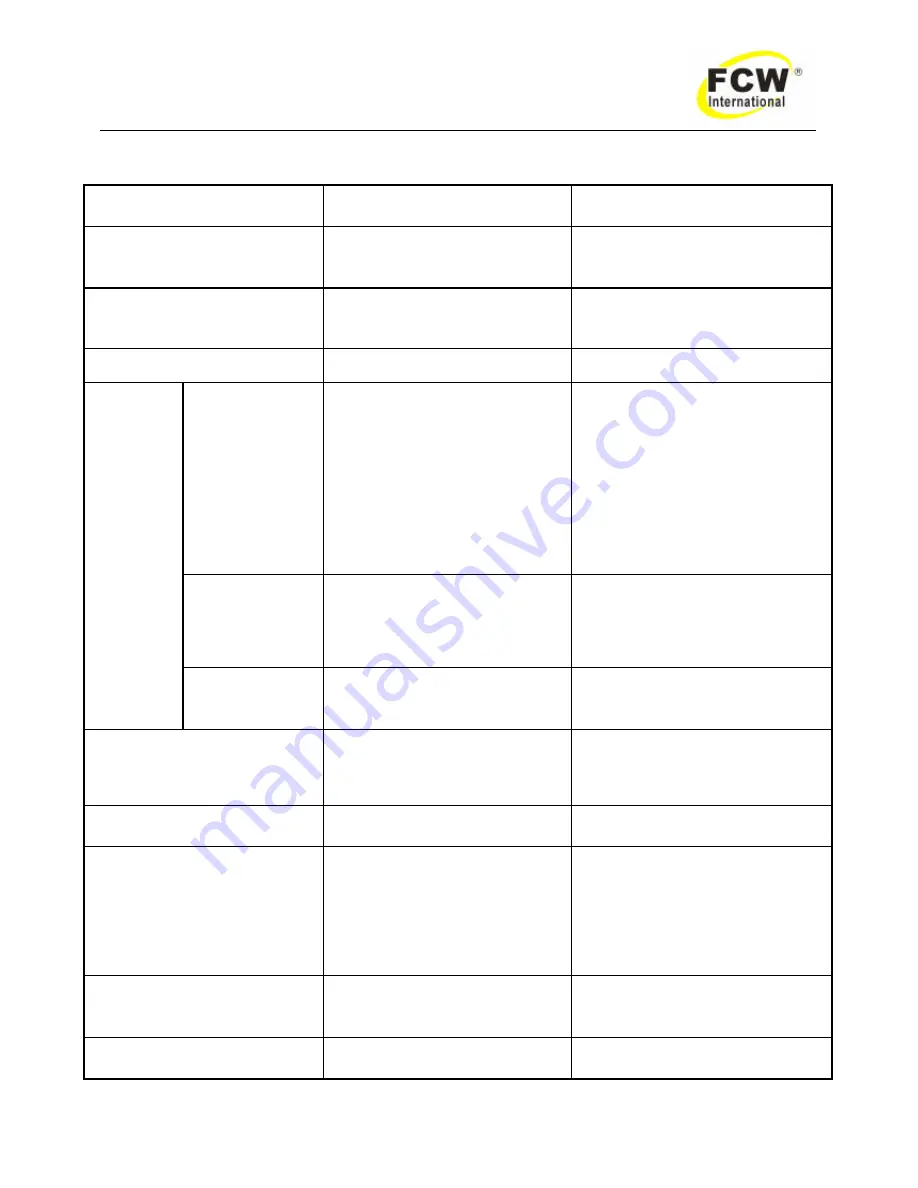
- 19 -
DYNA POWER 350CV
、
503CV
、
500CV
、
630CV
、
630HCV Operating Manual
Troubleshooting Guide
Fault
Cause
Remedy
1. The AC power indicator light is
not lit and welding arc can not
be established.
1. No power input or main power
switches damage.
2. Indicator damage.
1. Check input power or replace
main power switch.
2. Replace indicator light.
2. The AC power indicator light on
and welding arc can not be
established.
1. Input voltage unstable.
2. Diode damage.
1. Connect stabilizer or reset power
switch.
2. Replace diode.
3. The warning indicator light on.
Over load.
Reduce current or wait moment.
a. No gas flow
No wire feed
No output
1. MIG torch plug is not insert into
the socket or the connect is
bad.
2. MIG torch damage (diagnose
method: make the welding
machine control socket two
pins short circuit, the faulty
disappear).
3. Wire feeder plug is not insert
into the socket or the connect
condition is bad.
1. Insert the plug correctly, and
rotate it clockwise.
2. Repair or replace MIG torch.
3. Insert the plug correctly, and
rotate it clockwise.
b. No gas flow
Have wire feed
Have output
1. The gas line is not turn on.
2. The MIG torch damage.
3. The solenoid damage.
4. Wire speed Control board
damage.
1. Turn on the gas system.
2. Repair or replace.
3. Repair or replace.
4. Repair or replace.
4. Turn on
torch
control
switch
c. Have gas flow
Have wire feed
No output
1. Disconnect the work piece to
the work ground cable.
2. Main Board damage.
1. Reconnect the ground cable and
tighten the work piece.
2. Repair or replace.
5. Faulty welding arc control.
1. The MIG torch damage.
2. Faulty setting.
3. Main board damage.
1. Repair or replace the MIG torch.
2. Read this manual carefully and
set up correctly.
3. Repair or replace.
6. The arc weld has no output.
1. Transformer bad connect.
2. AC contactor bad connect.
1. Repair or replace.
2. Repair or replace.
7. Arc start difficult or often break
off.
1. The power supply voltage is too
low or the cable is too thin.
2. Main board damage.
3. The contact tip damage.
4. The work piece bad connect.
5. The wire roller damage.
6. The torch lead damage.
1. Connect a stabilizer or increase
the thickness of the power cable.
2. Repair or replace.
3. Repair or replace.
4. Repair or replace.
5. Replace
6. Replace
8. The maximum output welding
current can not achieved in the
rated input voltage.
Main board damage.
Repair or replace.
9. The current decrease in the
weld process.
Faulty cable connected to work
piece.
Make sure the cable positive connect
to the work piece correctly.