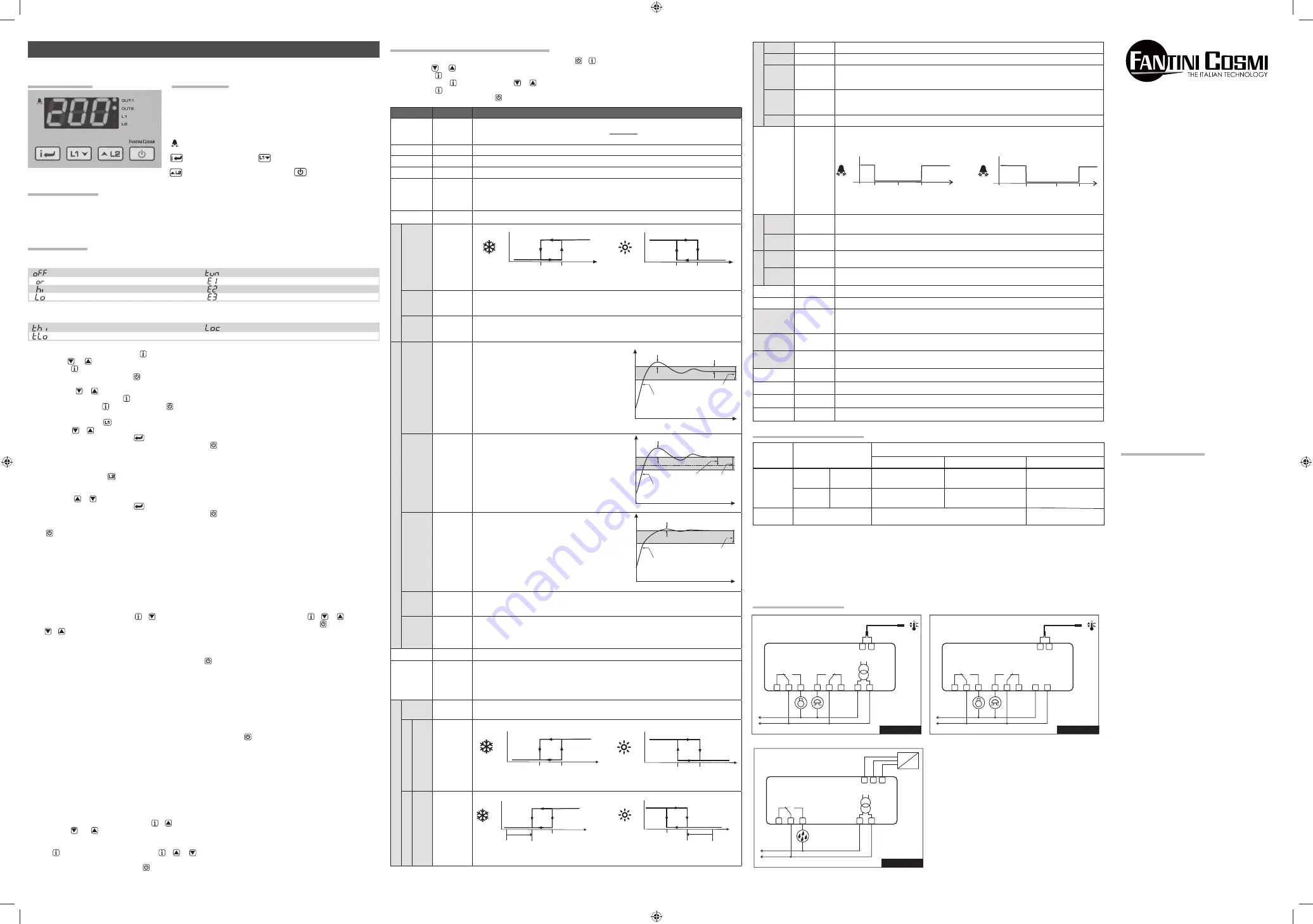
CONFIGURATION PARAMETERS
T
o get access to the parameter configuration menu, press button
■
+
for 5 seconds.
With button
■
or
select the parameter to be modified.
Press button
■
to display the value.
By keeping button
■
pressed, use button
or
to set the desired value.
When button
■
is released, the newly programmed value is stored and the following parameter is displayed.
T
o exit from the setup, press button
■
or wait for 30 seconds.
