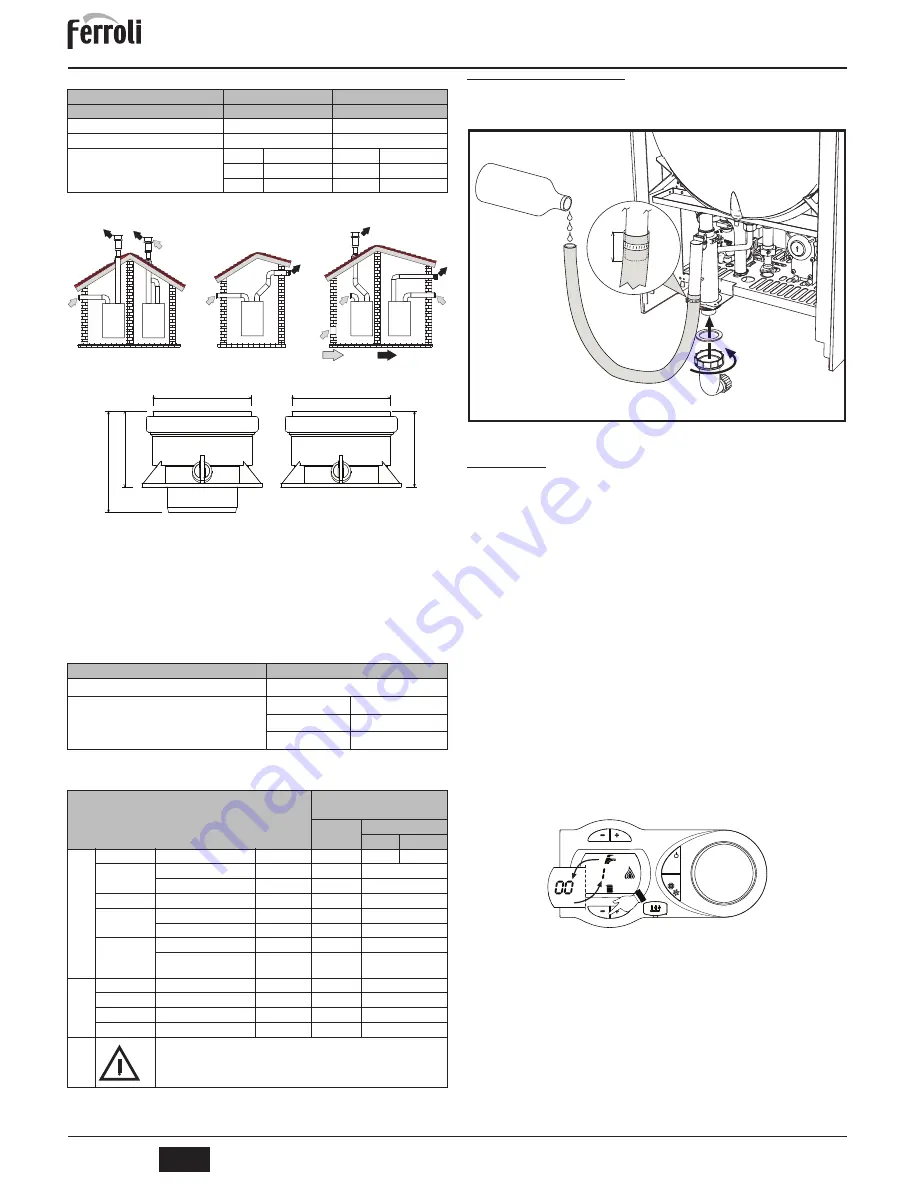
DOMIcondens F 24 D - F 28 D
34
EN
cod. 3541C751 - Rev. 00 - 10/2013
Table. 2 - Baffles for coaxial ducts
Connection with separate pipes
fig. 13 - Examples of connection with separate pipes (
= Air /
= Fumes)
For the connection of separate ducts, fit the unit with the following starting accessory:
fig. 14 - Starting accessory for separate ducts
Before proceeding with installation, check the baffle to be used and make sure the max-
imum permissible length has not been exceeded, by means of a simple calculation:
1.
Completely establish the layout of the system of split flues, including accessories
and outlet terminals.
2.
Consult the table 4 and identify the losses in m
eq
(equivalent metres) of every com-
ponent, according to the installation position.
3.
Check that the sum total of losses is less than or equal to the maximum permissible
length in table 3.
