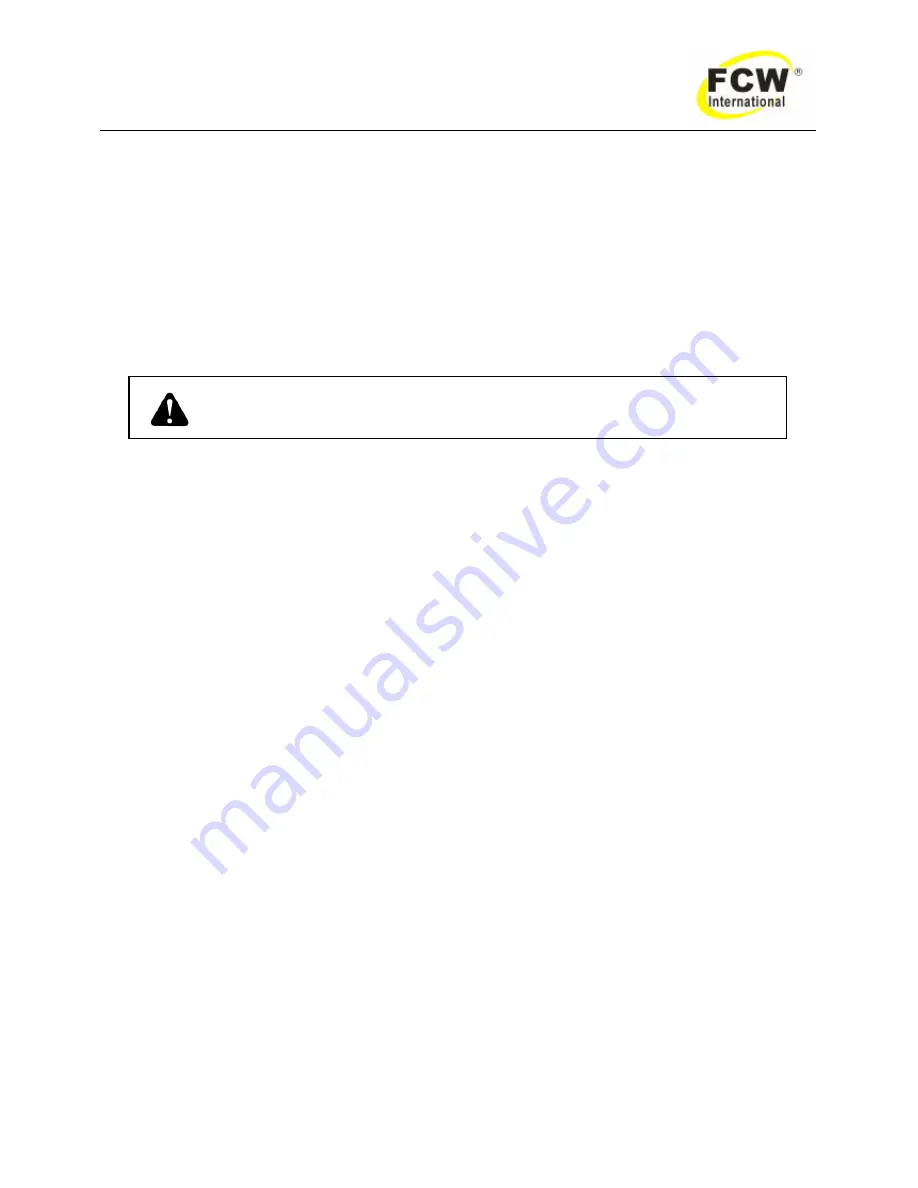
- 21 -
DYNA POWER 350CV
、
503CV
、
500CV
、
630CV
、
630HCV Operating Manual
l
Welding dirty, oily, painted oxidized or greasy plate.
Clean contaminates off plate.
l
Distance between the MIG gun
Keep the distance between the MIG gun nozzle and the work piece to a minimum. Refer to distance
from the MIG gun nozzle to the work piece in 5.03.
l
Maintain the MIG gun in good work order
Ensure that the gas holes are not blocked and gas is exiting out of the gun nozzle. Refer to the
WARNING.
Do not restrict gas flow by allowing spatter to build up inside the MIG gun nozzle.
Check that the MIG gun O-rings are not damaged.
WARNING:
Disengage the drive roll when testing for gas flow by ear.
b) Inconsistent wire feed
Wire feeding problems can be reduced by checking the following points:
l
Wire spool brake is too tight
Feed roller driven by motor in the cabinet will slip.
l
Wire spool brake is too loose
Wire spool can unwind and tangle.
l
Worn or incorrect feed roller size
Use “U” groove drive feeder roller matched to the aluminum wire size you are welding.
Use “V’
” groove drive feeder roller matched to the steel wire size you are welding.
Use “knurled V”’
groove drive feeder roller matched to the flux cored wire size you are welding.
l
Mis-alignment of inlet/ outlet guides
Wire will rub against the mis-aligned guides and reduces wire feed ability.
l
Liner blocked with debris
Debris is produced by the wire passing through the feed roller, if excessive pressure is applied to
the pressure roller adjuster.
Debris can also be produced by the wire passing through an incorrect feed roller groove shape or
size.
Debris is fed into the liner where it accumulates thus reducing wire feed ability.
l
Incorrect or worn contact tip
The contact tip transfers the weld current to the electrode wire. If the hole in the contact tip is too
large then arcing may occur inside the contact tip resulting in the electrode wire jamming in the
contact tip.
When using soft electrode wire such as aluminum it may become jammed in the contact tip due to
expansion of the wire when heated. A contact tip designed for soft electrode wires should be used.
l
Poor work lead contact to work piece
If the work lead has a poor electrical contact to the work piece then the connection point will heat up
and result in a reduction of power at the arc.
l
Bent liner
This will cause friction between the wire and the liner thus reducing wire feed ability.