PAR
RANGE
DESCRIPTION
SCL
1°C;
2°C;
°F
Readout scale (see table of input specifications)
Caution: upon changing the SCL value, it is then absolutely necessary to
reconfigure
the param-
eters relevant to the absolute and relative temperatures (SPL, SPH, 1SP, 1HY etc..)
SPL
-50°...SPH
Minimum limit for
1SP
setting
SPH
SPL...150° Maximum limit for
1SP
setting.
1SP
SPL... SPH Setpoint (value to be maintained in the room).
1CM
H
Y; PID
Control mode.
With
1CM
=H
Y
you select control with hysteresis: parameters
1HY
,
1T0 and 1T1
are used.
With
1CM
=PID you select a Proportional-Integral-Derivative control mode: parameters
1PB
,
1IT
,
1DT
,
1AR
,
1CT
will be used
1CH
REF; HEA
Refrigerating (REF) or Heating (HEA) control mode.
1CM
=HY
1HY
0...19.9°
OFF/ON thermostat di
f
ferential.
With
1HY
=0 the output is always o
ff.
1T0
0...30min
Minimum o
f
f time.
After
output
1 has
been
turned
of
f,
it
remains
inactive
for 1T0
minutes
regardless of the
temperature value measured.
1T1
0...30min
Minimum on time. (
the following parameter will be 1PF
).
After
output
1 has
been
turned
on,
it
remains
active
for 1T1
minutes
regardless of the
temperature
value measured.
1CM
=PID
1PB
0...19.9°
Proportional bandwidth.
T
emperature
control
takes
place
by
changing
the
ON
time
of the
output:
the closer the
temperature
to the
setpoint,
the less
time
of
activation.
A
small
proportional
band
increases
the promptness of
response of the
system
to
temperature
variations,
but
tends to
make
it
less
stable.
A
purely
proportional
control
stabilises
the
temperature
within
the
proportional
band
but
does not cancel
the deviation from setpoint.
With
1PB
=0 the output is always o
ff.
1IT
0...999s
Integral action time.
The
steady-state
error
is
cancelled
by
inserting
an
integral
action.
The
integral
action
time,
determines
the speed
with
which
the
steady-state
temperature
is
achieved,
but
a
high
speed
(
1IT
low)
may
be
the
cause
of
overshoot
and
instability
in
the response.
With
1IT
=0 the integral control is disabled.
1DT
0...999s
Derivative action time.
Response
overshoot
may
be
reduced
by
inserting
a
derivative
Action.
A
high
derivative
action
(
1DT
high)
makes
the
system
very
sensitive
to small
temperature
variation
s and
causes
instability
.
With
1DT
=0 the derivative control is disabled.
1AR
0...100%
Reset of integral action time referred to
1PB
Decreasing
the parameter 1AR
reduces
the
integral
control
action
zone,
and
consequently
the
overshoot (see figure on paragraph
1IT
).
1CT
1...255s
Cycle time.
It’s the
period
in
which
the
output
ON
time
changes. The
quicker
the
system
to
be
controlled
reacts to
temperature
variations,
the smaller the
cycle
time
must
be,
in
order to
obtain
higher
temperature stability and less sensitivity to load variations.
1PF
ON/OFF
Output state in case of probe failure.
OAU
NON;
THR;
AL0;
AL1
AUX output operation.
NON : output disabled (always o
f
f). (
the next parameter will be ATM
)
THR: output programmed for second thermostat control (
the next parameter will be 2SM
).
AL0: contacts open when an alarm condition occurs (
the next parameter will be ATM
).
AL1: contacts make when an alarm condition occurs (
the next parameter will be ATM
).
OAU
=THR
2SM
ABS;
REL
Setpoint 2 mode.
Channel 2 set
poin
t ma
y be
ab
s
olu
te
(
2SM
=ABS),
or a
di
fferent
ial
relat
iv
e to set
poin
t 1
(
2SM=RE
L)
2SM
=ABS
2SP
SPL...SPH Auxiliary output switchover temperature (
the next parameter will be 2CH
)
2SM
=REL
2DF
-19.9...19.9°
T
emperature di
f
ferential relative to
1SP.