Table. 3 - Baffles for separate ducts
Table. 4 - Accessories
3.7 Condensate drain connection
The boiler has an internal trap for draining the condensate. Fit the inspection union
A
and
the flexible tube
B
, pressing it in for about 3 cm. Fill the trap with approx. 0.5 L of water
and connect the flexible tube to the drainage system.
fig. 15 - Condensate drain connection
4. SERVICE AND MAINTENANCE
4.1 Adjustments
Gas conversion
The unit can work on natural gas or LPG and is factory-set for use with one of these two
gases, as clearly shown on the packing and data plate. Whenever a different gas to that
for which the unit is arranged has to be used, the special conversion kit will be required,
proceeding as follows:
1.
Disconnect the power supply ahead of the boiler and close the gas cock;
2.
Replace the nozzles at the main burner and pilot burner, fitting the nozzles indicated
in the technical data table in cap. 5, depending on the type of gas used
3.
Connect the power supply ahead of the boiler and open the gas cock;
4.
Modify the parameter for the type of gas:
•
put the boiler in standby mode
•
press the DHW buttons details 1 and 2 - fig. 1 for 10 seconds: the display shows
“
b01
“ flashing.
•
press the DHW buttons details 1 and 2 - fig. 1) to set parameter
00
(for opera-
tion with natural gas) or
01
(for operation with LPG).
•
press the DHW buttons details 1 and 2 - fig. 1 for 10 seconds.
•
the boiler will return to standby mode
5.
Adjust the minimum and maximum pressures at the burner (ref. relevant para-
graph), setting the values given in the technical data table for the type of gas used
6.
Apply the sticker, contained in the conversion kit, near the data plate as proof of the
conversion.
TEST mode activation
Press the heating buttons (details 3 and 4 - fig. 1) together for 5 seconds to activate the
TEST
mode. The boiler lights at the maximum heating power set as described in the fol-
lowing section.
The heating and DHW symbols (fig. 16) flash on the display; the heating power will ap-
pear alongside.
fig. 16 - TEST mode (heating power = 100%)
Press the heating buttons (details 3 and 4 - fig. 1) to increase or decrease the power
(Min.=0%, Max.=100%).
By pressing the DHW
“-”
button (detail 1 - fig. 1), boiler output is immediately adjusted
to min. (0%). By pressing the DHW
“+”
button (detail 2 - fig. 1), boiler output is immedi-
ately adjusted to max. (100%).
If the TEST mode is activated and enough hot water is drawn to activate the DHW mode,
the boiler stays in the TEST mode but the circulating pump is deactivated.
To deactivate the TEST mode, press the heating buttons (details 3 and 4 - fig. 1) together
for 5 seconds.
The TEST mode is automatically deactivated in any case after 15 minutes or on stopping
of hot water drawing (if enough hot water has been drawn to activate the DHW mode).
Coaxial 60/100
Coaxial 80/125
Max. permissible length
6 m
12 m
Reduction factor 90° bend
1 m
0.5 m
Reduction factor 45° bend
0.5 m
0.25 m
Baffle to use
0 ÷ 2 m
Ø 45
0 ÷ 6 m
Ø 45
2 ÷ 4 m
Ø 50
6 ÷ 12 m
no baffle
4 ÷ 6 m
no baffle
Separate ducts
Max. permissible length
55 m
eq
Baffle to use
0 ÷ 15 m
eq
Ø 45
15 ÷ 35 m
eq
Ø 50
35 ÷ 55 m
eq
No baffle
Losses in m
eq
Air
inlet
Fume exhaust
Vertical
Horizontal
Ø 80
PIPE
1 m M/F
1KWMA83W
1.0
1.6
2.0
BEND
45° M/F
1KWMA65W
1.2
1.8
90° M/F
1KWMA01W
1,5
2.0
PIPE SECTION
with test point
1KWMA70W
0.3
0.3
TERMINAL
air, wall
1KWMA85A
2.0
-
fumes, wall with antiwind
1KWMA86A
-
5.0
FLUE
Split air/fumes 80/80
010027X0
-
12.0
Fume outlet only Ø80
01
1KWMA86U
-
4.0
Ø 60
PIPE
1 m M/F
1KWMA89W
6.0
BEND
90° M/F
1KWMA88W
4.5
REDUCTION
80/60
041050X0
5.0
TERMINAL
fumes, wall with antiwind
1KWMA90A
7.0
ATTENTION: CONSIDER THE HIGH PRESSURE LOSSES OF Ø60 ACCESSORIES;
USE THEM ONLY IF NECESSARY AND AT THE LAST FUME EXHAUST SECTION.
C
52
C
32
C
52
B
22
C
12
Ø 81
Ø 81
Ø
65
Ø
87
Ø
65
041039X0
0.5 l
A
B
3 cm
eco
comfort
reset
II
II
II
I I
I I I I I I
II
II
II
II
II
II
II
I I
I I I I I I
II
II
II
II