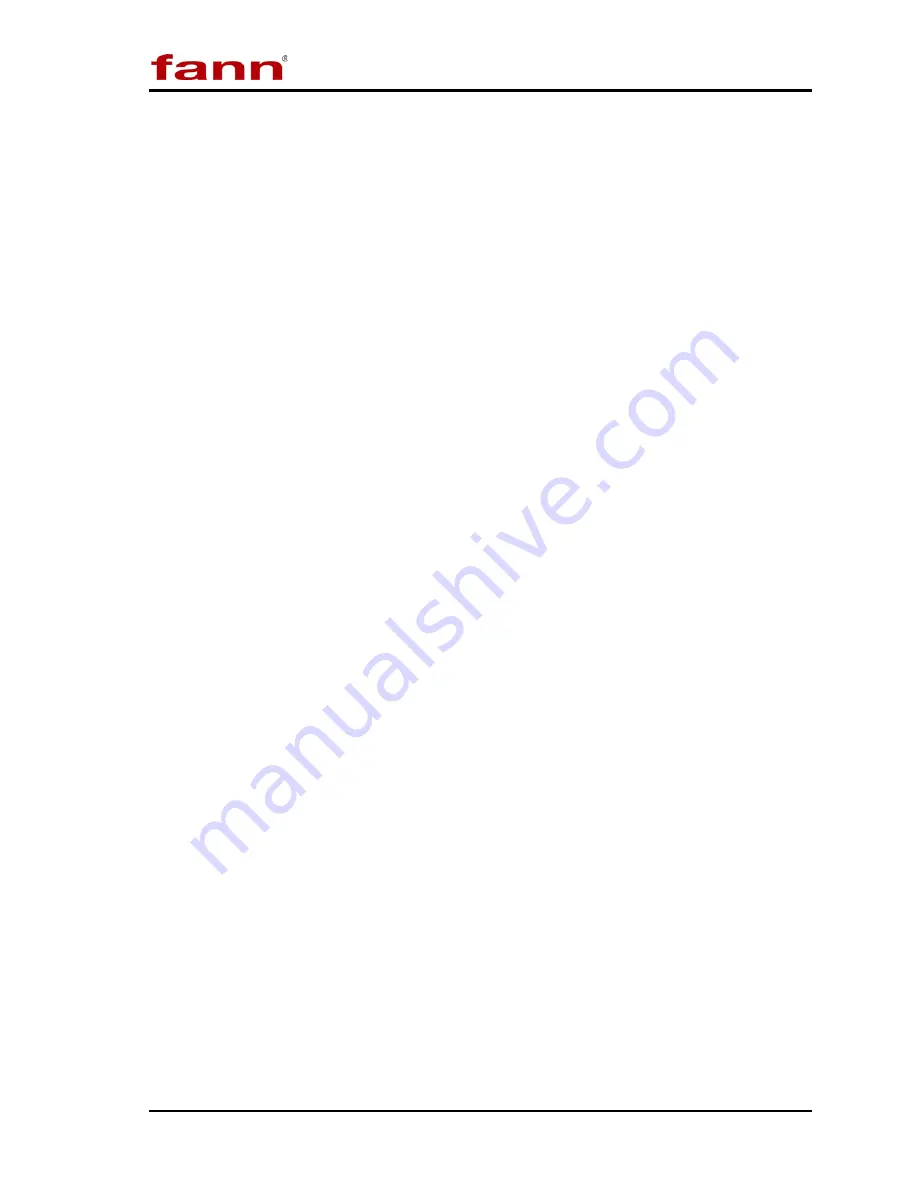
Model 640 & 640CC Instruction Manual
D01206676
Revision A February 2016
33
pressing the slug out, be careful not to damage the paddle shaft point or the
paddle itself. If the slug is not pressed out straight, it may cause the cup sleeve
to become oval and prevent the threaded closures from threading into the
sleeve.
3.
Periodically disassembly the diaphragm hub and clean any cement from the
Teflon o-rings. Replace the o-rings if they are badly worn.
4.
Check the rubber diaphragm for signs of brittleness or cracking. Replace if
necessary.
5.
Check the point on the bottom of the paddle shaft. Replace it if it is worn to
the point that the paddle rubs on the bottom of the slurry cup. Check to see
that the paddle shaft is not excessively worn where the shaft extends through
the diaphragm hub. Replace if wear is excessive.
6.
Check the slurry cup seal plug for wear. Replace it if it is worn to the point that
the paddle rubs on the bottom of the slurry cup.
Changing the Metal O-ring on the Cylinder Assembly
12.4
Pry the old o-ring out using a plastic or soft metal tool so as not to damage the
sealing surfaces.
1.
Coat the new o-ring with a light coating of grease.
2.
Press the new o-ring into the seal groove using your fingers. Do not bend or
scratch the new o-ring.
3.
Place the plug in the pressure vessel and thread in place until the seal shaft
contacts the new o-ring.
4.
Using a rubber mallet or dead blow hammer and light blows, begin to close the
plug and compress the o-ring. After three hits with the hammer, unscrew the
plug part way. Repeat this process until the scribe lines on the plug and
cylinder are lined up. Installation is now complete.
5.
Realignment of the witness marks on the plug and cylinder is recommended
each time the seats are lapped or if pressure leakage persists. In time, plug and
cylinder threads wear and heat-induced flexing of the plug and cylinder require
witness mark realignment because the marks no longer represent the actual
seating of the seal shaft.
Changing/Cleaning the High Pressure Filter Element
12.5
1.
Disconnect the 3/8-inch high-pressure connections and remove the filter
assembly.