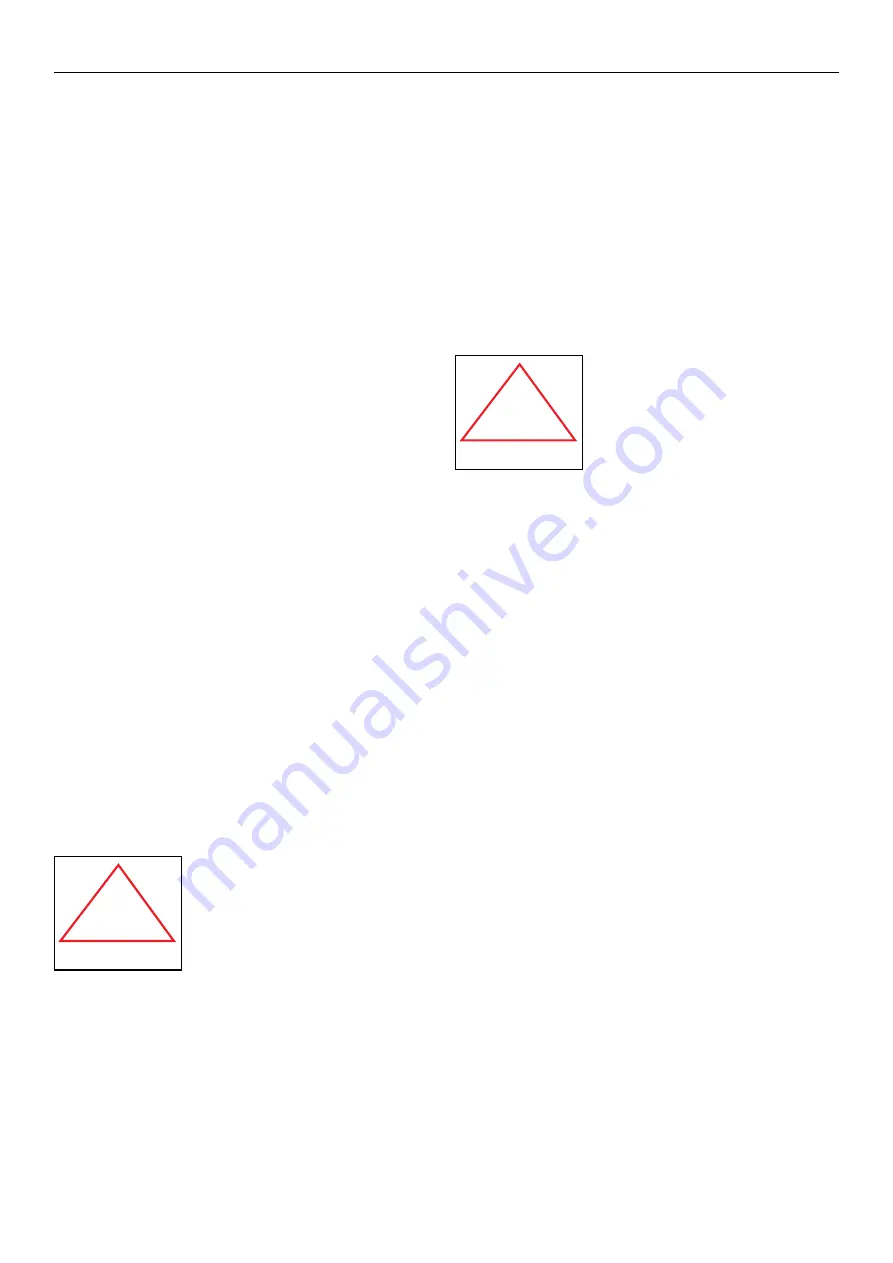
CR40
8
TRANSPORT
• Before driving with the machine, ensure the safe
mounting of the machine. Make sure that the
journals are seating correctly and that the pins are
tight. Check the tension of the lower link stabilizers.
• Before driving with the machine, make sure that
the required lamps and reflectors as well as the
slow moving vehicle sign are attached correctly.
Moreover, the lamps should be checked for correct
functioning.
• Before driving with the attached machine, make
sure that the hydraulic unit of the machine is dep-
ressurized (unless otherwise instructed in the ope-
rating instructions).
• When driving on public roads, always observe the
valid traffic regulations. The travel speed must be
adapted to the specific conditions.
• When driving, please take into consideration the
additional mass resulting from the machine’s
weight. It may affect the reactions, the steerability
and the braking function of the tractor.
• Please note that the machine rear sways when tur-
ning.
• Pay attention to the machine’s height near bridges
or other height restricting objects.
• When backing off, the machine may obstruct the
rear view. Exercise extreme caution. If necessary,
ask a flagman to help you; he can indicate the
required distances.
• It is prohibited for other people to ride on the ma-
chine.
OPERATION
Many occupational accidents
take place in abnormal
circumstances. Therefore it is im-
portant to take into account all
the possible circumstances that
may arise during operation of
the machine.
• Depending on the machine’s type, it will have
diverse safety devices and protectors. These are
meant to protect the machine and its operator,
and they must never be removed or altered. Never
start up or use the machine without all the safety
devices and protectors in place. Also check the uni-
versal joint’s safety equipment and joins.
• Never insert any body part into the machine with
the engine running.
• If any faults arise that may jeopardize occupational
safety, turn off the machine.
• During operation, the machine’s operator is res-
ponsible for safety in the whole work area. Work
may not be carried out in the presence of any fac-
tors that jeopardize occupational safety.
• Exercise extreme caution when hitching / unhit-
ching the machine from a tractor/trailer.
The machine’s operator must
have constant, unobstructed
visibility of the work area. If this
is not possible, the operator must
work with an assistant.
• Look out for moving parts when the machine is in
operation.
• Secure the machine against unauthorized and
accidental operation (e.g. moving when parked)
whenever it is left unattended.
• Never leave the machine running unattended.
• Avoid causing fast, stroke-like loading.
• Never exceed the given operating values.
• All safety and warning signs on and in the machine
must be legible and intact.
• The machine may not be operated by persons who
are unwell or under the influence of drugs or alco-
hol.
MAINTENANCE
• The machine may only be serviced and repaired by
professionals.
• Electrical and hydraulic faults may only be repaired
by authorized professionals.
• In cases requiring welding, contact the manufac-
turer.
• Turn off the tractor engine and disconnect the uni-
versal joint before beginning service or maintenan-
ce actions.
• Before any maintenance work, turn the main power
switch of the tractor to OFF.
• Ensure that there is no pressure in the hydraulic
system.
• Take out the key from the tractor’s ignition for the
duration of the servicing or maintenance. Check
that the power is off from the machine you are
working on.
!
DANGER!
CAUTION!
!
Содержание CR40
Страница 2: ......
Страница 29: ...CR40 29 ...
Страница 34: ...CR40 34 200002521 LIFTING BOOM ...
Страница 38: ...CR40 38 1 10 9 8 7 6 5 4 3 2 11 16 15 14 13 12 15 13 200001719 ROTATOR CR300 W25A25 ...
Страница 43: ...CR40 43 ...
Страница 46: ...CR40 46 1 10 9 8 7 6 5 4 3 2 11 17 16 15 14 13 12 4 6 13 200001965 HYDRAULIC SUPPORT LEGS 3 POINT LINKAGE ...
Страница 48: ...CR40 48 ...
Страница 51: ......