The auxiliary output setpoint is equal to
1SP+2DF
ON/OFF refrigerating control
(
1CM
=H
Y
,
1CH
=REF)
ON/OFF heating control
(
1CM
=H
Y
,
1CH
=HEA)
1SP
1SP+1HY
T[°]
ON
OFF
1SP
1SP-1HY
T[°]
ON
OFF
Time
T
emperature
Process
temperature
Overshoot
Steady-state error
1PB
1SP
Time
T
emperature
Process
temperature
Overshoot
1PB
1PBx1AR%
integral control
action area
1SP
Time
T
emperature
Process
temperature
Overshoot
1PB
1SP
2SP
2SP+2HY T[°]
ON
OFF
2SP
2SP-2HY
T[°]
ON
OFF
ON/OFF control in refrigeration
(
2SM
=ABS,
2CH
=REF)
ON/OFF control in heating
(
2SM
=ABS,
2CH
=HEA)
1SP+2DF
1SP
2DF>0
1SP+2DF+2HY
T[°]
ON
OFF
1SP
1SP+2DF
2DF<0
1SP+2DF-2HY
T[°]
ON
OFF
ON/OFF control in refrigeration. Setpoint 2
relative to setpoint 1 (
OAU
=THR,
2CH
=REF)
ON/OFF control in heating. Setpoint 2
relative to setpoint 1 (
OAU
=THR,
2CH
=HEA)
TECHNICAL DATA
Power supply
L03BI-
12V
ac/dc ±10%, 3W
L03BM-
230
V
ac±10%, 50/60Hz, 3W
Relay outputs (L03B---)
OUT1
16(4)A 240Vac
OUT2
16(4)A 240Vac
Inputs
see table of input specifications
Measurement range
see table of input specifications
Measurement accuracy
see table of input specifications
Operating conditions
-10 … +50°C; 15%...80%
r
.H.
CE (Reference Norms)
EN60730-1; EN60730-2-9;
EN55022 (Class B); EN50082-1
Front protection
IP40
OAU
=THR
2CH
REF; HEA
Refrigerating control (REF) or heating control mode (HEA) for the auxiliary output.
2HY
0...19.9°
Di
f
ferential of thermostat 2. With
2HY
=0 the auxiliary output always remains o
ff.
2T0
0...30min
Minimum o
f
f time.
After
output
2 has
been
turned
of
f,
it
remains
inactive
for 2T0
minutes
regardless of the
temperature
value measured.
2T1
0...30min
Minimum on time.
After
output
2 has
been
turned
on,
it
remains
active
for 2T1
minutes
regardless of the
temperature
value measured.
2PF
ON/OFF
Auxiliary output state in case of probe failure.
ATM
NON;
ABS;
REL
A
larm threshold management.
NON
:
all temperat
ure
alarms are
inhibi
ted
(
the following parameter will be SB
)
.
ABS: t
he
value
s programmed
in
ALA and AHA represent the real alarm thresholds.
RE
L: t
he
value
s programmed
in
ALR and AHR are alarm
di
fferent
ial
s referred to 1SP and 1SP+1HY.
A
TM
=ABS
ALA
-50°...AHA Low temperature alarm threshold.
AHA
ALA...150° High temperature alarm threshold.
A
TM
=REL
ALR
-12.0...0°
Low temperature alarm di
f
ferential.
With
ALR
=0 the low temperature alarm is excluded
AHR
0...12.0°
High temperature alarm di
f
ferential.
With
AHR
=0 the high temperature alarm is excluded
ATD
0...120min
Delay before alarm temperature warning.
SB
NO/YES
Stand-by button enabling.
INP
0mA/4mA,
T1/T2
ST1/SN4
Sensor input selection (see table of input specifications).
Warning: “0mA/4mA”, “T1” and “T2” are not available
RLO
-19.9...RHI Minimum range value
RLO
takes the minimum value measured by the transmitter (i.e. the value matching 0V, 0/4mA).
RHI
RLO...99.9 Maximum range value
RHI
takes the maximum value measured by the transmitter (i.e. the value matching 1V, 20mA)
OS1
-12.5...12.5°
Probe
T1 offset.
TLD
1...30min
Delay for minimum temperature (TLO) and maximum temperature (THI) logging.
SIM
0...100
Display slowdown
ADR
1...255
address for PC communication (not available)
INPUT SPECIFICATIONS
WIRING DIAGRAMS
1SP
1SP-ALR
T[°]
ON
OFF
1SP+1HY+AHR
1SP
1SP-1HY-ALR
1SP+AHR
T[°]
ON
OFF
T
emperature alarm with relative thresholds,
refrigerating control (
ATM
=REL,
1CH
=REF)
T
emperature alarm with relative thresholds,
heating control (
ATM
=REL,
1CH
=HEA).
