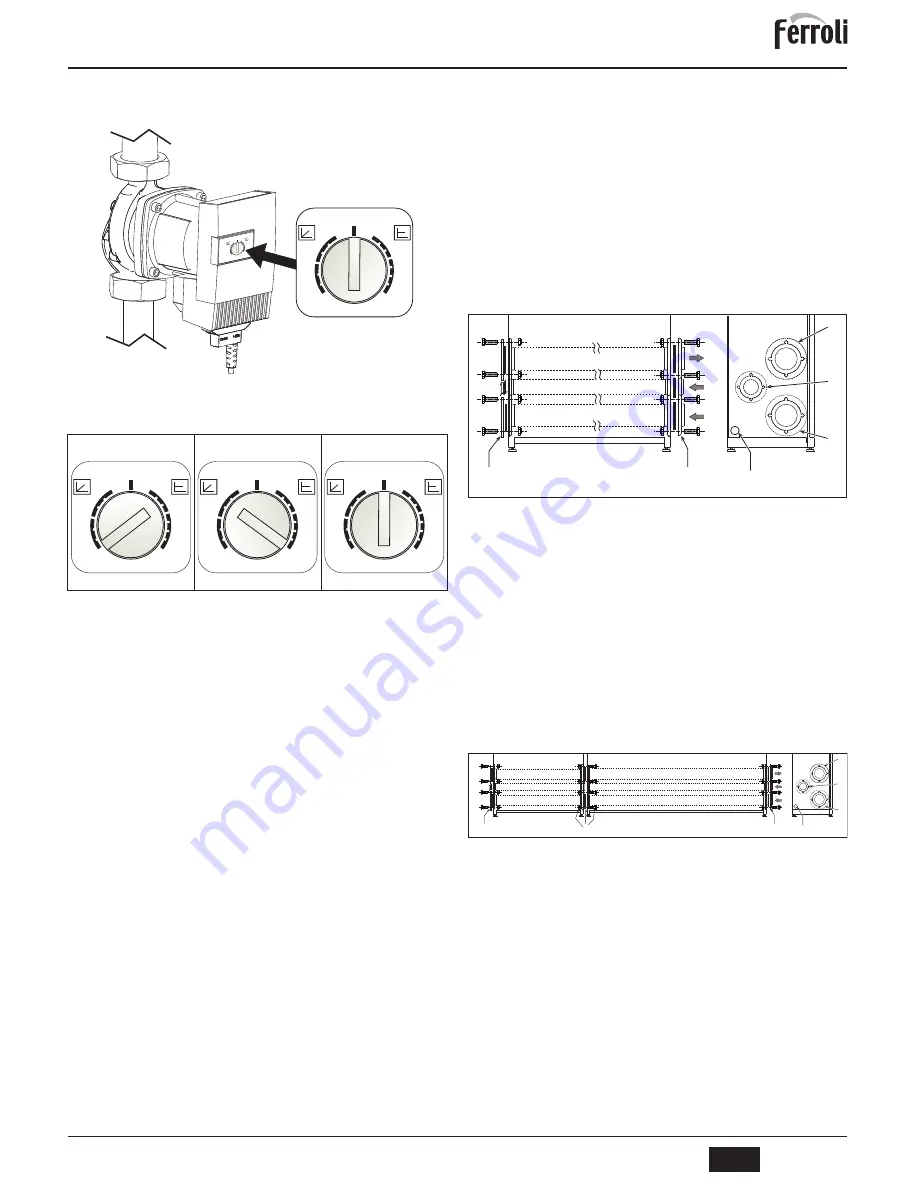
ENERGY TOP B
75
EN
High-efficiency circulating pump (optional)
The factory setting is suitable for all installations; however a different operation strategy
can be set with the speed selector (see fig. 19), depending on the characteristics of the
system.
fig. 19
- Setting Dp-v Proportional head
(fig. 20)
The circulating pump head will be automatically reduced with the decrease in flow rate
required by the system. This setting is optimum for systems with radiators (2 pipes or sin-
gle pipe) and/or thermostatic valves.
The strong points are the reduction in power consumption with the decrease in system
demand and reduction of noise in radiators and/or thermostatic valves. The operating
range is from min. (2) to max. (8).
