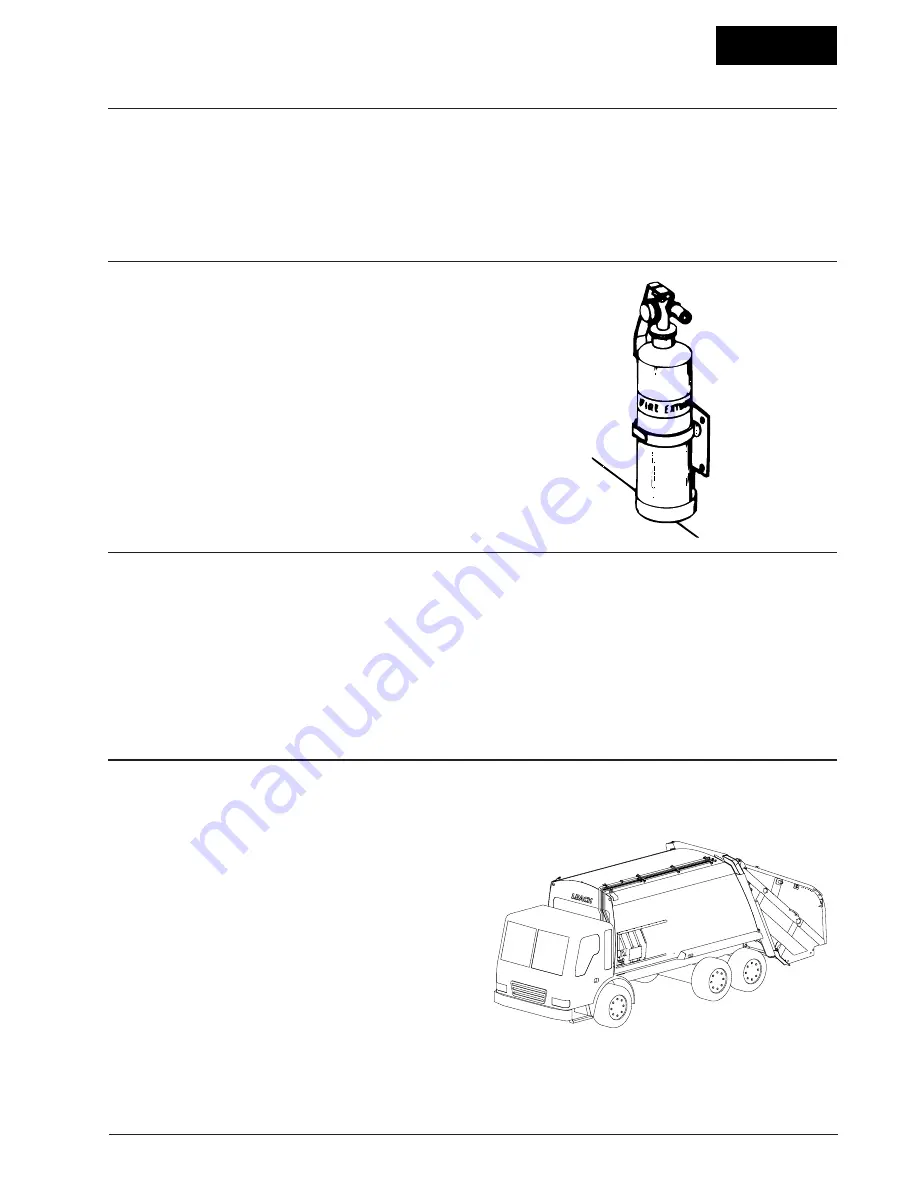
SECTION 1
SAFETY PRECAUTIONS
HYDRAULICS
Hydraulic fluid operates under high temperatures.
Avoid contact with piping, hoses or cylinders to pre-
vent burns.
Never use hands to check for leaks. Hydraulic fluid
escaping under pressure may cause injury.
1.
2.
In case of injury seek proper medical treatment im-
mediately.
3.
FIRE PROTECTION
Keep a fire extinguisher accessible at all times, as
recommended by the Bureau of Motor Carrier
Safety.
Never use lighted smoking materials, open flame
or sparks around when working with flammable
materials such as fuel tanks or storage batteries.
Never have an open flame as a light source.
Never load ashes or other materials which might
be smoldering. These materials could ignite refuse
in the packer body.
1.
2.
3.
4.
HOUSEKEEPING
Good housekeeping habits are a major factor in acci-
dent prevention.
Keep handrails and steps clean and free of grease
or debris.
Do not store brooms or other equipment where they
could inadvertently activate the packer controls.
1.
2.
Rubbish, scrap paper and litter are highly combus-
tible. Such material should be stored in metal con-
tainers entirely clear of sparks and flames.
3.
SHUTDOWN
Put all controls in neutral.
Set parking brake.
Disengage PTO.
Shut off engine.
Shut off solenoid dashboard switch.
Remove key.
Lock vehicle.
1.
2.
3.
4.
5.
6.
7.
1-5
Содержание LEACH 2R-III
Страница 2: ......
Страница 8: ......
Страница 15: ...SAFETY PRECAUTIONS DECAL PLACEMENT SECTION 1 2 1 3 4 5 1 2 3 4 5 CART TIPPER CONTROL DOWN UP DOWN UP 1 7 ...
Страница 26: ...SECTION 2 2 8 ...
Страница 28: ...OPERATION SECTION 3 LOCATION OF OPERATING CONTROLS 3 2 4 6 5 7 8 1 2 3 8 9 10 11 12 7 ...
Страница 46: ...SECTION 3 3 20 ...
Страница 54: ...SECTION 4 4 8 ...
Страница 60: ...SECTION 6 6 4 PREVENTIVE MAINTENANCE 1 2 3 4 5 6 7 8 ...
Страница 62: ...SECTION 6 6 6 ...
Страница 76: ...SECTION 7 7 10 ...