L03BM--
11
12
230V~
OUT2
18
17
16
OUT1
21
20
19
2
3
16(4)A
16(4)A
DISPLAY
During normal operation, the display shows either the temperature measured or one of the following indications:
Controller in stand-by
Controller in autotuning
Probe
T1 overrange or failure
In tuning: timeout1 error
Room high temperature alarm
In tuning: timeout2 error
Room low temperature alarm
In tuning: overrange error
MENU INFO
The information available in this menu is:
Maximum temperature recorded
Keypad state lock
Minimum temperature recorded
Access to menu and information displayed.
Press and immediately release button
■
.
With button
■
or
select the data to be displayed.
Press button
■
to display value.
T
o exit from the menu, press button
■
or wait for 10 seconds.
Reset of THI, TLO recordings
With button
■
or
select the data to be reset.
Display the value with button
■
.
While keeping button
■
pressed, use button
.
CHANNEL 1 SETPOINT
(display and modification of desired temperature value)
Press and release
bu
tton
■
: t
he
L
ED
L1
blinks, t
he
di
spla
y show
s 1
S
P for 1 second and then the set
poin
t assoc
ia
ted
value
.
Press
bu
ttons
■
or
to set the
desired
value
(adjus
tment
is
wi
t
hin
the
minimum
SPL and
maximum
SPH
limi
t
)
.
T
o store the new value press button
■
, or wait for 10 seconds.
T
o go back to normal mode without saving the new value, press
■
.
CHANNEL 2 SETPOINT
With
the
auxiliary
output
set as thermostat control
(
■
OAU
=THR),
it
’s
possible
to
modify
setpoint
2
during
the normal
operation
of the controller.
Press and release
button
■
:
the
LED
L2
blinks,
the
display
shows
2S
P for 1 second
if
setpoint
2
is
an
absolute
threshold
(
2SM
=ABS),
alternatively
the
display
shows
2DF
,
if
setpoint
2
is
a threshold
relative
to
setpoint
1
(
2SM
=REL),
then the
value
associated to the parameter appears.
Press buttons
■
or
to set the desired value.
T
o store the new value press button
■
or wait for 10 seconds.
T
o go back to normal mode without saving the new value, press
■
.
STAND-BY
B
u
tton
, when
pressed for
3
second
s, allow
s the controller to
be
pu
t on a st
andby
or
ou
t
pu
t control to
be
resumed
(wi
th SB
=YES
onl
y)
.
KEYPAD LOCK
The
keypad
lock
avoids
undesired,
potentially
dangerous
operations,
which
might
be
attempted
when
the controllers
is
operating
in
a
public
place. In the INFO
menu,
set parameter LOC
=YES
to
inhibit
all
functions
of the
buttons.
To
resume
normal
operation
of keypad, adjust setting so that
LOC=NO.
CONTROLLER AUTOTUNING IN PID MODE
Before starting
In the
setup
mode
(see
configuration
parameters):
set 1CM=PID;
make
sure
that 1CH matches the
desired
operation
mode
(
1CH
=REF for refrigerating control,
1CH
=HEA for heating control); then adjust setpoint
1SP
at the desired value.
Start autotuning
During
normal
operation,
keep
buttons
+
pressed for
3
seconds. 1CT
blinks
on the
display
.
With
+
or
set the
cycle
time
in
order to
define
the
dynamic
of the process to
be
controlled. To
abort
the
autotuning
function,
press
; to start
autotuning
press
+
or wait for 30 seconds.
During autotuning
During
the
entire
autotuning
phase,
the
display
alternates
TUN
with
the
actual
temperature
measured.
In case of
power
failure,
when
power
is
resumed,
after the
initial
autotest
phase,
the controller
resumes
the
autotuning
function.
To
abort
the
autotuning,
without
modifying
the
previous
control
parameters,
keep
button
pressed for
3
seconds.
After
the
autotuning
has
taken
place
successfully, the controller updates the control parameters and start to control.
Errors
If the autotuning function failed, the display shows an error code:
E1
timeout1
error:
the controller
could
not
bring
the
temperature
within
the
proportional
band.
Increase
■
1SP
in
case of
heating
control, vice versa, decrease
1SP
in case of refrigerating control and re-start the process.
E2
timeout2
error:
the
autotuning
has not ended
within
the
maximum
time
allowed
(1000
cycle
times).