- Setting Dp-v Constant head
(fig. 21)
The circulating pump head will remain constant with the decrease in flow rate required
by the system. This setting is optimum for all floor systems or old systems with large
pipes.
In addition to reduced power consumption, in floor systems all the circuits will be bal-
anced for the same head loss. The operating range is from min. (1) to max. (8).
- Setting Fixed max. speed
(fig. 22)
The circulating pump does not modulate its power, and will always run at max. speed.
The operating principle is that of conventional circulating pumps (with a reduction in pow-
er consumption compared to them).
Water system characteristics
In the presence of water harder than 25° Fr, it is advisable to use suitably treated water,
in order to avoid possible scaling in the boiler caused by hard water, or corrosion pro-
duced by aggressive water. Due to its low thermal conductivity, scaling even just a few
mm thick causes significant overheating of the generator walls, with consequent serious
problems.
Water treatment is indispensable in case of very large systems (containing large
amounts of water) or with frequent introduction of replenishing water in the system. If par-
tial or total emptying of the system becomes necessary in these cases, it is advisable to
refill with treated water.
Gas connection
The gas must be connected to the corresponding union with a rigid metal pipe.
The gas meter must be adequate for the simultaneous use of all units connected to it.
Carry out the generator gas connection in accordance with current regulations. The di-
ameter of the gas pipe leaving the generator does not determine the diameter of the pipe
between the unit and the meter; it must be chosen according to its length and pressure
loss.
B
Make sure to install a fuel shutoff valve externally with respect to the modules,
enabling the gas to be turned off even without opening the single modules
equipped with key closing.
Connection instructions
ENERGY TOP B
is equipped on the inside with 3 manifolds (gas, system delivery and
return) and a condensate drain pipe that facilitate cascade connection and also connec-
tion of a single module to the system. The manifolds are sized for a connection in series
of up to 1000 kW.
The cabinet contains a set of 3 seals (2 for water manifolds, 1 for gas manifold) with re-
spective bolts and nuts, to be used for connection to a subsequent module (connection
in cascade). The optional kit code 042027X0, containing 3 blind flanges and 3 drilled
flanges with respective seals and screws, is available on request for the connection to
the system.
To connect a single module
•
After establishing on which side of the module to make the water and gas connec-
tions, connect the flanges with the joining section contained in the kit on that side
after suitably welding them to the system pipes. Make sure to correctly fit the special
seals contained in the kit.
•
Connect a Ø40 pipe to the condensate drain pipe for removing the condensate pro-
duced during operation (see fig. 52).
•
Fit the blind flanges contained in the kit on the opposite side of the module, placing
the special seals in between.
fig. 23
1
Gas inlet
2
System delivery
3
System return
4
Condensate drain
5
Blind flanges - kit 042027X0 (optional)
7
Blind flanges - kit 042027X0 (optional)
To connect several modules in line
•
Connect the first module to the system and gas pipes, as described above, but with-
out fitting the blind flanges on the opposite side of the module to that of the connec-
tion.
•
Connect the second module on this side, making sure to align the connection flang-
es and the condensate drain pipe. Place the seals contained in the kit between the
flanges of the two modules.
•
Fit the bolts contained in the kit on the flanges from the inside of the first module,
making them come out of the flanges in the second module. Partially tighten the nuts
on the bolts from inside the second module.
•
Before tightening the nuts, make sure all the seals are correctly positioned and fit
the condensate drain pipes of the two modules (see fig. 53).
•
Tighten the nuts and repeat the connection operations for the following modules.
fig. 24
1
Gas inlet
2
System delivery
3
System return
4
Condensate drain
5
Blind flanges - kit 042027X0 (optional)
7
Blind flanges - kit 042027X0 (optional)
8
Seals and screws (standard)
Setting
Dp-v
Proportional head
fig. 20
Setting
Dp-c
Constant head
fig. 21
Setting
Fixed max. speed
fig. 22
1
4
8
8
5
2
ext. in
1
4
8
8
5
2
ext. in
1
4
8
8
5
2
ext. in
1
4
8
8
5
2
ext. in
1
4
8
8
5
2
ext. in
2
1
3
4
7
5
2
1
3
2
1
3
4
7
2
1
3
8
5
cod. 3541H060 - Rev. 02 - 04/2018