Re-start the
autotuning
■
process and set a longer cycle time
1CT.
E3
temperature
overrange:
check
that the error
was
not
caused
by
a
probe
malfunction,
then decrease
■
1SP
in
case of
heating
control, vice versa increase
1SP
in case of refrigerating control and then re-start the process.
T
o eliminate the error indication and return to the normal mode, press button
■
.
Control improvement
T
o reduce overshoot, reduce the integral action reset
■
1AR
To
increase
the response speed of the
sys
tem
, reduce
the proport
ional
band
■
1PB.
Cau
t
ion: doing
t
his
makes
the
sys
tem less st
able
.
To
reduce
swings
in
steady-state
temperature,
increase
the
integral
action
time
■
1IT;
system
stability
is
thus
increased,
although
its response speed is decreased.
To
increase
the speed of response to the
variations
in
temperature,
increase
the
derivative
action
time
■
1DT.
Caution:
a
high
value makes the system sensitive to small variations and it may be a source of instability
.
RECALIBRATION
Have a precision reference thermometer or a calibrator to hand. Ensure that
■
OS1
=0 and
SIM
=0.
Switch the controller o
f
f then on again.
■
During the auto-test phase, press buttons
■
+
and keep them pressed till the controller shows
0AD.
With
buttons
■
and
select 0AD or SAD
:
0AD
allows
a
calibration
of
0,
inserting
a constant
correction
over
the
whole
scale
of
measurement.
SAD
allows
a
calibration
of the top part of the
measurement
scale
with
a
proportional
correction
between
the
calibration point and 0.
Press
■
to
display
the
value
and then
use
+
or
to
make
the read
value
coincide
with
the
value
measured
by
the
reference instrument.
Exit from calibration by pressing button
■
.
OPERATION
The
L03B--
controller
,
size
71x98x61
mm
(WxHxD),
is
to
be
secured
to a DIN
rail
in
such
a
position
as to
ensure
that no
liquid
■
infiltrates causing serious damage and compromising safety
;
Make
sure
that
electrical
connections
comply
with
the paragraph
“wiring
diagrams”.
To
reduce
the effects of
electromagnetic
■
disturbance, keep the sensor and signal cables well separate from the power wires.
Place the probe
T1 inside the room in a point that truly represents the temperature of the stored product.
■
INSTALLATION
OUT1
OUT2
L1
L2
Channel 1 output
Channel 2 output
Alarm
Channel 1 setpoint modification
Channel 2 setpoint modification
Fig.1 - Front panel
Thank you for having chosen a Fantini Cosmi product. Before installing the instrument, please read these instructions carefully
to ensure maximum performance and safety.
DESCRIPTION
INDICATION
L03B--/L23EM1A INSTRUCTION FOR USE
Info / Enter button
Modify Setpoint 1 / Decrease button
Increase / Modify Setpoint 2 button
Exit / Stand-by button
MODEL
INPUT
RANGE [MEASUREMENT ACCURACY]
SCL=1°C
SCL=2°C
SCL=°F
L03B--
INP=ST1
PTC 1000 Ω
(LS120)
-40/-19.9 ÷ 99.9/105°C
[<±
0
.
3
°
C(-40÷130
°
),±
1°C]
-40 ÷ 105°C
[<±0.3°C
(-40÷130°),±1°C]
-40 ÷ 221°F
[<±0.6°F
(-40÷221°),±2°F]
INP=SN4
NTC 10K Ω
(LS130)
-40/-19.9 ÷ 99.9/105°C
[<±
0
.
3
°
C(-40÷100
°
), ±
1°C]
-40 ÷ 105°C
[<±0.3°C
(-40÷100°),±1°C]
-40 ÷ 221°F
[<±0.6°F
(-40÷210°),±2°F]
Via Dell’Osio 6
20090 Caleppio di Settala MI ITALIA
Phone no. +39 02 95682.222
Fax no. +39 02 95307006
Web: www.fantinicosmi.it
e-mail: [email protected]
AC1-5
L03BI--
11
12
12Vac/dc
OUT2
18
17
16
OUT1
21
20
19
2
3
16(4)A
16(4)A
L23EM1A
12
11
230V~
OUT1
21
20
19
rH
V
2
3
4
V
IN
V+
V-
16(4)A
L23EM1A
0÷1V (LS160A)
RLO÷RHI [< ± 3mV]
-----